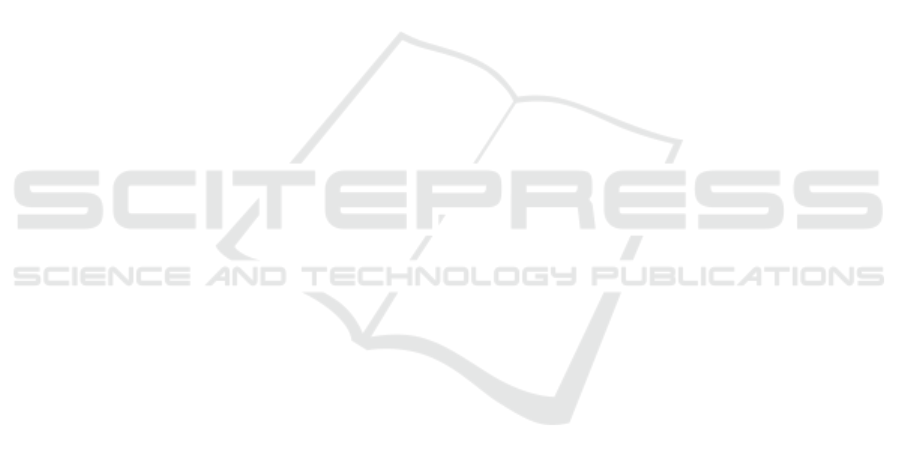
5 CONCLUSIONS
This paper presents the work carried out in the design
and development of piezoresistive sensor matrix used
to detect and monitor the pressure. The
characterization and calibration procedures of the
FSR sensor was presented, as well as, tests in pressure
measurement applications, where the influence of the
use of different spacers material (acrylic and felt)
with different stiffness was analysed. In this case, it
was observed that the use of a spacer material, with
low rigidity, namely the felt spacer, coupled to the
commercial FSR sensor was found to greatly improve
the accuracy of pressure measurement. The sensor’s
response using the felt spacers showed greater
sensitivity.
From the graph of Figure 12 it is possible to see
that the sensor starts to respond from a conductivity
of approximately 0,05 mS which, by data from
graphic representation of Figure 7, correspond to a
pressure values below 5 kPa. With this, it is observed
that the piezoresistive sensor can detect in the
pressure range where the value of the capillary
tension inside the tissues (32 mmHg, corresponding
to about 4 kPa) is inserted, from which the pressure
begins to cause lesions on the skin, especially in
regions of vulnerable bone prominence. Thus,
according to the study developed around the use of
commercial piezoresistive sensors in pressure
detection and mapping systems, it was found that this
kind of sensors allows the pressure measurement,
including when used with other pressure ulcer
prevention systems. The developed sensing matrix
was able to read pressure variations, presenting a
satisfactory performance, which proves its usefulness
in body pressure monitoring applications.
ACKNOWLEDGEMENTS
The authors acknowledge Graça Bonifácio, Sandra
Ventura, José Casquilho, Miguel Ribeiro for their
contributions. This research is supported by FEDER
funds through the COMPETE 2020 Programme
under project ActiveRest (project 18011 of the
33/SI/2015 call).
REFERENCES
Call, E. and Black, J. (2015). ‘Using Devices for Pressure
Ulcer Prevention and Treatment’. In National Pressure
Ulcer Advisory Panel.
Dealey, C. (2012). The Care of Wounds: A Guide for
Nurses. Chichester: John Wiley & Sons. 4th edition.
Available at: https://www.wiley.com/en-
us/The+Care+of+Wounds%3A+A+Guide+for+Nurses
%2C+4th+Edition-p-9781405195690 (Accessed:
24 January 2018).
FSR 402 (no date). Available at:
https://www.interlinkelectronics.com/fsr-402
(Accessed: 18 February 2018).
Fulton, B. and Monro, A. (2009). ‘Dynamic and static
support mattresses and overlays decreased pressure
ulcer incidence when compared to standard care in adult
acute care settings’, pp. 1–14. doi:
10.1213/ANE.0b013e3181f7107d.
Giovanelli, D. and Farella, E. (2016). ‘Force Sensing
Resistor and Evaluation of Technology for Wearable
Body Pressure Sensing’. In Journal of Sensors.
Hindawi, pp. 1–13. doi: 10.1155/2016/9391850.
Lyder, C. H. and Ayello, E. A. (2008). Pressure Ulcers: A
Patient Safety Issue, Patient Safety and Quality: An
Evidence-Based Handbook for Nurses. In Agency for
Healthcare Research and Quality (US), pp. 268-299.
Mattress Retail & Design | XSENSOR Technology
Corporation (no date). Available at:
https://xsensor.com/applications/mattress-design-rd/
(Accessed: 24 January 2018).
McInnes, E. et al. (2011). ‘Support surfaces for treating
pressure ulcers’. In Cochrane Database of Systematic
Reviews.
Menoita, E. et al. (2012). ‘Superfícies de apoio na
prevenção das úlceras de pressão’. In Journal of Aging
and Innovation.
Murray, M. et al. et al. (2001) ‘Clinical practice guidelines
for the prediction and prevention of pressure ulcers’. In
Prim. Intent., 9(3), pp. 88-97.
National Pressure Ulcer Advisory Panel (2007). ‘National
Pressure Ulcer Advisory Panel Support Surface
Standards Initiative Terms and Definitions Related to
Support Surfaces’, Components, pp. 1–10.
Overview | Force Sensitive Resistor (FSR) | Adafruit
Learning System (no date). Available at:
https://learn.adafruit.com/force-sensitive-resistor-
fsr/overview (Accessed: 24 February 2018).
Rocha, J. A., Miranda, M. J. and Andrade, M. J. (2006).
‘Abordagem terapêutica das úlceras de pressão -
Intervenções baseadas na evidência’. In Acta Medica
Portuguesa, 19(1), pp. 29–38.
Rocha, J. G. et al. (2008). ‘System providing discomfort
monitoring for people in wheelchairs’. In 2008 IEEE
International Symposium on Industrial Electronics,
Cambridge, UK, pp. 961–966.
Sensor Products Inc. (no date) Mattress Surface Pressure
Mapping. Available at:
www.sensorprod.com/bodyfitter (Accessed: 24
February 2018).
Superfícies de apoio na prevenção das úlceras de pressão
(no date). In Journal of Aging and Innovation.
BIODEVICES 2019 - 12th International Conference on Biomedical Electronics and Devices
296