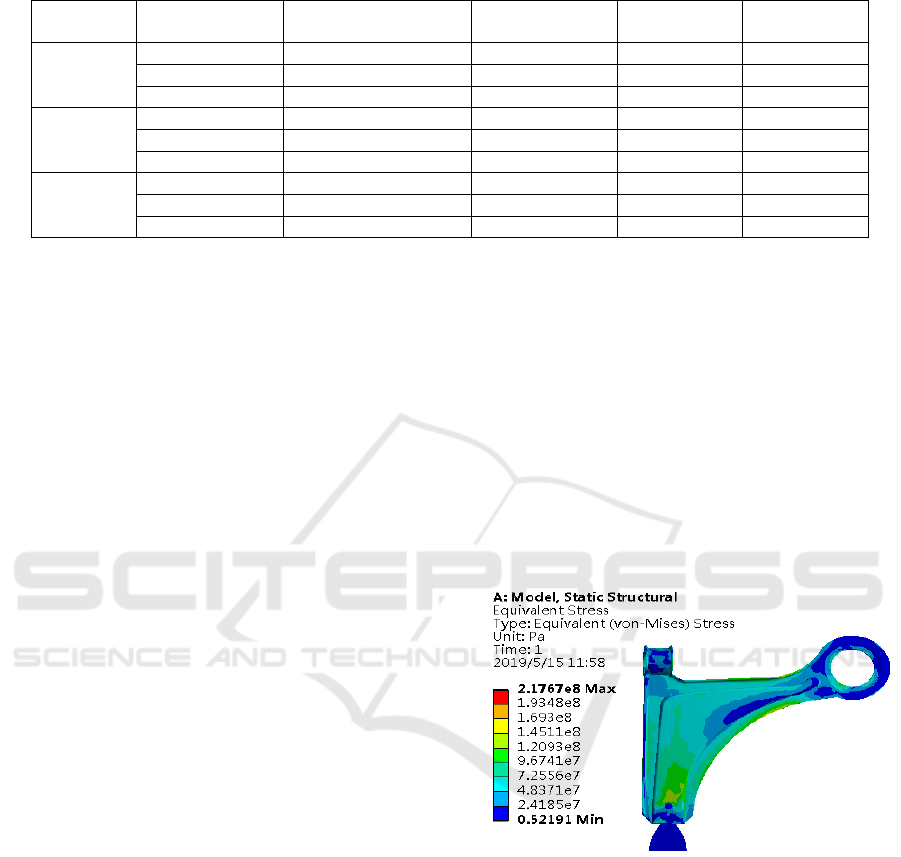
Table 1. This caption has one line so it is centered.
Among them, A and B are connected to the sub-
frame with rubber bushing, and C is connected to the
steering knuckle with spherical hinges (Heo S J, D.
O. Kang, J. H. Lee, et al, 2013).
In this paper, the whole vehicle dynamics model
built by ADAMS of an enterprise is used for
reference. According to the design criterion of the
enterprise, the strength analysis basis of four
representative connection points to the lower control
arm is calculated based on the given height and
quality of the center of mass, classical formula of
automobile theory and dynamic equation of
automobile suspension. The linear mechanical
parameters of four typical working conditions are
simulated. As shown in Table 1:
2.2 Strength and Stiffness Analysis
Because the force on the lower control arm of the
suspension is complex in the actual movement of the
vehicle. Often multiple forces and moments coexist
at the same time. Among the four commonly used
strength theories in material mechanics, the third and
fourth strength theories of classical material
mechanics are closest to the lower control arm. The
steel of the original lower control arm is QSTE450,
which belongs to plastic yield material and has
medium performance index in high strength steel.
Yield failure is one of the most important failure
failures of the lower control arm of McPherson
suspension, because it does not refer to the effect of
the second principal stress. So the fourth strength
theory is more theoretical basis for composite
calculation. Therefore, the fourth strength theory is
used to evaluate the mechanical properties of the
original control arm.
Stress nephograms under four extreme
conditions are shown in Figure 2-5.
According to the finite element analysis of four
kinds of simulation under extreme conditions, the
worst condition is forward braking, and its
maximum stress value reaches 420 MPa. The
maximum stress is mainly concentrated in the first
rivet-Y direction. Understanding the stress
distribution of the control arm under extreme
conditions can provide a reference for lightweight
drilling and weight reduction.
3 LIGHTWEIGHT DESIGN OF
LOWER CONTROL ARM
3.1 Structure-based Lightweight
Figure 2. Accelerated Forward.
In the light-weight design, this paper mainly adopts
the way of drilling and lightweight. According to the
results of stress analysis of four representative
working conditions mentioned above, it can be
concluded that the working condition of forward
braking is the worst. Therefore, structural
optimization and lightweight are also optimized
based on the stress analysis results of forward
braking. In most areas where the stress value is
small, we can drill lightweight holes. The regions
with large stress values can be strengthened to
reduce the regions with large local stress values. At
the same time, the minimum safety factor is
ICVMEE 2019 - 5th International Conference on Vehicle, Mechanical and Electrical Engineering
22