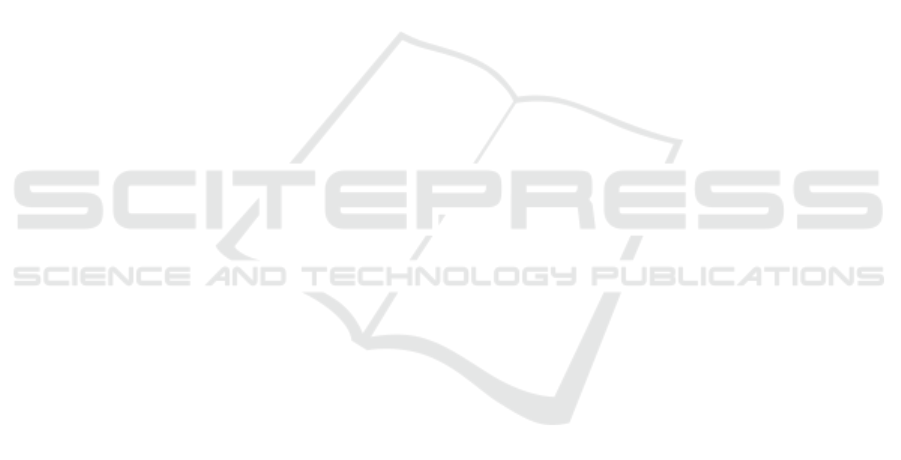
As you can see from (b) in Figure 2 and Figure 3 that when the distance of the nozzle inlet on the
side of the furnace to the top of the gasifier is 0.75m, the above undesirable phenomena weaken
evidently, the impact and interception of the nozzle jet flow on the side of the furnace on the main
flow of the nozzle jet on the top of the furnace become strong greatly, and the nozzle jet flow on the
side of the furnace dose not scour the wall of the furnace. However, the authors find out that the main
flow of the nozzle jet on the top of the furnace collides with the nozzle jet flow on the side of the
furnace without reaching the state of full development. In this way the jet flow from the various
nozzles will collide with each other after a very short time when they enter into the gasifier, which
will be disadvantageous for the nozzles to realize their sound atomization performance fully.
Meanwhile, when comparing (c) in Figure 2 and Figure 3, the recirculation zone formed around the
nozzle on the top of the furnace is relatively small because the distance of the nozzle inlet on the side
of the furnace to the top of the gasifier is very near. For gasifier of thermal operation, if the
recirculation zone around the nozzle on the top of the furnace is small, the volume of the air
entrainment of the surrounding high temperature gas by the nozzle jet flow on the top of the furnace
will be less, which is not good for the nozzle jet flow on the top of the furnace and the ignition and
burning in the collision area, and at the same time will reduce the stability of the ignition and
operation within the gasifier. So, the increase of the air entrainment of the surrounding high
temperature gas by the nozzle jet flow on the top of the furnace should be considered properly, for
which the most direct way is to increase the recirculation zone. When the distance of the nozzle inlet
on the side of the furnace to the top of the gasifier is 0.9m, the nozzle jet flow on the top of the
furnace collides with the nozzle jet flow on the side of the furnace when it’s fully developed. In this
way, the sound atomization performance of the nozzles on the top and both sides of the furnace can
be fully realized, and the time from the entering of the jet flow of the nozzle into the gasifier to the
collision is prolonged, which have provided precondition for the full development of jet flow,
increase the recirculation zone around the nozzle jet flow on the top of the furnace, strengthen the
nozzle jet flow on the top of the furnace, and increase the stability of the ignition and operation
within the gasifier. So, from the perspective of the distribution effect of the flow field, it’s
comparatively ideal when the distance of the nozzle inlet on the side of the furnace to the top of the
gasifier is 0.9m.
(a), (b), (c) in Figure 4 and Figure 5 are respectively the contour map of the turbulence intensity
distribution and turbulent kinetic energy distribution of the gasifier when the distances of the position
of the nozzle inlet to the top of the gasifier are 0.6m, 0.75m and 0.9m. As you can see from the
figures that when the distance is 0.6m, the turbulence intensity distribution and turbulent kinetic
energy distribution are apparently different from that of 0.75m and 0.9m. When the distance is 0.6m,
the nozzle jet flow on the side of the furnace dose not impact the internal flow field of the nozzle jet
flow on the top of the furnace; because the nozzle inlet on the side of the furnace is very near to the
top of the furnace, the position of the collision of the nozzle jet flow on the side of the furnace and on
the top of the furnace is just the position where the rigidity of the nozzle jet flow on the top of the
furnace are comparatively strong. In this case, the impact and interception effect of the nozzle jet
flow from the side on the jet flow from the top are not evident, and the kinetic energy of the flow
from the side of the furnace has been exhausted before it comes to intervene the internal flow field of
the nozzle jet flow on the top of the furnace, and thus the function of the nozzle jet flow on the side
of the furnace does not realize fully. However, the situation for the distances of 0.75m and 0.9m is
much better compared to 0.6. Especially when the distance of the nozzle inlet to the top of the
gasifier is 0.9, the kinetic energy of the flow from the side of the furnace are fully realized, the
impact and the interception of the nozzle jet flow on the top of the furnace are very evident, and the
area with comparatively intensified turbulent mixing strength becomes larger, all of which can be
seen from (c) in figure 4.9. So, from the perspective of the distribution of the turbulence intensity
distribution and turbulent kinetic energy distribution, it’s comparatively ideal when the distance of
Cold State Numerical Simulation of New Type Coal-water-slurry Gasifier
351