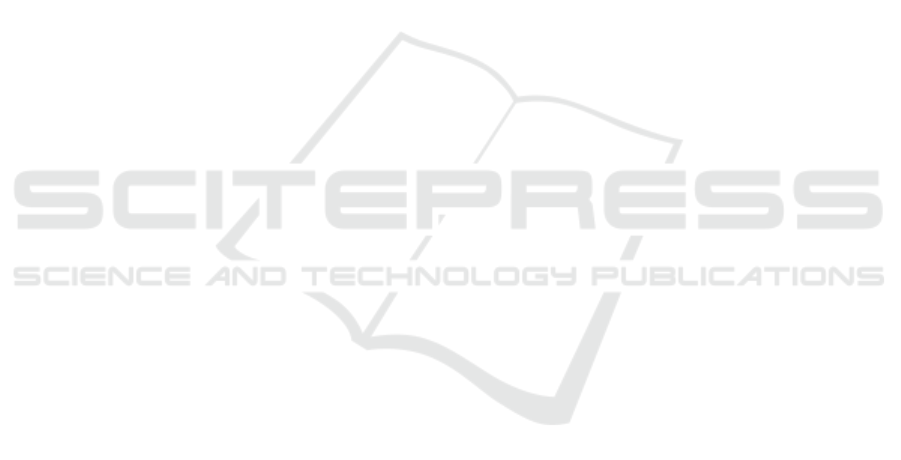
ical shape. This implies that fewer residuals are cre-
ated for control points near the border of the lens
and the smoothing term has a larger influence lead-
ing to worse reconstruction. However real measure-
ments tend to create very noisy and inaccurate mea-
surements near the edge of the lens. These error result
from inter reflections or rough surface on the edges,
such that we decided not to reduce the influence of
the smoothing term towards the fringes.
As mentioned in Sect. 4.1 we assume that the
interpolation of the sparse measurements has a pro-
found impact on the final reconstruction. To ver-
ify this, we compared the bicubic and bilinear inter-
polation of M for different sample rates. The first
method results in a smooth function even at pixel bor-
ders, whereas the linear interpolation can cause G1-
discontinuities. The top plot in Fig. 5a shows that the
bicubic interpolation is generally the superior interpo-
lation method especially for freeform surfaces with a
lower sample rate. For higher sample rates however,
the linear interpolation is also a good approximation.
Finally, we study the convergence rate of the op-
timization procedure in the second row of Fig. 5.
The simulation and ground truth error behave simi-
lar and only change insignificantly for the first fifteen
to twenty iterations for the simulated objects.
5 CONCLUSION AND FUTURE
WORK
We presented two setups to reconstruct a lens sur-
face from its reflection pattern. We have shown that
a continuous line, used in the first setup, produces
reconstructions of inadequate accuracy for quality
control. However, the proposed optimization frame-
work and setup was adapted to explicitly provide
ray-measurement correspondences. The optimiza-
tion framework is agnostic to the actual measurement
technique, if a mapping from the surface point to the
space of the light source is available. In future work
we will try different types of lasers that directly en-
code the angle along the ray (e.g. using phase encod-
ing) and evaluate if the denser measurements signifi-
cantly impact reconstruction quality.
In this paper we explicitly filtered secondary re-
flections to stick to a simple light path with a single
reflection at the initial surface. We therefore require
two scans to fully capture a single lens. The presented
framework can be extended easily to more complex
paths with multiple surface interactions. We will in-
corporate this into our method to simultaneously cap-
ture both sides of a PAL in a single measurement.
Although the reconstruction time of around 2 min-
utes is short enough to include the method as a qual-
ity assurance tool into an existing production line, we
would like to speed up the process. Since the simula-
tions of the individual laser rays, done during residual
computation, are independent, we anticipate a mean-
ingful speedup by implementing a GPU based version
of our algorithm.
ACKNOWLEDGEMENTS
This research is funded by Bayerische Forschungss-
tiftung ”Schritthaltende 3D-Rekonstruction und -
Analys (AZ-1184-15)” (For3D). The lenses and PALs
are provided by our project partners Rupp+Hubrach
Brillenglas.
REFERENCES
Agarwal, S., Mierle, K., and Others. Ceres solver.
http://ceres-solver.org.
B
¨
ohm, W. (1977). Cubic b-spline curves and surfaces
in computer aided geometric design. Computing,
19(1):29–34.
Bookstein, F. L. (1989). Principal warps: thin-plate splines
and the decomposition of deformations. IEEE Trans-
actions on Pattern Analysis and Machine Intelligence,
11(6):567–585.
Chamadoira, S., Blendowske, R., and Acosta, E. Progres-
sive addition lens measurement by point diffraction in-
terferometry. OPTOMETRY AND VISION SCIENCE,
89(10):15321542.
Farin, G. (2002). Curves and Surfaces for CAGD: A Prac-
tical Guide. Morgan Kaufmann Publishers Inc., San
Francisco, CA, USA, 5th edition.
Greiner, G. (1994). Variational Design and Fairing of Spline
Surfaces. Computer Graphics Forum, 13(3):143–154.
Halstead, M. A., Barsky, B. A., Klein, S. A., and Mandell,
R. B. (1996). Reconstructing curved surfaces from
specular reflection patterns using spline surface fitting
of normals. In Proceedings of the 23rd Annual Con-
ference on Computer Graphics and Interactive Tech-
niques, SIGGRAPH ’96, pages 335–342, New York,
NY, USA. ACM.
Hocken, R. and Pereira, P. (2011). Coordinate Measuring
Machines and Systems, Second Edition. CRC Press.
Kaminski, J. (2008). Geometrische Rekonstruktion spiegel-
nder Oberfl
¨
achen aus deflektometrischen Messdaten.
PhD thesis, FAU Erlangen N
¨
urnberg.
Kaminski, J., Lowitzsch, S., Knauer, M. C., and H
¨
ausler, G.
(2006). Full-field shape measurement of specular sur-
faces. In Osten, W., editor, Fringe 2005, pages 372–
379, Berlin, Heidelberg. Springer Berlin Heidelberg.
Knauer, M. (2006). Absolute Phasenmessende Deflektome-
trie. PhD thesis, FAU Erlangen N
¨
urnberg.
VISAPP 2020 - 15th International Conference on Computer Vision Theory and Applications
82