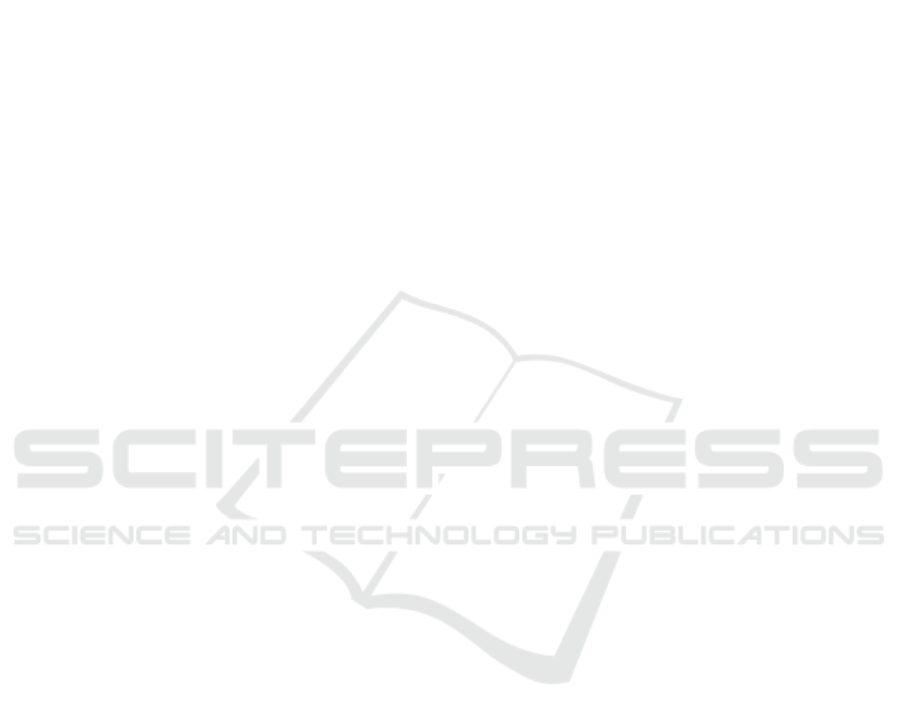
Friction Performance of SiCp/Cu Hybrid Materials with Compound
Additive
Yunlong Zhang, Wei Zhou
*
, Haifeng Zhang and Qingxiang Yang
Anyang institute of technology, Huang he street, Anyang city, P. R. China
Keywords: Cu matrix hybrid material, Rare earth oxides, Coefficient of friction
Abstract: Copper alloy material had excellent electrical and thermal characteristics, but its poor wear resistance and low
hardness limited its wider application. So it was necessary to improve wear resistance of copper alloy. In this
paper, compound additives La
2
O
3
/Al
2
O
3
/CeO
2
were introduced into SiCp/Cu composites and hot-press
sintering method was executed to synthesize SiCp/Cu composites. The influence of rare earth oxides on the
phase constitution, micro structure and coefficient of friction of SiCp/Cu composites were investigated.
1 INTRODUCTION
Metal composites were developed into prime
candidate as functional materials. Metal-ceramics
composites exhibited superior performance such as
high specific strength, high elastic modulus and wear
resistance. Copper alloy were utilized as functional
materials with high thermal electrical properties
(Wang, 2011). However, the poor wear resistance
limited wider engineering application. Some ceramic
particles were used as reinforcement, such as metal
carbides (WC, SiC, TiC), metal nitrides (TiN, Si
3
N
4
),
metal borides (ZrB
2
, WB, TiB
2
) and metal oxides
(Al
2
O
3
, ZrO
2
). SiC particles were utilized in the Cu
matrix considering the special properties of SiC
p
on
account of high hardness, good wear, low density
(Dhokey, 2008). So SiC
p
/Cu composites were
developed as functional material due to their
excellent electrical and thermal conductivity, good
wear resistance (Zhang, 2008). At present, more
reports on SiC
p
/Cu composites were widespread (Zhu,
2007). Copper-based composites reinforced with
15-35wt.% SiC were fabricated by mechanical
alloying, so an increase in milling time and SiC
content (up to 25 wt.%) lead to a higher hardness of
Cu matrix materials due to homogenization of
microstructure and refinement of reinforcing
particles (Perumal, 2015). The effect of SiC content
and particle size on the density, hardness and
electrical conductivity were investigated (Peng,
2012). The structure and particle size of copper based
composite reinforced with a high content (15-35wt%)
of silicon carbide and prepared by mechanical
alloying in the high energy planetary mill
(Prosviryakov, 2013). However, the reports about
addition of rare earth oxides to SiC/Cu composites
were relatively scarce. In this work,
La
2
O
3
/Al
2
O
3
/CeO
2
were introduced into SiC
p
/Cu
composite. The density, phase constitution, micro
structure and coefficient of friction of SiC
p
/Cu
composites were investigated.
2 EXPERIMENTAL PROCESS
The initial materials were domestic copper powders
(D
50
=38µm), SiC powder (D
50
=38.5µm), Al
2
O
3
powders (D
50
=0.5µm) and La
2
O
3
powders
(D
50
=0.5µm). The initial powders were mixed in
accordance with the composition ratio designed in
Table 1 in which mass ratio of Al
2
O
3
and La
2
O
3
was
1:3. The content of CeO
2
was about 2wt.%. For
comparison specimen S5 without compound
additives was also studied. The initial powders were
mixed by ball-milling machine. The milling was
320rpm for 8h. Before sintering process, the mixture
was cold pressed into a cylindrical compact in a die of
40mm in diameter with pressure of 200MPa. SiC
p
/Cu
composites were sintered in a graphite die at 840℃
for 1h in hot-press sinter furnace with argon gas and
heating rate was about 30℃/min. Density measure
was carried out according to Archimedes principle.
Microstructure of composites was observed by SEM.
Phases constitution were analysized by X-ray(Bruker
Zhang, Y., Zhou, W., Zhang, H. and Yang, Q.
Friction Performance of SiCp/Cu Hybrid Materials with Compound Additive.
DOI: 10.5220/0008186100930096
In The Second International Conference on Materials Chemistry and Environmental Protection (MEEP 2018), pages 93-96
ISBN: 978-989-758-360-5
Copyright
c
2019 by SCITEPRESS – Science and Technology Publications, Lda. All rights reser ved
93