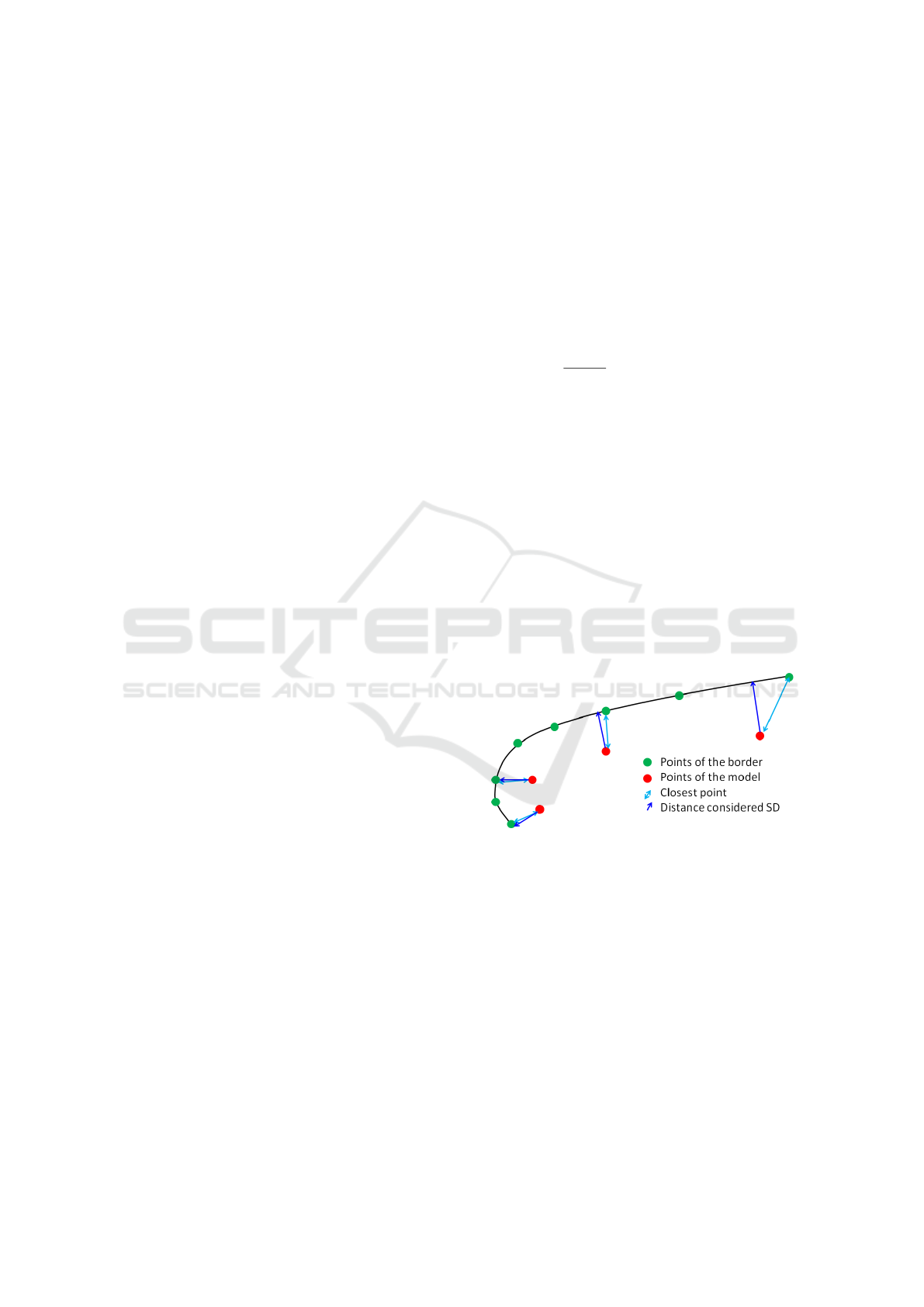
text. Qualitative and quantitative results are given. Fi-
nally section 5 concludes this paper.
