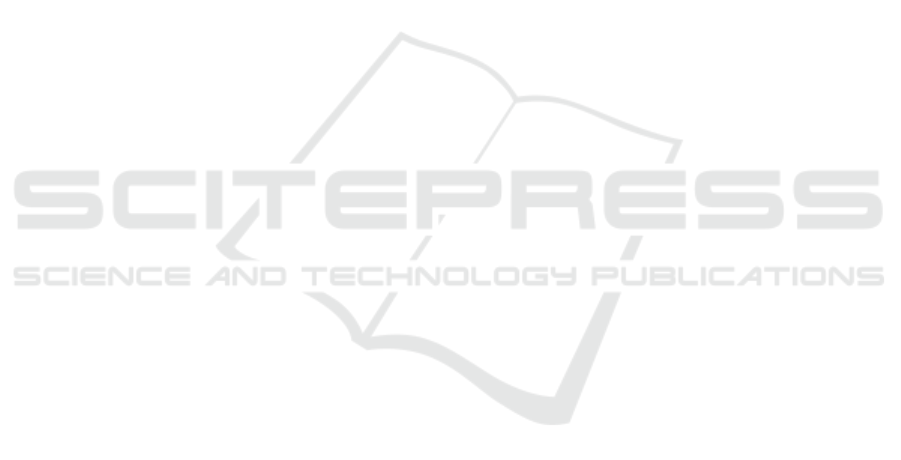
tion program under grant agreement No. 820971
ˆ
E
(”ROBOMINERS”) and from the RoboCity2030-
DIH-CM, Madrid Robotics Digital Innovation Hub,
S2018/NMT-4331, funded by Programas de Activi-
dades I+D en la Comunidad de Madrid and co-funded
by Structural Funds of the EU. The authors acknowl-
edge the help of Prof. Maria Consuelo Huerta of
the Department of Structural Mechanics and Indus-
trial Constructions and PhD.
´
Alvaro Nieto Carrero of
the Mechanical Engineering Department of the Uni-
versidad Polit
´
ecnica de Madrid.
REFERENCES
Alexander, R. M. (1984). Elastic energy stores in running
vertebrates. American Zoologist, 24(1):85–94.
Alexander, R. M. (1988). Why mammals gallop. American
zoologist, 28(1):237–245.
Bhattacharya, S., Singla, A., Dholakiya, D., Bhatnagar, S.,
Amrutur, B., Ghosal, A., Kolathaya, S., et al. (2019).
Learning active spine behaviors for dynamic and effi-
cient locomotion in quadruped robots. In 2019 28th
IEEE International Conference on Robot and Hu-
man Interactive Communication (RO-MAN), pages 1–
6. IEEE.
Coral, W., Rossi, C., and Curet, O. (2015). Free vibra-
tion analysis of a robotic fish based on a continuous
and non-uniform flexible backbone with distributed
masses. The European Physical Journal Special Top-
ics, 224(17):3379–3392.
Culha, U. and Saranli, U. (2011). Quadrupedal bounding
with an actuated spinal joint. In 2011 IEEE Interna-
tional Conference on Robotics and Automation, pages
1392–1397. IEEE.
Day, L. M. and Jayne, B. C. (2007). Interspecific scaling
of the morphology and posture of the limbs during the
locomotion of cats (felidae). Journal of Experimental
Biology, 210(4):642–654.
De Santos, P. G., Garcia, E., and Estremera, J. (2007).
Quadrupedal locomotion: an introduction to the con-
trol of four-legged robots. Springer Science & Busi-
ness Media.
Eckert, P., Spr
¨
owitz, A., Witte, H., and Ijspeert, A. J.
(2015). Comparing the effect of different spine and
leg designs for a small bounding quadruped robot. In
2015 IEEE International Conference on Robotics and
Automation (ICRA), pages 3128–3133. IEEE.
