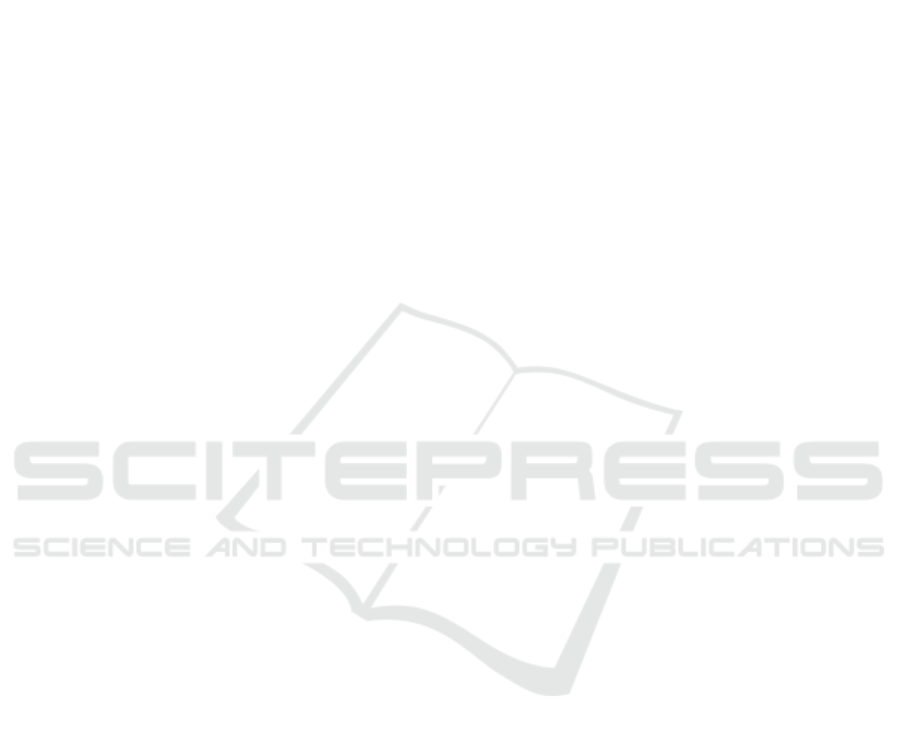
Stress Analysis of Helideck Structures on Offshore Patrol Vessel
Achmad Zubaydi
1
, Septia Hardy Sujiatanti
1
and Refdi
1
1
Department of Naval Architecture, Faculty of Marine Technology, Institut Teknologi Sepuluh Nopember, Surabaya,
Indonesia
Keywords: Helideck, Offshore Patrol Vessel
Abstract: The helicopter deck structure plan should be able to guarantee a structure with a stress not exceeding the
permissible stress. A helideck structure analysis is carried out based on the loading conditions obtained from
helicopter landing variations to calculate maximum load, maximum stress, and deformation. The results
obtained are von misses stress and deformation values for various loading condition. The maximum stress
generated under condition 1 is 109 MPa with a deformation value of 2.015 mm. The maximum value of the
maximum stress for condition 2 is 135 MPa with a deformation value of 2,069 mm. The maximum value of
the maximum stress for condition 3 is 174 MPa with a deformation value of 4,161 mm. The maximum value
of the maximum stress for condition 4 is 223 MPa with a deformation value of 5,969 mm. It can be concluded
that condition 1 is the most optimum helicopter landing conditions with the lowest stress and deformation
among all load conditions.
1 INTRODUCTION
Republic of Indonesia Marine Security Agency
(BAKAMLA RI) requires a large and sophisticated
fleet of patrol boats to defend the Indonesian border.
One of the sophistication is helideck for global
monitoring. The helideck construction planning is to
make a construction that has a stress level at the limits
permitted. Planning a helideck construction must be
able to guarantee a structure with a stress no more
than the clearance stress. Helideck construction must
be designed to avoid excessive elastic deformation
which can result in changes in geometry due to the
load received. These parts must be measured
appropriately for the actual or charged styles.
To ensure the helideck can be used safely and
function properly, it is necessary to conduct research
as an effort to identify any hazards that might
threaten, the main purpose is to verify the strength of
the helideck structure when subjected to a load with
the condition of the helicopter remaining on the
runway and landing. The design of the helideck must
be able to anticipate the occurrence of emergency
landings by helicopters. Emergency landings can be
located around the helideck area, inside or outside the
helipad.
This research was conducted to calculate the
maximum loading value, maximum stress,
deformation by using finite element method.
Calculating the level of security in the helideck
construction, calculating the level of safety (safety
factor) in the construction of the helideck and
knowing the most critical components and need to get
more attention.
2 LITERATURE REVIEWS
Helicopter deck known as helideck is a landing area
for specially built helicopters on ships including all
structures, firefighting equipment and other facilities
needed for safe operation of helicopters. Other
facilities include refueling facilities and hangar
facilities. Helicopter landing areas must be designed
for emergency helicopter landings. The helicopter
landing area must be on the topmost deck and have a
large manouver zone, and most importantly the
helicopter landing area must be close to the side of the
ship.
Helideck is a deck of a ship or an offshore
structure built for landing or taking off a helicopter as
shown in Figure 1. Landing areas must have the
widest possible area to provide safe access to
helicopters upon landing (DNV, 2010).
106
Zubaydi, A., Sujiatanti, S. and Refdi, .
Stress Analysis of Helideck Structures on Offshore Patrol Vessel.
DOI: 10.5220/0008375501060110
In Proceedings of the 6th International Seminar on Ocean and Coastal Engineering, Environmental and Natural Disaster Management (ISOCEEN 2018), pages 106-110
ISBN: 978-989-758-455-8
Copyright
c
2020 by SCITEPRESS – Science and Technology Publications, Lda. All rights reserved