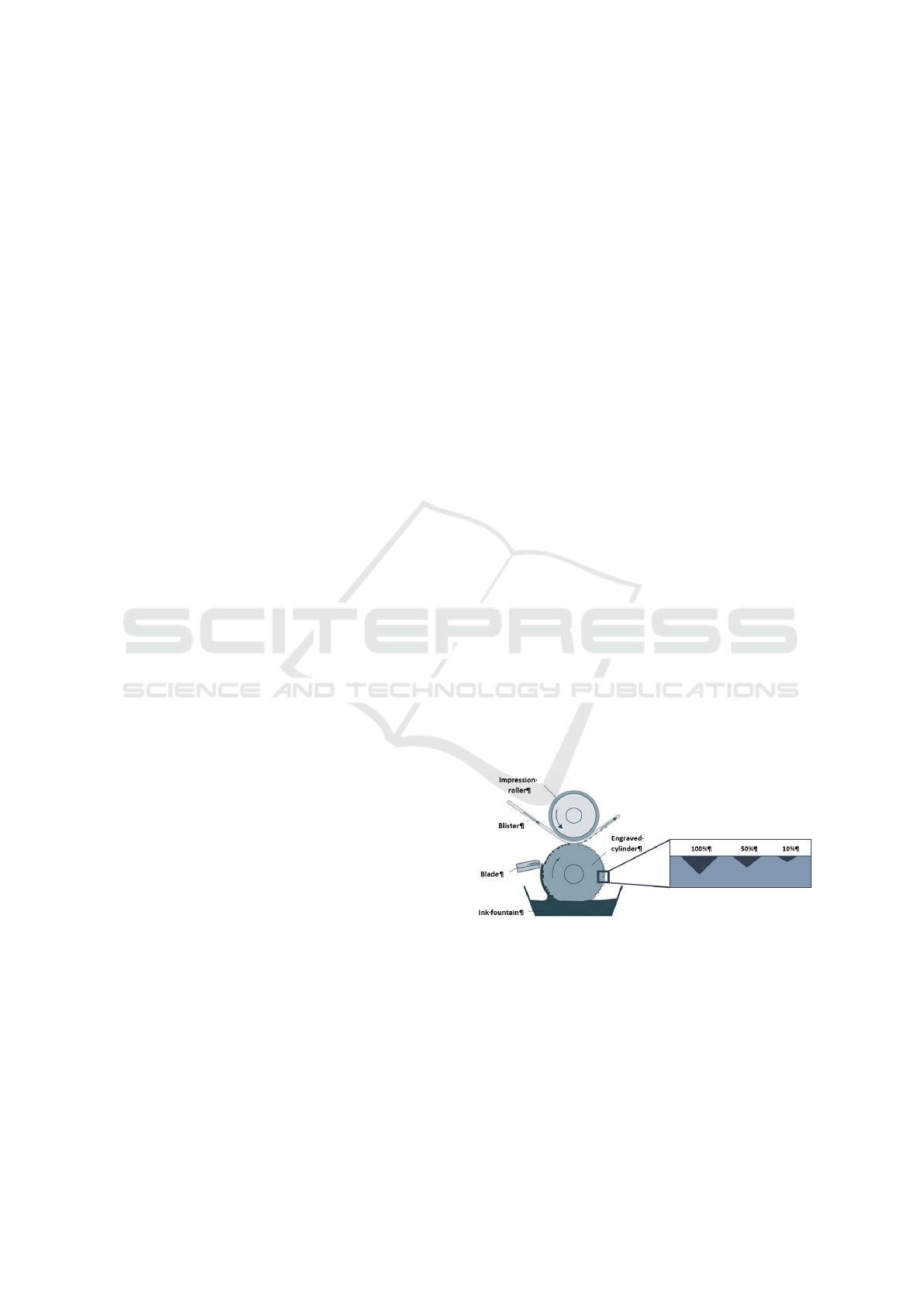
and packaging authentication, the research and deve-
lopment of more efficient techniques or of the exten-
sion of their application domain is a hot topic in aca-
demia and industry. While developing the novel se-
curity elements to fight against packaging counterfei-
ting, the following requirements might be taken into
account: 1) easy integration and generation proces-
ses, 2) low cost, 3) use of standard printing process, 4)
fast and automatic verification process, 5) use of com-
mon devices for verification (office scanners, smartp-
hones), 6) reliable verification by any user, 7) good
level of global security and strong anti-fraud ability.