2 REGISTRATION
The registration literature is very rich and offers many
different registration methods. Interesting surveys can
be found in: (Zitova and Flusser, 2003) (Sotiras et al.,
2013). We focus on the techniques relevant to our ap-
plication. Our model contains only the boundaries of
the object’s components and the visual appearance of
the inner parts is unknown. Thus image-based regis-
tration techniques are not suitable for our application.
Also the object is made of nearly incompressible
material and suffers only large scale deformations.
Thus, the inner parts move coherently with the object
boundary. Therefore we perform a shape registration
between the 2D model and the object external bound-
ary, and then apply the computed deformation to the
entire model. The same strategy is used by Peterlik
(Peterl
´
ık et al., 2017).
Our aim is then to register the model 2D shape
to shape of the manufactured object. Because of the
flexible nature of our objects, we need a non-rigid 2D
shape registration. Many methods exist in the litera-
ture for this purpose.
Among them there are many well known methods
such as the ICP (Iterative Closest Point) method in-
troduced par Besl and McKay (Besl et al., 1992), but
even its variants later developed (Rusinkiewicz and
Levoy, 2001) (Pomerleau et al., 2013) are inappropri-
ate for cases where the sampling step is not uniform.
This is the case in our application, because the model
is discretized so that there are more points in areas
of strong curvature while the object boundary is regu-
larly sampled according to the resolution of the im-
age acquisition device. Also it is very sensitive to
the initialization step. Another widespread method
is the Coherent Point Drift (CPD) algorithm, (My-
ronenko and Song, 2010) (Myronenko et al., 2007).
It is a probabilistic method, for both rigid and non-
rigid point set registration that considers the align-
ment of two point sets as a probability density esti-
mation problem.
The method developed by Rouhani (Rouhani and
Sappa, 2012) is particularly suitable for our purpose.
Indeed, it can cope with the not even discretization
step of the model’s border. Also it exploits a quadratic
distance approximation which allows each iteration of
the algorithm to be linearly solved. Hence, the regis-
tration process has a fast convergence. Because of
those reasons we choose to use Rouhani’s method.
2.1 Principle of Rouhani’s Registration
Let us describe the Rouhani’s registration princi-
ple introduced in (Rouhani and Sappa, 2012). Let
S = {s
i
}
N
s
1
be the set of data points of the model shape
and C = {c
i
}
N
c
1
the points of the object boundary. The
registration is done by minimizing an error term in an
iterative process. This error relies on the sum of the
distance of points s
i
belonging to the model, to the
border of the object C:
SD(s
i
,C) =
d
i
d
i
− ρ
j
[(s
i
− c
j
)
T
T
j
]
2
+ [(s
i
− c
j
)
T
N
j
]
2
(1)
with s
i
the considered point belonging to the
model, c
j
the closest point to s
i
belonging to C, T
j
and N
j
, the unit tangent and outer normal at c
j
, d
i
,
the signed distance between s
i
and c
j
, ρ
j
, the curva-
ture radius at s
i
.
The use of this distance makes this registration
method it suitable for a different number of points on
registered shapes. Figure 2 shows an illustration of
the considered distance: In low curvature zones the
considered distance is close to the normal distance to
the shape, and so the minimizing process is not af-
fected by the different number of points. Whereas
in high curvature zones, the considered distance is
equivalent to the euclidean one.
Figure 2: Illustration of the considered distance.
A squared control lattice, P, is defined and its de-
formation, L,is regularized by a global tension term ,
T (P), measured by its curvature over the whole do-
main:
T (P) =
Z Z
XY
[kL
xx
k
2
+ 2kL
xy
k
2
+ kL
yy
k
2
]dxdy (2)
with L, the vector field representing the deforma-
tion of the control lattice.
In each iteration, we optimize the deformation
field L in order to minimize the error E:
E = λT(P)+
N
s
∑
i=1
SD(L(s
i
),C) (3)
Non-rigid Shape Registration using Curvature Information
335