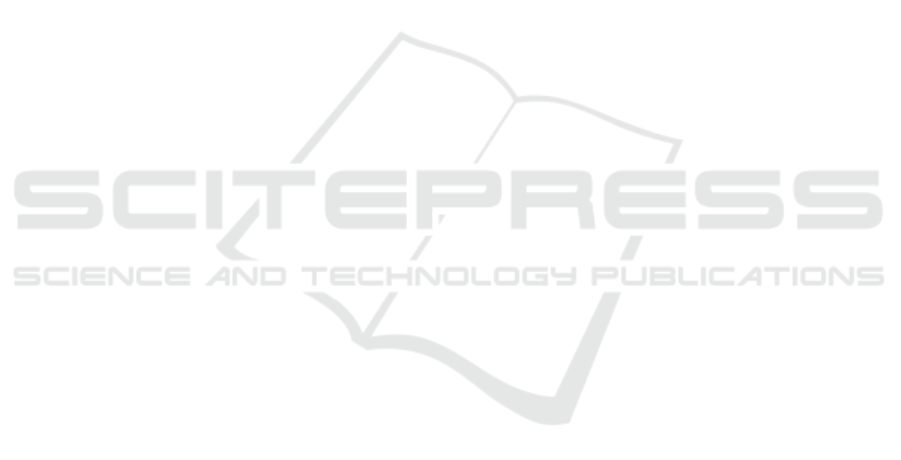
Bilkay, O., Anlagan, O., and Kilic, S. E. (2004). Job
shop scheduling using fuzzy logic. The Internatio-
nal Journal of Advanced Manufacturing Technology,
23(7-8):606–619.
Buzacott, J. A., Corsten, H., G
¨
ossinger, R., and Schneider,
H. (2013). Production planning and control: Basics
and concepts. Lehr- und Handb
¨
ucher der Betriebs-
wirtschaftslehre. Oldenbourg Verlag, M
¨
unchen.
Chen, K. J. and Ji, P. (2007). A genetic algorithm for dy-
namic advanced planning and scheduling (daps) with
a frozen interval. Expert Systems with Applications,
33(4):1004–1010.
Chen, X., Wen Lin, H., and Murata, T. (2012). Composite
dispatching rule design for dynamic scheduling with
customer-oriented production priority control. IEEJ
Transactions on Electrical and Electronic Engineer-
ing, 7(1):53–61.
Choi, S. H. and Wang, K. (2012). Flexible flow
shop scheduling with stochastic processing times: A
decomposition-based approach. Computers & Indus-
trial Engineering, 63(2):362–373.
Chongwatpol, J. and Sharda, R. (2013). Rfid-enabled
track and traceability in job-shop scheduling environ-
ment. European Journal of Operational Research,
227(3):453–463.
De Snoo, C. and Van Wezel, W. (2011). The intercon-
nectivity of planning and shop floor: Case description
and relocation analysis. In Behavioral operations in
planning and scheduling, pages 31–43. Springer Ber-
lin Heidelberg, Berlin, Heidelberg.
Ebrahimi, M., Fatemi Ghomi, S., and Karimi, B. (2014).
Hybrid flow shop scheduling with sequence depen-
dent family setup time and uncertain due dates. Ap-
plied Mathematical Modelling, 38(9-10):2490–2504.
Fayad, C. and Petrovic, S. (2005). A fuzzy genetic algo-
rithm for real-world job shop scheduling. In Innovati-
ons in applied artificial intelligence, volume 3533 of
Lecture Notes in Computer Science, pages 524–533.
Springer Berlin Heidelberg, Berlin, Heidelberg.
Ganschar, O. and Gerlach, S. (2013). Produktionsarbeit der
Zukunft - Industrie 4.0. Fraunhofer-Verl., Stuttgart.
Gao, K. Z., Suganthan, P. N., Chua, T. J., Chong, C. S., Cai,
T. X., and Pan, Q. K. (2015). A two-stage artificial bee
colony algorithm scheduling flexible job-shop schedu-
ling problem with new job insertion. Expert Systems
with Applications, 42(21):7652–7663.
Gao, K. Z., Suganthan, P. N., Pan, Q. K., Chua, T. J., Chong,
C. S., and Cai, T. X. (2016a). An improved artificial
bee colony algorithm for flexible job-shop scheduling
problem with fuzzy processing time. Expert Systems
with Applications, 65:52–67.
