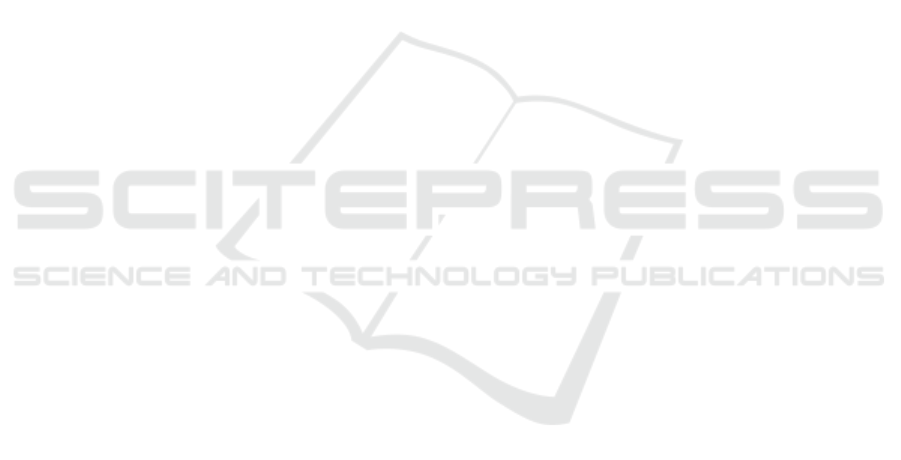
REFERENCES
Altun, O., Kepenek, R., Tasdemir, F., Akyurek, F., Akbu-
lut, C. T. M., Nuzumlali, O. L., and Inceturkmen, E.
(2017). Development of a fully programmable roic
with 15 μm pixel pitch for mwir applications.
Amber D. Fischer, T. V. Downes, R. L. (2007). Median
spectral-spatial bad pixel identification and replace-
ment for hyperspectral swir sensors.
Anderson-Sprecher, R. (1994). Model comparisons and r2.
The American Statistician, 48(2):pp. 113–117.
Celestre, R., Rosenberger, M., and Notni, G. (2016). A no-
vel algorithm for bad pixel detection and correction
to improve quality and stability of geometric mea-
surements. Journal of Physics: Conference Series,
772(1):012002.
David L. Perry, E. L. D. (1993). Linear theory of nonuni-
formity correction in infrared staring sensors. Optical
Engineering, 32:32 – 32 – 6.
Gade, R. and Moeslund, T. B. (2014). Thermal cameras and
applications: a survey. Machine Vision and Applicati-
ons, 25(1):245–262.
Godoy, S. E., Pezoa, J. E., and Torres, S. N. (2008). Noise-
cancellation-based nonuniformity correction algo-
rithm for infrared focal-plane arrays. Appl. Opt.,
47(29):5394–5399.
Isoz, W., Svensson, T., and Renhorn, I. (2005). Nonunifor-
mity correction of infrared focal plane arrays.
Jonah C. McBride, M. S. S. (2009). Improving scene-based
nonuniformity correction for infrared images using
frequency domain processing.
Kai, M., Zhan, S., Xiaodong, P., Yongsheng, W., and Wen-
bin, L. (2016). An interpolation method based on
two-step approach model for bad point in bayer color
image. In 2016 2nd IEEE International Conference on
Computer and Communications (ICCC), pages 599–
602.
Kumar, A. (2013). Sensor non uniformity correction algo-
rithms and its real time implementation for infrared
focal plane array-based thermal imaging system. De-
fence Science Journal, 63(6):589–598.
Liang, C., Sang, H., and Shen, X. (2014). Efficient scene-
based method for real-time non-uniformity correction
of infrared video sequences. Electronics Letters,
50(12):868–870.
Lin, Y. and Calarco, A. (1990). Offset, gain and bad pixel
correction in electronic scanning arrays. US Patent
4,920,428.
Milton, A. F., Barone, F. R., and Kruer, M. R. (1985). In-
fluence of nonuniformity on infrared focal plane array
performance. Optical Engineering, 24:24 – 24 – 8.
Ness, G., Oved, A., and Kakon, I. (2017). Derivative ba-
sed focal plane array nonuniformity correction. CoRR,
abs/1702.06118.
Schulz, M. and Caldwell, L. (1995). Nonuniformity cor-
rection and correctability of infrared focal plane ar-
rays. Infrared Physics & Technology, 36(4):763 – 777.
Shi, H., Zhang, Q., Qian, J., Mao, L., Cheng, T., Gao, J.,
Wu, X., Chen, D., and Jiao, B. (2009). Optical sensi-
tivity analysis of deformed mirrors for microcantilever
array ir imaging. Opt. Express, 17(6):4367–4381.
Vera, E., Meza, P., and Torres, S. (2011). Total variation ap-
proach for adaptive nonuniformity correction in focal-
plane arrays. Opt. Lett., 36(2):172–174.
Wang, M., Tsukamoto, T., and Tanaka, S. (2015). Uncooled
infrared thermal imaging sensor using vacuum-
evaporated europium phosphor. Journal of Microme-
chanics and Microengineering, 25(8):085001.
Young, S. S., Driggers, R. G., and Jacobs, E. L. (2008). Sig-
nal Processing and Performance Analysis for Imaging
Systems. Artech House, Inc., Norwood, MA, USA.
Yuan, X., Wan, W., and Zhao, M. (1995). New method for
nonuniformity correction of solid state image sensor.
Proc.SPIE.
VISAPP 2018 - International Conference on Computer Vision Theory and Applications
226