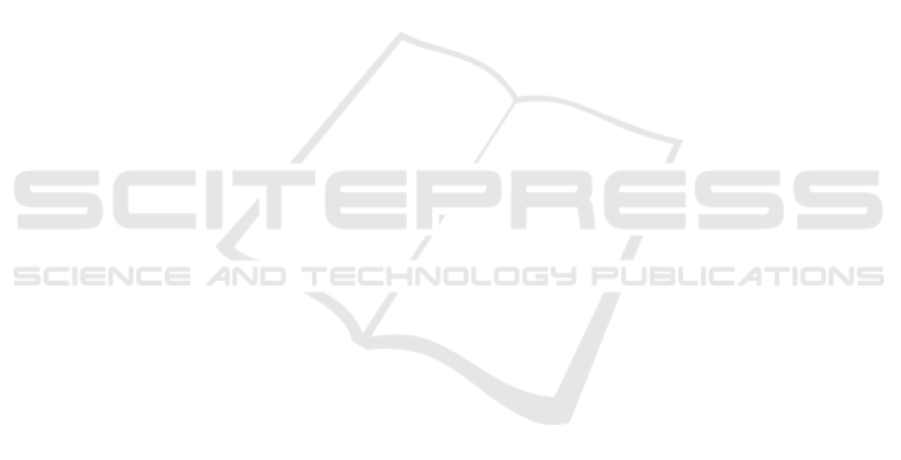
Technique: The Root Mean Square (RMS) and Mean
value of both ‘Force’ and ‘Vibration’ datasets were
calculated for every block. For example, Block 1
had (RMS and Mean) ‘Force’ values and (RMS and
Mean) ‘Vibration’ values affiliated to it. This feature
extraction technique was applied to both Operation1
and Operation2 datasets, thus generating eight values
of ‘Force’ and ‘Vibration’ for every block. The tem-
perature was a single value measured only once across
both Operation1 and 2 for every block. Hence, the
final training dataset comprised of 17 sample values
due to 17 blocks and each sample was associated with
the above mentioned nine features. Following such a
technique, ensured that the input and output datasets
could now be mapped easily without having to either
reduce the input dataset or duplicate the output values.
Hence, this technique embedded in an ANFIS frame-
work highlights the novelty proposed by this paper.
5.2 Overarching Model Architecture
Figure 5 shows the proposed system architecture. The
nine feature dataset as described above was subjected
to some feature extraction techniques and was then
used as input to an ANFIS model for predicting the
Sa value. The proposed model is a three-input single-
output Sugeno based ANFIS. This architecture over-
came the limitations of ‘Model 1’ as now each block
was linked to nine distinct features, all mapped to a
single Sa value thus avoiding any duplications.
5.3 Feature Extraction
To remove any biases, the sample dataset was ran-
domised. Furthermore, it was identified that the vi-
bration, force and temperature data were all scaled
differently. Therefore, to ensure equal contribution to
the model design, they all were normalised to a com-
parable scale i.e. between 0 and 1. Having nine input
features but only 17 data samples, such a dataset was
considered unfit for model training. Therefore, PCA
was applied to reduce the dimensionality and retain
the useful information of the removed features;
PCA Method: The four vibration values (i.e. RMS
and Mean from both Operation 1 and 2) were first col-
lected together and then subjected to PCA thus reduc-
ing the dimension of vibration dataset from four to
one. The same method was then applied to the four
force associated features thus reducing their dimen-
sionality to one. Following this method, the dimen-
sionality of the training dataset was reduced from nine
features at the start to three input features, i.e. PCA’d
Vibration, PCA’d Force and Temperature as shown in
Figure 5. Due to the small sample size (i.e. seven-
teen samples), it was decided to utilise 13 samples for
training i.e. a 76% and 24% split of the data.
Verification and Validation
Multiple Runs: The developed ANFIS model was
executed 100 times such that the original dataset was
randomised in each run thus producing a different
RMSE and Correlation value. This was done to ev-
idence the generalisability of the model. Therefore to
evaluate the performance, average RMSE and Corre-
lation values were calculated.
K-Fold Cross Validation: Despite the reduced di-
mensionality, such a low number of data samples
posed the risk of overfitting. Hence, 4 Fold Cross-
validation was applied. The performance was eval-
uated by calculating the average Correlation and
RMSE value obtained in each fold. This was used
to evidence the model’s diversity and robustness.
5.4 Results and Discussion
An average correlation and RMSE of 0.87 and 0.09
was obtained on running the model 100 times using
the testing data thus showing acceptable performance.
Figures 6 and 7 show the best predicted and observed
Sa values obtained among the 100 runs using test-
ing and training data. A low RMSE of 0.07 and
0.05 shows the high accuracy of the predictor. Fur-
thermore, the results obtained from the 4-Fold cross-
validation also showed a high correlation and a low
RMSE value for both the training and testing dataset,
thus evidencing model’s generalisability. The 3D sur-
face plots between the input and output, correspond-
ing to this single best run are shown in Figure 8 and
Figure 9.These plots are non-linear and within the
data minimum and maximum ranges thus suggesting
that no obvious extrapolation occurred. Furthermore,
a linear regression model and a 2 layer feed-forward
ANN were designed and used as benchmarks to com-
pare the performance. Both these models produced a
higher RMSE and a lower correlation value than the
ANFIS model thus showing an inferior performance.
Comparison between Model 1 and Model 2
Model2 achieved a lower RMSE and a higher Corre-
lation value. Some other differences were as follows:
• Model1 followed a “Bin Division” approach, util-
ising the actual dataset values thus leading to in-
formation loss. While Model2 utilised the statis-
tical features of the dataset to predict the surface
roughness and thus the preferred choice
FCTA 2020 - 12th International Conference on Fuzzy Computation Theory and Applications
290