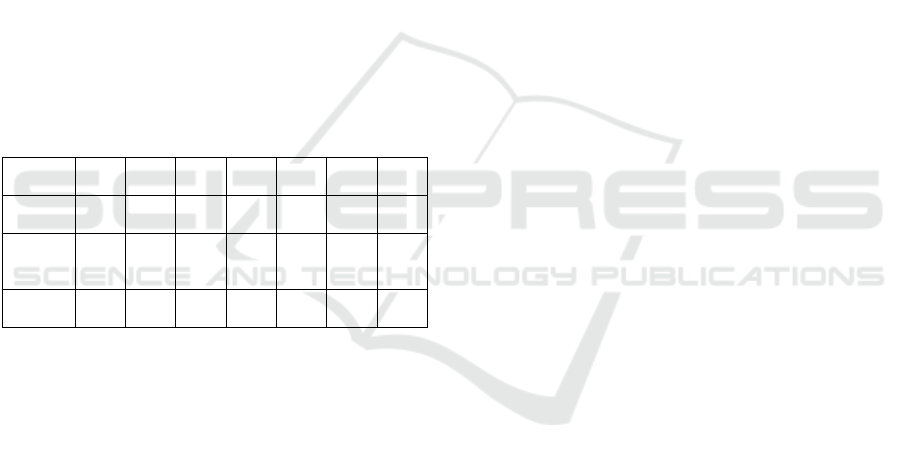
problem in CNN model training, the CycleGAN
model is applied to generate a sufficiently large
dataset of negative samples from a very limited
number of real saw-mark image patches. Due to the
indiscriminate patterns between the regular random
crystal grains and the saw-mark in a small image
patch, the detected saw-mark region in a full-sized
solar image may not be completely detected. The
postprocessing with the horizontal projection in the
segmented binary image can effectively identify the
presence/absence of a saw-mark in the inspection
image. The preliminary experimental results indicate
the proposed method can effectively detect various
saw-mark defects including black line, white line and
impurity in solar wafer surfaces.
The proposed method currently focuses on saw-
mark detection in multicrystalline solar wafers. In the
future, the use of the CycleGAN or GAN-variant
models to create various defect types such as
contaminants, particles and fingerprints and training
the CNN model for multiple-classes classification are
worthy of further investigation.
Table 1: Recognition rates with varying number of training
samples for the CNN models.
REFERENCES
Z. Fu, Y. Zhao, Y. Liu, Q. Cao, M. Chen, J. Zhang, J. Lee,
2004. “Solar cell crack inspection by image
processing,” Int’l. Conf. on Business of Electronic
Product Reliability and Liability, Shanghai, China, pp.
77–80.
M. A. Ordaz, G. B. Lush, 2000. “Machine vision for solar
cell characterization,” Proc. of SPIE, San Diego, CA,
USA, pp. 238–248.
M. Pilla, F. Galmiche, X. Maldague, 2002. “Thermographic
Inspection of Cracked Solar Cells,” Proc. of SPIE,
Seattle, WA, USA, pp. 699–703.
D. M. Tsai, C. C. Chang, S. M. Chao, 2010. “Micro-crack
inspection in heterogeneously textured solar wafers
using anisotropic diffusion,” Image and Vision
Computing, vol. 28, pp. 491–501.
I. Ar, Y. S. Akgul, 2008. “A generic system for the
classification of marble tiles using Gabor filters,”
International Symposium on Computer and Information
Sciences, Istanbul, pp. 1–6.
X. Xie, M. Mirmehdi, 2005. “Localising surface defects in
random color textures using multiscale texem analysis
in image eigenchannels,” IEEE Int’l. Conf. on Image
Processing, Genoa, Italy, pp. III–1124–7.
X. Xie, M. Mirmehdi, 2007. “TEXEMS: Texture exemplars
for defect detection on random textured surfaces,” IEEE
Transactions on Pattern Analysis and Machine
Intelligence, vol. 29, pp. 1454–1464.
W.-C. Li, D.-M. Tsai, 2011. “Automatic saw-mark
detection in multicrystalline solar wafer images,” Solar
Energy Materials and Solar Cells, vol. 95, pp. 2206-
2220.
Y. LeCun, Y. Bengio, G. Hinton, 2015. “Deep learning,”
Nature, vol. 521, pp. 436-444.
D. Soukup, R. Huber-Mork, 2014 . “Convolutional neural
networks for steel surface defect detection from
photometric stereo images, Intl. Symposium on Visual
Computing, pp. 668-677.
Y. Li, W. Zhao, J. Pan, 2017. Deformable patterned fabric
defect detection with Fisher criterion-based deep
learning,” IEEE Trans. Automation Science and
Engineering, vol. 14, pp. 1256-1264.
Y.-J. Cha, W. Choi, O. Buyukozturk, 2017. “Deep learning-
based crack damage detection using convolutional
neural networks,” Computer-aided Civil and
Infrastructure Engineering, vol. 32, pp. 361-378.
X. Gibert, V. M. Patel, R. Chellappa, 2017. ”Deep multitask
learning for railway track inspection,” IEEE Trans.
Intelligent Transport. Systems, vol. 18, pp. 153-164.
J.-Y. Zhu, T. Park, P. Isola, A. Efros, 2017 . “Unpaired
image-to-image translation using cycle-consistent
adversarial networks,” arXiv:1703.10593v2, 5 Oct..
A. Krizhevsky, L. Sutskever, G. Hinton, 2012. “ImageNet
classification with deep convolutional neural
networks,” Advances in Neural Information Processing
Systems 25 (NIPS).
I. Goodfellow, J. Pouget-Abadie, M. Mirza, B. Xu, D.
Warde-Farley, S. Ozair, A. Courville, Y. Bengio, 2014.
“Generative adversarial nets,” Advances in Neural
Information Processing Systems 27 (NIPS).
T. Zhou, P. Krahenbuhl, M. Aubry, Q. Huang, A. A. Efros,
2016. “Learning dense correspondence via 3d-guided
cycle consistency,” CVPR, pp. 117-126.
Chawla, N. V., Bowyer, K. W., Hall, L. O., and
Kegelmeyer, W. P. 2002. SMOTE: synthetic minority
over-sampling technique. Journal of Artificial
Intelligence Research, 16, 321-357.
Yen, S. J., and Lee, Y. S. 2009. Cluster-based under-
sampling approaches for imbalanced data distributions.
Expert Systems with Applications, 36, 5718-5727.
VISAPP 2019 - 14th International Conference on Computer Vision Theory and Applications
240