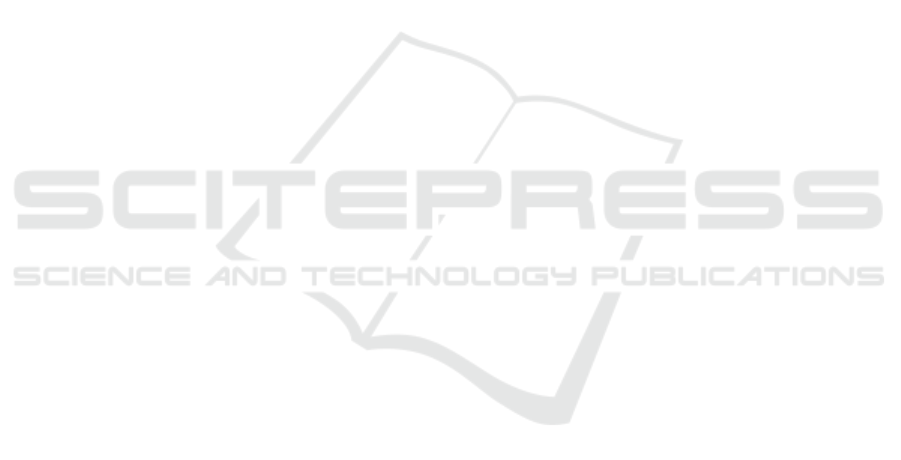
aircraft.
Based on this proof of concept, the creation of
such condional models will be focused on. This
can be addressed both from a 2D or 3D perspective
: gathering all the 3D classification results of a gi-
ven aircraft model (issued from many UAV’s flights)
to extract recurrent patterns, and using pattern 2D-
generative models conditioned upon detection results.
The presented method can be extended to all ex-
pected objects on the aircraft (marking, rivets, etc.),
or a combination via multi-primitive graph matching.
With more UAV inspections of the same aircraft over
a period of time, it could be envisioned to perform
orientation comparison to respond to loose screws.
REFERENCES
Backes, P. G., Bar-Cohen, Y., and Joffe, B. (1997). The
multifunction automated crawling system (MACS). In
Proceedings of International Conference on Robotics
and Automation, volume 1, pages 335–340.
Bauda, M.-A., Bazot, C., and Larnier, S. (2017). Real-
time ground marking analysis for safe trajectories of
autonomous mobile robots. In IEEE International
Workshop of Electronics, Control, Measurement, Sig-
nals and their Application to Mechatronics (ECMSM).
Bauda, M.-A., Grenwelge, A., and Larnier, S. (2018). 3D
scanner positioning for aircraft surface inspection. In
European Congress Embedded Real Time Software
and Systems.
Bjerregaard, L. (2018). Aircraft drone inspection techno-
logy. MRO Network.
Claybrough, M. (2016). System and method for automati-
cally inspecting surfaces. Patent WO 2016203151.
Davis, I. L. and Siegel, M. (1993). Automated nonde-
structive inspector of aging aircraft. In SPIE, editor,
Measurement Technology and Intelligent Instruments,
volume 2101.
Deruaz-Pepin, A. (2017). Method and system for deter-
mining the position of a moving craft. Patent WO
2017121936.
Donadio, F., Frejaville, J., Larnier, S., and Vetault, S.
(2016). Human-robot collaboration to perform aircraft
inspection in working environment. In 5th Internatio-
nal conference on Machine Control and Guidance.
Drury, C. G. (1999). Human reliability in civil aircraft
inspection. In Human Factors and Medicine Panel
(HFM) Workshop.
Drury, C. G., Patel, S. C., and Prabhu, P. V. (2000). Relative
advantage of portable computer-based workcards for
aircraft inspection. International Journal of Industrial
Ergonomics, 26(2):163–176.
Dubosclard, P., Larnier, S., Konik, H., Herbulot, A., and
Devy, M. (2015). Deterministic method for automatic
visual grading of seed food products. In Proceedings
of the International Conference on Pattern Recogni-
tion Applications and Methods (ICPRAM), volume 1,
pages 212–217.
Fishkel, F., Fischer, A., and Ar, S. (2006). Verification of
engineering models based on bipartite graph matching
for inspection applications. In Proceedings of the 4th
International Conference on Geometric Modeling and
Processing (GMP), pages 485–499.
Frejaville, J., Larnier, S., and Vetault, S. (2016). Locali-
sation
`
a partir de donn
´
ees laser d’un robot naviguant
autour d’un avion. In Reconnaissance des Formes et
l’Intelligence Artificielle (RFIA).
Futterlieb, M. (2017). Vision based navigation in a dynamic
environment. PhD thesis, Universit
´
e Paul Sabatier -
Toulouse III.
Futterlieb, M., Cadenat, V., and Sentenac, T. (2014). A na-
vigational framework combining visual servoing and
spiral obstacle avoidance techniques. In 11th Interna-
tional Conference on Informatics in Control, Automa-
tion and Robotics (ICINCO), volume 2, pages 57–64.
Jovan
ˇ
cevi
´
c, I. (2016). Exterior inspection of an aircraft
using a Pan-Tilt-Zoom camera and a 3D scanner mo-
ved by a mobile robot : 2D image processing and 3D
point cloud analysis. PhD thesis, Ecole des Mines
d’Albi-Carmaux.
Jovan
ˇ
cevi
´
c, I., Larnier, S., Orteu, J.-J., and Sentenac, T.
(2015). Automated exterior inspection of an aircraft
with a pan-tilt-zoom camera mounted on a mobile ro-
bot . Journal of Electronic Imaging, 24(6).
Jovan
ˇ
cevi
´
c, I., Viana, I., Orteu, J.-J., Sentenac, T., and Lar-
nier, S. (2016). Matching CAD model and image fe-
atures for robot navigation and inspection of an air-
craft. In International Conference on Pattern Recog-
nition Applications and Methods (ICPRAM 2016).
Kuhn, H. W. (1955). The hungarian method for the assig-
nment problem. Naval Research Logisitic, pages 83–
97.
Lakrouf, M., Larnier, S., Devy, M., and Achour, N. (2017).
Moving obstacles detection and camera pointing for
mobile robot applications. In Proceedings of the 3rd
International Conference on Mechatronics and Robo-
tics Engineering (ICMRE), pages 57–62.
Leiva, J. R., Villemot, T., Dangoumeau, G., Bauda, M. A.,
and Larnier, S. (2017). Automatic visual detection
and verification of exterior aircraft elements. In 2017
IEEE International Workshop of Electronics, Control,
Measurement, Signals and their Application to Me-
chatronics (ECMSM).
Liu, W., Anguelov, D., Erhan, D., Szegedy, C., Reed, S.,
Fu, C.-Y., and Berg, A. C. (2016). SSD: Single Shot
MultiBox Detector. In Computer Vision - European
Conference on Computer Vision (ECCV), pages 21–
37.
Marx, D. A. and Graeber, R. C. (1994). Human error in
aircraft maintenance. Johnstone, McDonald & Fuller,
Avebury Technical, Aldershot.
Miranda, J., Larnier, S., and Claybrough, M. (2018). Ca-
ract
´
erisation d’objets sur des images acquises par
drone. In Conf
´
erence Reconnaissance des Formes,
Image, Apprentissage et Perception.
VISAPP 2019 - 14th International Conference on Computer Vision Theory and Applications
426