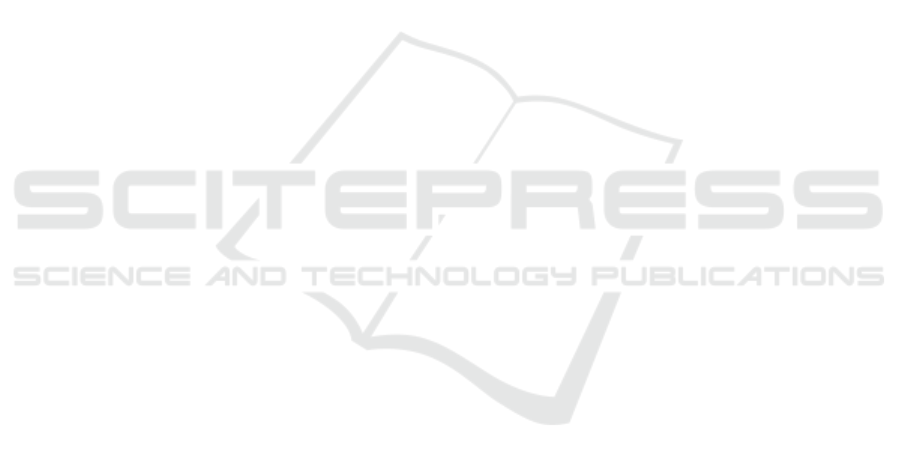
game engine provides an abstraction layer and flexibil-
ity in terms of features, visual fidelity and VR systems.
The devised workflow aims at creating a low barrier
of entry for industrial applications such that it can be
used in existing production processes with little effort.
ACKNOWLEDGEMENTS
We thank Alexander Pagonis and Jasmin Armbr
¨
uster
for their valuable input in this project. This work is
supported by the Austria Research Promotion Agency
(FFG) within project Virtual Reality for Cognitive
Products and Production Systems (grant No.: 864814).
REFERENCES
Al-Ahmari, A. M., Abidi, M. H., Ahmad, A., and Dar-
moul, S. (2016). Development of a virtual manufac-
turing assembly simulation system. Adv. Mech. Eng.,
8(3):168781401663982.
Boud, A. C., Baber, C., and Steiner, S. J. (2000). Virtual
reality: A tool for assembly? Presence Teleoperators
Virtual Environ., 9(5):486–496.
Bowland, N., Gao, J., and Sharma, R. (2003). A PDM- and
CAD-integrated assembly modelling environment for
manufacturing planning. J. Mater. Process. Technol.,
138(1-3):82–88.
Braatz, D., Toledo, F. M., Tonin, L. A., Da Costa, M. A. B.,
and Menegon, N. L. (2011). Conceptual and method-
ological issues for the application of game engines in
designs of productive situations. In 21st Int. Conf. Prod.
Res. Innov. Prod. Prod. ICPR 2011 - Conf. Proc.
Brooke, J. (1996). SUS - A quick and dirty usability scale.
Usability Eval. Ind., 189(194):4–7.
Carlson, P., Peters, A., Gilbert, S. B., Vance, J. M., and
Luse, A. (2015). Virtual Training: Learning Transfer
of Assembly Tasks. IEEE Trans. Vis. Comput. Graph.,
21(6):770–782.
Choi, S., Jo, H., Lee, J., and Noh, S. D. (2010). A rule-
based system for the automated creation of VR data
for virtual plant review. Concurr. Eng. Res. Appl.,
18(3):165–183.
Christiand, Yoon, J., and Kumar, P. (2009). A novel optimal
assembly algorithm for haptic interface applications of
a virtual maintenance system. J. Mech. Sci. Technol.,
23(1):183–194.
Chung, C. and Peng, Q. (2008). Enabled dynamic tasks plan-
ning in Web-based virtual manufacturing environments.
Comput. Ind., 59(1):82–95.
