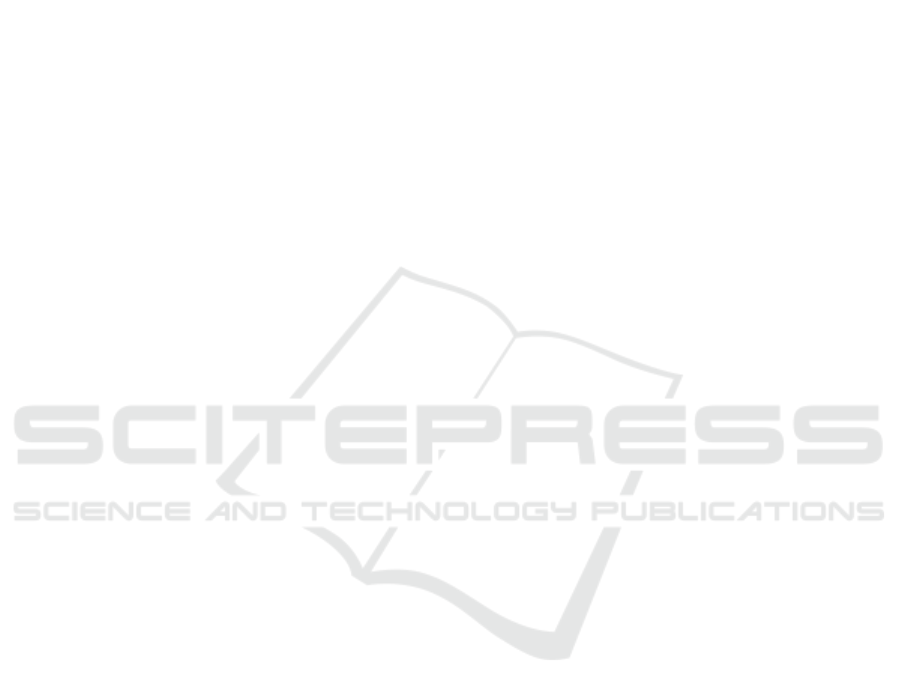
Effects of Longitudinal Shifts of Centre of Gravity on Ship Resistance: A
Case Study of a 31 M Hard-Chine Crew Boat
Ketut Suastika
1
∗
, Soegeng Riyadi
1
, I Ketut Aria Pria Utama
1
, and Xuefeng Zhang
2
1
Department of Naval Architecture, Institut Teknologi Sepuluh Nopember (ITS), Surabaya 60111, Indonesia
2
School of Marine Science and Technology, Tianjin University, Tianjin, China
Keywords:
CFD, Longitudinal Shift of Centre of Gravity, Hard-chine Crew Boat, Ship Resistance, Wave Pattern.
Abstract:
Computational fluid dynamics (CFD) simulations were performed to study effects of the longitudinal shifts
of centre of gravity (from the designed one) on ship resistance. Such a shift of centre of gravity has been
frequently observed in practice. This can occur, for example, due to inaccuracies in size and weight estimations
of ship components in the design stage and imperfections in bending, welding and assembly processes in the
production stage. For the reference case where there is no centre-of-gravity shift, the CFD results were verified
using data obtained from towing-tank experiments and using results from the Savitsky’s model. Results of
analysis show that for relatively low Froude numbers, a forward shift of centre of gravity results in a decrease
of ship resistance while a backward shift results in an increase of ship resistance. The opposite is true for
relatively high Froude numbers. Because the boat is designed to operate in relatively high Froude numbers
(Fr ¿ 0.7), a backward shift of centre of gravity is more favourable.
1 INTRODUCTION
In ship design, one of the owner requirements is the
ship speed. Based on the owner requirements, a ship
designer decides on the hull form and ship principal
particulars. So, ship speed enters the ship design pro-
cess in the first stage (EVANS, 1959). Estimations of
ship resistance and the required powering then follow.
In the first instance, the ship resistance is esti-
mated based on the full-load condition. However, a
ship is not always in full-load condition during its op-
erations. A shift of centre of gravity, particularly in
the longitudinal direction, may take place if the load-
ing condition changes. It has been observed that this
longitudinal shift of centre of gravity affects the ship
resistance (Kazemi and Salari, 2017).
A shift of centre of gravity, relative to the designed
one, can also take place during the production pro-
cess of the ship. This can happen due to, for example,
oversize of main engine, inaccuracy in weight estima-
tions of generator, structural components etc. In addi-
tion, a shift of centre of gravity can also occur due to
imperfections in bending, welding and assembly pro-
cesses (Takechi et al., 1998).
Figure 1 illustrates the production process of a
hard-chine crew boat in PT. Orela Shipyard, Ujung
Pangkah, Gresik, Indonesia and Figure 2 shows the
construction part near the bow. The boat in produc-
tion as shown in Figure 1 and 2 was made of alu-
minium. In such a production process, imperfections
as described above can occur, which result in a (lon-
gitudinal) shift of centre of gravity relative to the de-
signed one. Although longitudinal shifts of centre of
gravity have frequently been observed in practice, its
effects on ship resistance have insufficiently been ex-
plored.
The purpose of the present study is to investigate
effects of the longitudinal shifts of centre of gravity
on ship resistance. For that purpose, a hard-chine
crew boat, designed and built by PT. Orela Shipyard,
as shown in Figure 1 and 2, is considered as a case
study. The ship principal-particulars are summarized
in Table 1.
Computational fluid dynamics (CFD) simulations
were performed and the results for the reference case
without shift of centre of gravity were verified us-
ing data obtained from towing-tank experiments and
using results from the Savitsky’s model (Savitsky,
1964).
The research method is further elaborated in Sec-
tion. 2. The results and discussion are presented
in Section 3. The paper ends with conclusions, pre-
sented in Section 4.
Suastika, K., Riyadi, S., Utama, I. and Zhang, X.
Effects of Longitudinal Shifts of Centre of Gravity on Ship Resistance: A Case Study of a 31 m Hard-chine Crew Boat.
DOI: 10.5220/0008550801450152
In Proceedings of the 3rd International Conference on Marine Technology (SENTA 2018), pages 145-152
ISBN: 978-989-758-436-7
Copyright
c
2020 by SCITEPRESS – Science and Technology Publications, Lda. All rights reserved
145