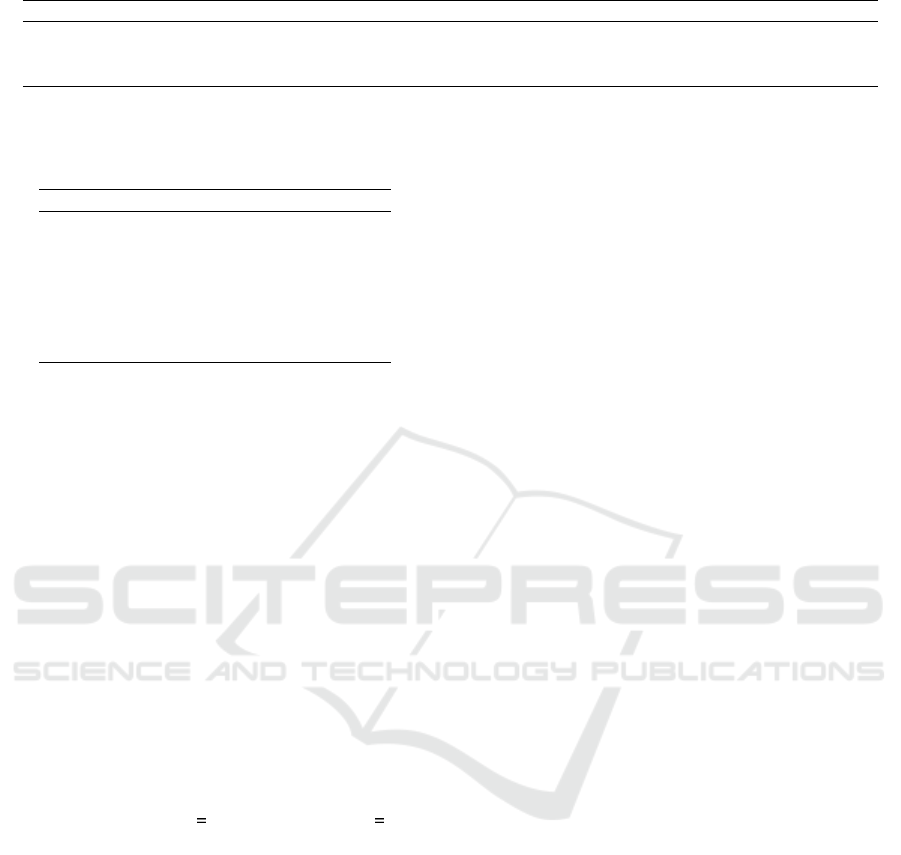
Table 1: Overview of state-of-the-art methods with regards to accessibility and the number of dials involved in the work.
J. Chi X. Ye C. Zheng M. Yi B. Sun H. Jiale B. Yang Q. Wang Proposed
No. of Dials 2 1 1 1 1 1 8 1 10
Open Source No No No No No No No No Yes
Public Data No No No No No No No No Yes
Table 2: Classification and error rate of the proposed met-
hod when processing the seven test videos.
Hit Miss µ [rad] σ [rad]
test1 11811 0 0.02 0.02
test2 967 1253 -0.47 1.28
test3 1801 0 -0.42 0.39
test4 1111 0 0.08 0.32
test5 451 0 -0.12 0.39
test6 347 704 -6.07 0.56
test7 571 2 -0.13 0.61
7 CONCLUSION
A method to automatically digitize analog circular
gauges using computer vision is presented with an ap-
plication example of a video recording of a pressure
gauge translated into a digital time series.
The method is based on segmenting objects in
each frame using Gaussian adaptive mean threshol-
ding and subsequently classifying the objects using
probability distributions estimated with the unsuper-
vised learning method Expectation Maximization.
The output of the algorithm is an estimated angle of
the pointer object, which is determined using PCA.
Recordings of seven pressure gauges, mounted on
waste water pumping stations, have been processed
by the algorithm. The mean and standard deviation of
the angle error are calculated for each of the videos
with the best case of µ 0.02 radians and σ 0.02
radians.
However, in three of the recordings, significant er-
rors are present. In test2 and test6 the bezel is made
from a reflective material, which makes it difficult to
segment objects properly with the proposed method
due to reflections. In another case, a problem is iden-
tified where the angle of the pointer is miscalculated
by ◦π radians due to motion blur.
The shortcomings that have been uncovered in the
tests are related to specific scenarios, which should be
taken into consideration during the next iteration of
the project. Generally, the results are very promising
and there is a great potential in the proposed parame-
tric classification method.
The source code is published at (Lauridsen and
Grassmé, 2018a) and the test and training data is pu-
blished at (Lauridsen and Grassmé, 2018b).
8 FUTURE WORK
The current system only processes a single frame at
a time, neglecting the benefits that might arise from
utilizing data from neighbouring frames. As an ex-
ample, to achieve better estimates for the circle, cen-
ter or for more accurate scale creation the temporal
neighboring data could be utilized. This could also be
used to reduce the errors introduced by motion blur,
where the angle is incorrectly determined by the blunt
end of the pointer.
Exploring other features, higher feature spaces or
other compositions could possibly increase the accu-
racy and make the proposed solution more robust.
The training data could also be more diverse in order
to better generalize to different types of dials. Lastly,
the level of automation can be improved by recogni-
zing the dial numbers and associating those numbers
to the scale marks.
REFERENCES
Alegria, F. C. and Serra, A. C. (2000). Computer vision
applied to the automatic calibration of measuring in-
struments. Measurement, 28(3):185 – 195.
Bishop, C. M. and Nasrabadi, N. M. (2007). Pattern Recog-
nition and Machine Learning. Journal of Electronic
Imaging, 16(4):049901.
Crawford, J. (1983). A non-iterative method for fitting ci-
rcular arcs to measured points. Nuclear Instruments
and Methods in Physics Research, 211(1):223–225.
Gellaboina, M. K., Swaminathan, G., and Venkoparao, V.
(2013). Analog dial gauge reader for handheld devi-
ces. In 2013 IEEE 8th Conference on Industrial Elec-
tronics and Applications (ICIEA). IEEE.
Jiale, H., En, L., Bingjie, T., and Ming, L. (2011). Reading
recognition method of analog measuring instruments
based on improved hough transform. In IEEE 2011
10th International Conference on Electronic Measu-
rement Instruments, volume 3, pages 337–340.
Jiannan Chi, Lei Liu, J. L. Z. J. G. Z. (2015). Machine
vision based automatic detection method of indicating
values of a pointer gauge. In Mathematical Problems
in Engineering, Article ID 283629, volume 2015.
Lauridsen, J. S. and Grassmé, J. G. (2018a). Bit-
bucket pressure gauge reader source code.
https://bitbucket.org/aauvap/pressure-gauge-reader
[Link].
Reading Circular Analogue Gauges using Digital Image Processing
381