The development of copy sensitive graphical co-
des can satisfy all the items above. These codes are
based on the use of measurable but not duplicable
physical characteristics (Goldman, 1983). Today we
can find numerous security elements that use measu-
rable but not duplicable physical characteristics and
that are sensitive to duplication attack. However, all
these elements have been developed for packaging or
documents that use the white uncoated/coated paper
and high resolution printing (from 600 dpi till 2400
dpi). Additionally, the authentication process is pro-
vided using high resolution scanners (from 600 dpi
till 4200 dpi).
We aim at developing security elements for pro-
tection of medicine packaging that are produced using
rotogravure printing on aluminum foils. To our kno-
wledge, there does not exist any tested solution for
such printing process and such type of support. The
well-understanding and characterization of the prin-
ting process is a crucial, preliminary step before deve-
loping efficient security elements. Therefore, the aim
of this paper is to study the characteristics of rotogra-
vure printing process and to identify several possible
paths for authentication of such packaging.
The paper is organized as follows. We introduce
the rotogravure printing technique which is world-
wide used for medicine blister foils production in
Section 2. Then we discuss some features of the ro-
togravure process in Section 2.2 that can be useful
to fight the increasing number of counterfeit medi-
cine products. We present the result of a preliminary
study of such a process, extended to foils in Section 3,
and discuss some promising outlooks for medicine
authentication in Section 4. Finally, we conclude in
Section 5.
2 ROTOGRAVURE PRINTING
CHARACTERIZATION
Rotogravure printing produces high-quality images
with intense rich colors using primary colors such as
CMYK. Each primary color is printed by one pass
through the press. Therefore, it is often used for high-
volume printing such as advertising pieces, magazi-
nes, catalogs and packaging.
2.1 Printing Process
Rotogravure is an intaglio printing process, where the
image is cut or etched below the surface. Rotogravure
printing has its pros and cons. The positive points are
long lifetime of printing cylinder (> 1 million copies),
variable printing formats, front- and backside printing
on one time, different printing primary colors, diffe-
rent materials, high printing quality, simple printing
principle. The negative points are costly cylinder en-
graving process and sloven based colors.
The rotogravure printing process uses a metal cy-
linders with an image engraved on it in the form of a
pattern with enclosed 3D cells. The cylinder radius is
determined by the final size of the page and repeat of
the design.
The cylinders are covered by cooper as it is soft
and pliable material easy to engrave. The copper layer
is only 80 microns thick. Before engraving, the cop-
per surface is automatically polished. It removes any
imperfections and smoothed out the cylinder. Polis-
hing also adds a roughness to the surface so it can
retain the ink that will lubricate the cylinder.
An artwork needs to be created before engraving
the cylinder. Digital data for text and images feed
the engraving heads, that images the copper cylinder.
Three the more popular types of engraving process are
electromechanical engraving, chemical etching and
laser engraving.
Figure 1: The printing process using rotogravure.
The printed image results from the ink transfer from
the honeycomb shaped cells (see Fig. 1) engraved into
the copper cylinder. The un-etched areas of the cylin-
der represent the non-image (unprinted) areas. The
cell depth control the amount of ink to be transferred
to the surface. The final size and shape of the printed
dots depend on the ink and type of paper.
After engraving, the cylinder is polished for a con-
sistent surface, and imperfections removal. The cylin-
VISAPP 2019 - 14th International Conference on Computer Vision Theory and Applications
578