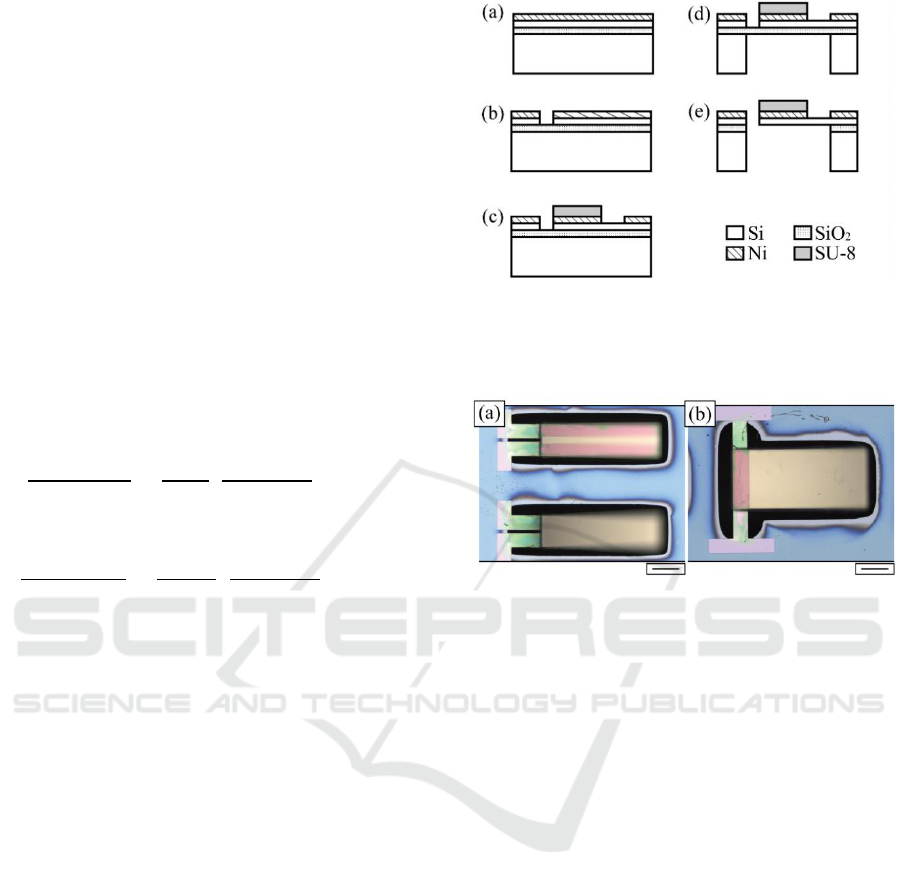
where, G
cell
and G
sub
are shear modulus of the cell and
the cell culture substrate.
To apply bending or torsion stimulus to cells,
which cultured on sub-mm area, we utilized magnetic
anisotropy. By patterning a soft magnetic material on
beam, bending or torsion deformation can be obtained
as shown in Figure 1. The inclination of the magnetic
material is tuned by an external magnetic field
applied perpendicularly to the microstructure. By
calculating an equation about the magnetic torque and
the torque generated by elastic deformation of the
beam, magnitude of bending or torsion stimulus
against an external magnetic field is obtained. In the
case of rectangular beam, the equation is expressed as
(Iwase et al., 2005; Roark et al., 1989),
for bending stimulus and,
for torsion stimulus. Where, η is an angle of torsion
par unit length. V
mag
and M
s
are the volume and the
saturation magnetization of magnetic material,
respectively. L
sub
and W
sub
are length, and width of the
cell culture substrate.
3 FABRICATION AND
EXPERIMENTAL RESULT
We fabricated the microstructure. To decide detail
dimensions, we targeted C2C12 as an example. We
estimated the length of C2C12 on substrate about 100
μm. Therefore, the size of deforming substrate was set
100 μm in length and 50 μm in width. To fabricate the
microstructure with size of micro order, we utilized
silicon (Si) with sub-micron thickness as the substrate.
Si is suited to microfabrication and fabricate free
standing structure like Figure 1 easily. In the case of
C2C12, assuming that the thickness is 1μm, on 270-
nm Si substrate, y
b
= 635 nm and y
t
= 635 nm from
Equations (2) and (4). Therefore, we obtain ε
bottom
/ε
top
≈ 0.12 and τ
bottom
/τ
top
≈ 0.12, respectively.
Fabrication process is shown in Figure 4. In the
fabrication process, silicon-on-insulator (SOI) wafer
was used. The thickness of the device Si layer, box
layer, and handle Si layer of the SOI wafer were 270
Figure 4: Cross-sectional diagrams of the fabrication
process. (a) Sputtering Ni layer. (b) Etching Ni and device-
Si layer. (c) Etching Ni layer and pattern SU-8 layer. (d)
Etching handle-Si layer. (e) Etching SiO
2
layer.
Figure 5: Images of fabricated microstructures. (a) The
microstructure to apply bending stimulus. (b) The
microstructure to apply torsion stimulus. Scar bars, (a) and
(b): 100 μm.
nm, 200 nm, and 300 μm, respectively. First, nickel
(Ni) layer with the thickness of 200 nm was sputtered
on the SOI wafer as a magnetic material (Figure 4 (a)).
Ni has a high saturation magnetization (M
s
= 0.6 T).
Then, the Ni layer was patterned using
photolithography, and the device Si layer was etched
with inductively-coupled-plasma reactive-ion etching
(ICP-RIE) using the Ni layer as a mask (Figure 4 (b)).
After that, the Ni layer was patterned again to remove
the Ni layer from the surface of cell culture region and
a negative photoresist (SU-8) was coated and
patterned on the Ni layer (Figure 4 (c)). We used SU-
8 to prevent a bending of beam, which is caused by a
strain mismatch between the Si layer and the Ni layer.
Then, the handle Si layer was patterned and etched
with ICP-RIE (Figure 4 (d)). Finally, the structure
was released by etching the box layer using HF
vapour (Figure 4 (e)). Fabricated microstructure is
shown in Figure 5. To compare with Equations (5)
and (6), we fabricated some microstructures with
different value of V
mag
by designing the width of Ni
layer.
We actuated the fabricated microstructures.
Figure 6 (a) shows the image of the experimental
Design of Microstructure for Stimulating Mechanical Torque to Cells
217