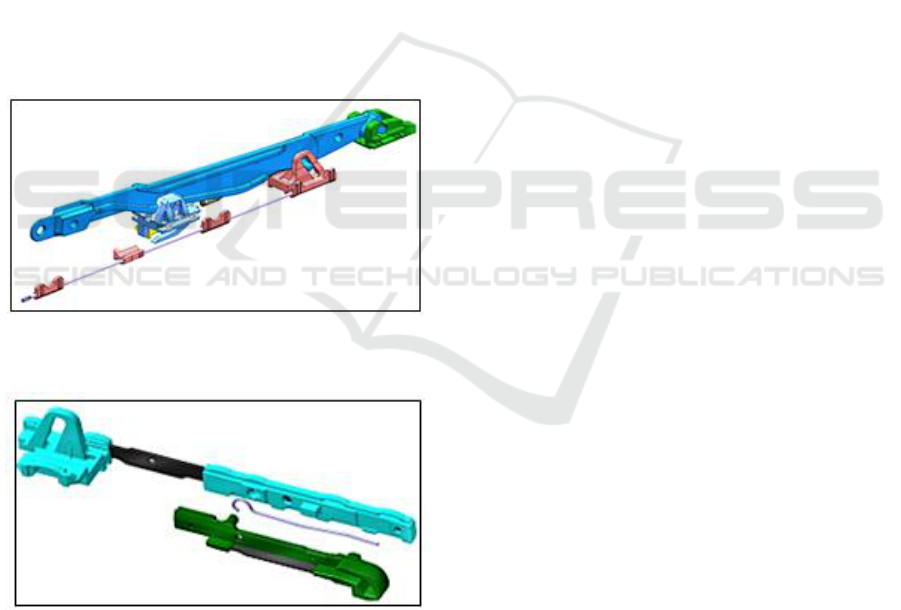
3 FAILURE POINT
IMPROVEMENT PLAN AND
VERIFICATION
3.1 Failure Point 1 Improvement
Results and Validation
Because the analysis of failure parts confirmed that
there was a problem with their structure, the
improvement result diagram of failure point 1 was
designed, and then the overall structure optimization
of the product was verified.
Respectively to draw the original car sunroof rail
slider old machinery group structure diagram 1 and
the improved new mechanical structure diagram 2,
the new machinery group is in the entire history of
the old mechanical group structure directly change
the structure, pressure spring effect is to make the
locking block into the locking hole, locking function
limit block, a new structure to solve the motor
sliding and locking groove sound problem.
Figure 1. Old mechanical group structure diagram: guide
block.
Figure 2. New mechanical structure diagram: guide block
+ lock block + compression spring assembly.
After asking the workers, most parts of the old
mechanical group used no. 45 steel, so other parts of
the new mechanical group still used no. 45 steel,
because no. 45 steel after proper heat treatment, has
high toughness, plasticity and wear resistance and
other comprehensive mechanical properties, suitable
for the mechanical group in a long time movement;
The pressure spring of the new mechanical group,
after searching for relevant information, can use the
piano steel wire, the material itself has very high
strength limit and elastic limit, can be widely used in
small spring material, its quality and performance
can meet the requirements.
Verification: before the durability test, the
operation resistance of the old mechanical group in
motion is tested and recorded. After a period of use,
its movement resistance value is tested. After that,
the movement resistance values generated during the
operation before and after the endurance of the new
mechanical group after the improvement were
recorded, and the data before and after the endurance
test of the mechanical group were compared and
confirmed, as shown in the following table 7.
Conclusion: after testing, it is concluded that the
trajectory of the new mechanical group is
controllable and the motion resistance is small, so as
to achieve a smoother movement and reduce the
amount of deformation caused by the movement. No
abnormal state (valid) was found in the mechanical
group whose new result state was verified before
and after the durability of its products.
3.2 Failure Point 2 Improvement
Results and Verification
Because the experimental state of various pieces
under various conditions was analyzed, the
improvement result of failure point 2 was obtained,
and then the condition change verification and
sealing strip length management were further
verified.
In the sealing strip processing, mold temperature
control machine to change the mold temperature
after curing. The main functions of changing mold
temperature are: to improve the molding efficiency
of products, reduce the production of defective
products, improve the appearance of products, and
restrain the defects of products; when the product is
vulcanized, vulcanizing agent and accelerator are
added. Under certain temperature and pressure
conditions, the linear macromolecules in the rubber
are transformed into three-dimensional mesh
structure to realize the crosslinking vulcanization of
the rubber. After vulcanization of the rubber, change
the original strength of low, small elasticity, cold
and hard heat viscosity, easy to age and other defects,
improve wear resistance, resistance to swelling, heat
resistance and other aspects, expanded its scope of
application.
Analysis and Research on the Fault Phenomenon of Car Sunroof
67