Gehring, C., Coros, S., Hutter, M., Bloesch, M.,
Hoepflinger, M. A., and Siegwart, R. (2013). Con-
trol of dynamic gaits for a quadrupedal robot. In 2013
IEEE international conference on Robotics and au-
tomation, pages 3287–3292. IEEE.
Iida, F., Reis, M., Maheshwari, N., Yu, X., and Jafari, A.
(2012). Toward efficient , fast , and versatile running
robots based on free vibration.
Maheshwari, N., Yu, X., Reis, M., and Iida, F. (2012).
Resonance based multi-gaited robot locomotion. In
2012 IEEE/RSJ International Conference on Intelli-
gent Robots and Systems, pages 169–174.
Nichol, J. G., Singh, S. P., Waldron, K. J., Palmer Iii,
L. R., and Orin, D. E. (2004). System design of
a quadrupedal galloping machine. The International
Journal of Robotics Research, 23(10-11):1013–1027.
Ogata, K. (1997). Modern control systems. Prentice Hall.
Park, H.-W., Chuah, M. Y., and Kim, S. (2014). Quadruped
bounding control with variable duty cycle via verti-
cal impulse scaling. In 2014 IEEE/RSJ International
Conference on Intelligent Robots and Systems, pages
3245–3252. IEEE.
Phan, L. T., Lee, Y. H., Lee, Y. H., Lee, H., Kang, H., and
Choi, H. R. (2017). Study on quadruped bounding
with a passive compliant spine. In 2017 IEEE/RSJ In-
ternational Conference on Intelligent Robots and Sys-
tems (IROS), pages 2409–2414. IEEE.
Poulakakis, I., Smith, J. A., and Buehler, M. (2005). Mod-
eling and experiments of untethered quadrupedal run-
ning with a bounding gait: The scout ii robot. The In-
ternational Journal of Robotics Research, 24(4):239–
256.
Raibert, M., Blankespoor, K., Nelson, G., and Playter, R.
(2008). Bigdog, the rough-terrain quadruped robot.
IFAC Proceedings Volumes, 41(2):10822–10825.
Raibert, M. H. (1986). Legged robots that balance. MIT
press.
Rao, S. S. (2011). Mechanical vibrations. Pearson Higher
5th Ed.
Reis, M. and Iida, F. (2014). An energy-efficient hop-
ping robot based on free vibration of a curved
beam. IEEE/ASME Transactions on Mechatronics,
19(1):300–311.
Semini, C., Tsagarakis, N. G., Guglielmino, E., Focchi,
M., Cannella, F., and Caldwell, D. G. (2011). De-
sign of hyq–a hydraulically and electrically actuated
quadruped robot. Proceedings of the Institution of
Mechanical Engineers, Part I: Journal of Systems and
Control Engineering, 225(6):831–849.
Skoblar, A.,
ˇ
Ziguli
´
c, R., Braut, S., and Bla
ˇ
zevi
´
c, S. (2017).
Dynamic response to harmonic transverse excitation
of cantilever euler-bernoulli beam carrying a point
mass. FME Transactions, 45(3):367–373.
Tsujita, K. and Miki, K. (2011). A study on trunk stiff-
ness and gait stability in quadrupedal locomotion
using musculoskeletal robot. In 2011 15th Inter-
national Conference on Advanced Robotics (ICAR),
pages 316–321. IEEE.
Wang, L., Yang, Y., Chen, Y., Majidi, C., Iida, F., Askou-
nis, E., and Pei, Q. (2018). Controllable and reversible
tuning of material rigidity for robot applications. Ma-
terials Today, 21(5):563–576.
Zhang, C. and Rossi, C. (2017). A review of compliant
transmission mechanisms for bio-inspired flapping-
wing micro air vehicles. Bioinspir. Biomim., 12(2).
Zhang, C. and Rossi, C. (2019). Effects of elastic hinges
on input torque requirements for a motorized indirect-
driven flapping-wing compliant transmission mecha-
nism. IEEE Access, 7:10368–13077.
A Bio-inspired Quasi-resonant Compliant Backbone for Low Power Consumption Quadrupedal Locomotion
249