Gao, K. Z., Suganthan, P. N., Pan, Q. K., Tasgetiren, M. F.,
and Sadollah, A. (2016b). Artificial bee colony algo-
rithm for scheduling and rescheduling fuzzy flexible
job shop problem with new job insertion. Knowledge-
Based Systems, 109:1–16.
Gholami, M. and Zandieh, M. (2009). Integrating simula-
tion and genetic algorithm to schedule a dynamic flex-
ible job shop. Journal of Intelligent Manufacturing,
20(4):481–498.
Ghrayeb, O. A. (2003). A bi-criteria optimization: Minimi-
zing the integral value and spread of the fuzzy make-
span of job shop scheduling problems. Applied Soft
Computing, 2(3):197–210.
Gonz
´
alez-Neira, E. M., Garc
´
ıa-C
´
aceres, R. G., Caballero-
Villalobos, J. P., Molina-S
´
anchez, L. P., and Montoya-
Torres, J. R. (2016). Stochastic flexible flow shop
scheduling problem under quantitative and qualitative
decision criteria. Computers & Industrial Engineer-
ing, 101:128–144.
Graham, R. L., Lawler, E. L., Lenstra, J. K., and Kan, A.
(1979). Optimization and approximation in determi-
nistic sequencing and scheduling: A survey. In Dis-
crete optimization, volume 5 of Annals of Discrete
Mathematics, pages 287–326. North-Holland Pub. Co,
Amsterdam and New York and New York.
Gu, J., Gu, M., Cao, C., and Gu, X. (2010). A novel compe-
titive co-evolutionary quantum genetic algorithm for
stochastic job shop scheduling problem. Computers
& Operations Research, 37(5):927–937.
Gutenberg, E. (1971). Grundlagen der Betriebswirtschaft-
slehre: Die Produktion. Berlin, Heidelberg, New
York: Springer-Verlag.
Hamzadayi, A. and Yildiz, G. (2016). Event driven stra-
tegy based complete rescheduling approaches for dy-
namic m identical parallel machines scheduling pro-
blem with a common server. Computers & Industrial
Engineering, 91:66–84.
Hao, X., Lin, L., Gen, M., and Ohno, K. (2013). Ef-
fective estimation of distribution algorithm for sto-
chastic job shop scheduling problem. Procedia Com-
puter Science, 20:102–107.
Hauptvogel, A. (2015). Bewertung und Gestaltung von
cyber-physischer Feinplanung: Zugl.: Aachen, Techn.
Hochsch., Diss., 2015, volume 2015,6 of Ergebnisse
aus der Produktionstechnik Produktionssystematik.
Apprimus-Verl., Aachen, 1. edition.
He, W. and Sun, D.-h. (2013). Scheduling flexible job shop
problem subject to machine breakdown with route
changing and right-shift strategies. The Internatio-
nal Journal of Advanced Manufacturing Technology,
66(1-4):501–514.
Heinrich, B., Linke, P., and Gl
¨
ockler, M. (2015). Grundla-
gen Automatisierung. Springer Fachmedien Wiesba-
den, Wiesbaden.
H
¨
oll, A., R. C. and Stimming, C. (2015). Hochau߬sende
r
¨
uckmeldedaten. intelligente sensorik. In Ergebnis-
bericht des BMBF-Verbundprojektes ProSense, pages
51–56. Aachen: Apprimus Verlag.
Horng, S.-C., Lin, S.-S., and Yang, F.-Y. (2012). Evolutio-
nary algorithm for stochastic job shop scheduling with
random processing time. Expert Systems with Appli-
cations, 39(3):3603–3610.
Hußlein, T. and Breidbach, J. (2015). Anwendung und
anwendbarkeit von optimierungsalgorithmen in der
praxis. In Produktionsplanung und -steuerung, pages
227–239. Springer Gabler, Berlin.
Javadi, B., Saidi-Mehrabad, M., Haji, A., Mahdavi, I.,
Jolai, F., and Mahdavi-Amiri, N. (2008). No-wait
Meta Heuristics for Dynamic Machine Scheduling: A Review of Research Efforts and Industrial Requirements
199