Convard, T., Picon, F., and Wilken, M. (2018). Acceler-
ating Data Conversion and Visualization–Automating
CAD data preparation and real-time visualization using
Unreal Studio. Technical report, Epic Games.
Epic Games (2019). Unreal engine. https://www.
unrealengine.com.
Gallegos-Nieto, E., Medell
´
ın-Castillo, H. I., Gonz
´
alez-
Badillo, G., Lim, T., and Ritchie, J. (2017). The anal-
ysis and evaluation of the influence of haptic-enabled
virtual assembly training on real assembly performance.
Int. J. Adv. Manuf. Technol., 89(1-4):581–598.
Gong, L., Berglund, J., Fast-Berglund,
˚
A., Johansson, B.,
Wang, Z., and B
¨
orjesson, T. (2019). Development of
virtual reality support to factory layout planning. Int. J.
Interact. Des. Manuf., 13(3):935–945.
Hilfert, T. and K
¨
onig, M. (2016). Low-cost virtual reality
environment for engineering and construction. Vis.
Eng., 4(1):2.
Jayaram, S., Jayaram, U., Wang, Y., Tirumali, H., Lyons,
K., and Hart, P. (1999). VADE: A Virtual Assembly
Design Environment. IEEE Comput. Graph. Appl.,
19(6):44–50.
Jerald, J. (2016). The VR Book. Association for Computing
Machinery and Morgan & Claypool, New York, NY,
USA.
Jun, Y., Liu, J., Ning, R., and Zhang, Y. (2005). Assembly
process modeling for virtual assembly process plan-
ning. Int. J. Comput. Integr. Manuf., 18(6):442–451.
Korves, B. and Loftus, M. (1999). The application of immer-
sive virtual reality for layout planning of manufacturing
cells. Proc. Inst. Mech. Eng. Part B J. Eng. Manuf.,
213(1):87–91.
Li, J. R., Liu, J. W., Wang, Q. H., and Hu, G. H. (2018). A
staged haptic rendering approach for virtual assembly
of bolted joints in mechanical assembly. Int. J. Adv.
Manuf. Technol., 96(1-4):161–171.
Liu, Z., Nan, Z., Qiu, C., Tan, J., Zhou, J., and Yao, Y.
(2019). A discrete fireworks optimization algorithm
to optimize multi-matching selective assembly prob-
lem with non-normal dimensional distribution. Assem.
Autom., 39(2):323–344.
Mahdjoub, M., Monticolo, D., Gomes, S., and Sagot, J.-C.
(2010). A collaborative Design for Usability approach
supported by Virtual Reality and a Multi-Agent Sys-
tem embedded in a PLM environment. Comput. Des.,
42(5):402–413.
Michalos, G., Karvouniari, A., Dimitropoulos, N., Togias,
T., and Makris, S. (2018). Workplace analysis and
design using virtual reality techniques. CIRP Ann.,
67(1):141–144.
Ou, L.-M. and Xu, X. (2013). Relationship matrix based
automatic assembly sequence generation from a CAD
model. Comput. Des., 45(7):1053–1067.
Sagardia, M., Hulin, T., Hertkorn, K., Kremer, P., and
Sch
¨
atzle, S. (2016). A platform for bimanual virtual
assembly training with haptic feedback in large multi-
object environments. In Proc. ACM Symp. Virtual Real.
Softw. Technol. VRST, volume 02-04-November-2016,
pages 153–162, New York, USA. ACM Press.
Wang, Q. H., Huang, Z. D., Li, J. R., and Liu, J. W. (2018). A
force rendering model for virtual assembly of mechani-
cal parts with clearance fits. Assem. Autom., 38(2):173–
181.
Zhang, N., Liu, Z., Qiu, C., Hu, W., and Tan, J. (2019). Opti-
mizing assembly sequence planning using precedence
graph-based assembly subsets prediction method. As-
sem. Autom., ahead-of-print(ahead-of-print).
GRAPP 2020 - 15th International Conference on Computer Graphics Theory and Applications
278