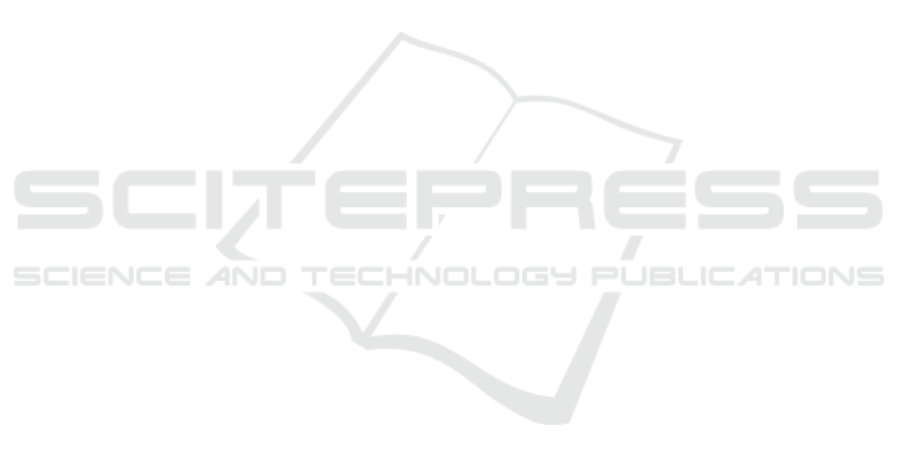
work must be given more attention, because without
proper tools, it is difficult to validate the proposed
approaches. Concerning the aspects covered by the
selected papers, all studies have covered the data in-
tegration aspect. Data analysis and monitoring have
also been covered by 16 papers and Systems integra-
tion comes third, with 15 papers. We think it is nor-
mal that these two aspects are the most covered as-
pects, due to the fact that computer integrated man-
ufacturing is all about connected systems, data inter-
changeability and reusability. Cloud computing has
been covered as well by 9 contributions, which is less
than what we expected, in view of the opportunities
that are allowed by it. Thus, much work remains to
be done to cover other aspects of CIM. As for Secu-
rity, little attention has been given to this aspect in
research. Yet it is a crucial prerequisite to ensure the
sustainability of the business. Mobility has been cov-
ered the least, with only 3 contributions, despite it has
being an important aspect in the era of industry 4.0,
which makes it besides security potential research ar-
eas.
REFERENCES
Alessandra Caggiano, T. Segreto, R. T. (2016). Cloud man-
ufacturing framework for smart monitoring of ma-
chining.
Bousdekis, A., Papageorgiou, N., Magoutas, B., Apostolou,
D., and Mentzas, G. (2015). A real-time architecture
for proactive decision making in manufacturing enter-
prises.
Clements, P. C. (1996). A survey of architecture description
languages.
Dennis Weihraucha, Paul Anton Schindlera, W. S. (2018).
A conceptual model for developing a smart process
control system.
Ding, K., Chan, F. T., Zhang, X., Zhou, G., and Zhang, F.
(2019). Defining a digital twin-based cyber-physical
production system for autonomous manufacturing in
smart shop floors.
Emanuel Trunzer1 · Ambra Cal
`
a2, 3 · Paulo Leit
˜
ao4 ·
Michael Gepp2 · Jakob Kinghorst1 · Arndt L
¨
uder3,
H. S. . M. R. . B. V. (2019). System architectures for
industrie 4.0 applications: Derivation of a generic ar-
chitecture proposal.
Farid Meziane, Sunil Vadera, N. P. (2000). Intelligent sys-
tems in manufacturing: Current developments and fu-
ture, article in integrated manufacturing systems.
Fei Tao, Q. Q. (2019). New it driven service-oriented smart
manufacturing: Framework and characteristics.
Jeon, B., Um, J., Yoon, S. C., and Suh, S.-H. (2016). An
architecture design for smart manufacturing execution
system.
Jiang, J.-R. (2017). An improved cyber-physical systems
architecture for industry 4.0 smart factories.
Kavakli, E., Buenabad-Chavez, J., Tountopoulos, V.,
Loucopoulos, P., and Sakellariou, R. (2018). Speci-
fication of a software architecture for an industry 4.0
environment.
Khakifirooz, M., Cayard, D., Chien, C. F., and Fathi, M.
(2018). A system dynamic model for implementation
of industry 4.0.
Kitchenham, C. (2007). Guidelines for performing system-
atic literature reviews in software engineering.
Lane Thames, D. S. (2016). Software-defined cloud manu-
facturing for industry 4.0.
Leit
˜
ao, P., Barbosa, J., Foehr, M., Cal
`
a, A., Perlo, P., Iuz-
zolino, G., Petrali, P., Vallhagen, J., and Colombo,
A. W. (2017). Instantiating the perform system ar-
chitecture for industrial case studies.
Li, Q., Jiang, H., Tang, Q., Chen, Y., Li, J., and Zhou, J.
(2017). Smart manufacturing standardization model
and standards framework.
Li, Q., Pu, Y., Xu, Z., Wei, H., Tang, Q., Chan, I., Jiang, H.,
Li, J., and Zhou, J. (2019). Architecture of integration
of industrialization and informatization.
Li Da Xu, Eric L. Xu, L. L. (2018). Industry 4.0: state of
the art and future trends.
Lia, Q., Tanga, Q., Chana, I., Weia, H., Pua, Y., Jiangb,
H., Lib, J., and Zhou, J. (2018). Smart manufacturing
standardization: Architectures, reference models and
standards framework.
Michael P. Papazoglou, Willem-Jan van den Heuvel,
J. E. M. (2015). A reference architecture and
knowledge-based structures for smart manufacturing
networks.
M
¨
uller, R., H
¨
orauf, L., Vette, M., and Speicher, C.
(2016). Planning and developing cyber-physical as-
sembly systems by connecting virtual and real worlds.
Mohammed, W. M., Ramis, B., Iarovyi, S., and Negri, E.
(2018). Generic platform for manufacturing execution
system functions in knowledge-driven manufacturing
systems.
SangSu Choi, Thorsten Wuest, B. K. (2018). Towards a
platform for smart manufacturing improvement plan-
ning.
Sherwin Menezes, Savio Creado, R. Y. Z. (2018).
Smart manufacturing execution systems for small and
medium-sized enterprises.
Tae Hyun Kim, Jongpil Jeongb, Y. K. (2019). A conceptual
model of smart manufacturing execution system for
rolling stock manufacturer.
Tang, H., Li, D., Wang, S., and Dong, Z. (2018). Casoa: An
architecture for agent-based manufacturing system in
the context of industry 4.0.
Tao, F., Qi, Q., Liu, A., and Kusiak, A. (2018). Data-driven
smart manufacturing.
Theorin, A., Bengtsson, K., Provost, J., Lieder, M., Johns-
son, C., Lundholm, T., and Lennartson, B. (2017). An
event-driven manufacturing information system archi-
tecture for industry 4.0.
Thijs Franck, M.-E. I. (2018). Towards an integrated archi-
tecture model of smart manufacturing enterprises.
Computer Integrated Manufacturing Architecture: A Literature Review
255