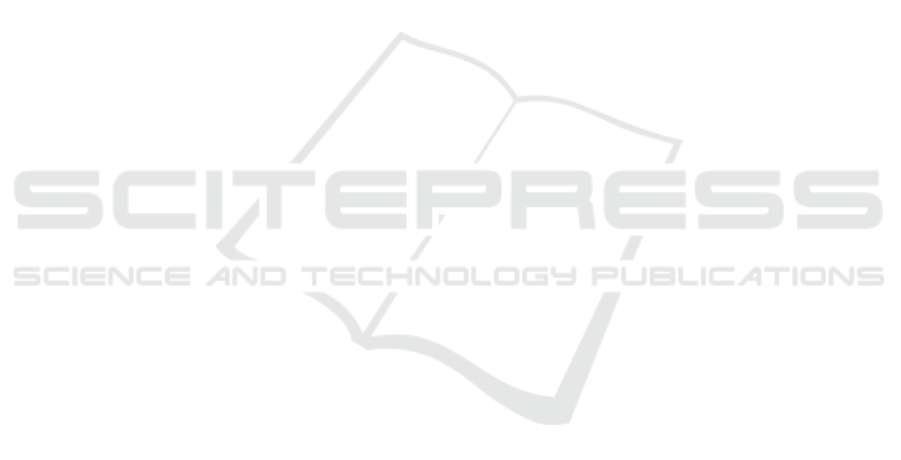
ACKNOWLEDGEMENTS
Thanks to the Hexalab platform (Bracci et al., 2019)
for providing tools and datasets from previous studies.
REFERENCES
Bracci, M., Tarini, M., Pietroni, N., Livesu, M., and
Cignoni, P. (2019). Hexalab.net: An online viewer for
hexahedral meshes. Computer-Aided Design, 110:24
– 36.
Fuentes Suárez, A. J. and Hubert, E. (2018). Scaffolding
skeletons using spherical voronoi diagrams: feasibil-
ity, regularity and symmetry. Computer-Aided Design,
102:83–93.
Gao, X. and Chen, G. (2016). A local frame based hexa-
hedral mesh optimization. In Proceedings of the 25th
International Meshing Roundtable.
Gao, X., Huang, J., Xu, K., Pan, Z., Deng, Z., and Chen, G.
(2017). Evaluating hex-mesh quality metrics via cor-
relation analysis. Computer Graphics Forum, 36:105–
116.
Hijazi, Y., Bechmann, D., Cazier, D., Kern, C., and Th-
ery, S. (2010). Fully-automatic branching recon-
struction algorithm : application to vascular trees.
In Shape Modeling International (SMI10), Aix-en-
Provence, 21-23 June.
Komaritzan, M. and Botsch, M. (2018). Projective skinning.
Proc. ACM Comput. Graph. Interact. Tech., 1(1).
Kowalski, N., Ledoux, F., and Frey, P. (2016). Smoothness
driven frame field generation for hexahedral meshing.
Computer-Aided Design, 72:65 – 77. 23rd Interna-
tional Meshing Roundtable Special Issue: Advances
in Mesh Generation.
Kremer, M., Bommes, D., Lim, I., and Kobbelt, L.
(2014). Advanced automatic hexahedral mesh genera-
tion from surface quad meshes. In Proceedings of the
22nd International Meshing Roundtable, pages 147–
164.
Lévy, B. and Liu, Y. (2010). Lp centroidal voronoi tes-
sellation and its applications. ACM Transactions on
Graphics, 29(4):119:1–119:11.
Livesu, M., Muntoni, A., Puppo, E., and Scateni, R. (2016).
Skeleton-driven adaptive hexahedral meshing of tubu-
lar shapes. Computer Graphics Forum, 35(7):237–
246.
Livesu, M., Pietroni, N., Puppo, E., Sheffer, A., and
Cignoni, P. (2020). Loopycuts: Practical feature-
preserving block decomposition for strongly hex-
dominant meshing. ACM Transactions on Graphics
(SIGGRAPH), 39(4).
Livesu, M., Sheffer, A., Vining, N., and Tarini, M. (2015).
Practical hex-mesh optimization via edge-cone recti-
fication. ACM Transactions on Graphics, 34(4).
Livesu, M., Vining, N., Sheffer, A., Gregson, J., and
Scateni, R. (2013). Polycut: Monotone graph-cuts for
polycube base-complex construction. Transactions on
Graphics (Proc. SIGGRAPH ASIA 2013), 32(6).
Lu, J. H.-C., Quadros, W. R., and Shimada, K. (2017). Eval-
uation of user-guided semi-automatic decomposition
tool for hexahedral mesh generation. Journal of Com-
putational Design and Engineering, 4(4):330 – 338.
Na, H.-S., Lee, C.-N., and Cheong, O. (2002). Voronoi
diagrams on the sphere. Computational Geometry,
23(2):183–194.
Nieser, M., Reitebuch, U., and Polthier, K. (2011). Cube-
Cover - Parameterization of 3D Volumes. Computer
Graphics Forum.
Panotopoulou, A., Ross, E., Welker, K., Hubert, E., and
Morin, G. (2018). Scaffolding a skeleton. Research
in Shape Analysis, 12:17–35.
Peng, C.-H., Zhang, E., Kobayashi, Y., and Wonka, P.
(2011). Connectivity editing for quadrilateral meshes.
ACM Transactions of Graphics, 30(6).
Schneiders, R. (1996). A grid-based algorithm for the gen-
eration of hexahedral element meshes. Engineering
with Computers, 12(3):168–177.
Sokolov, D., Ray, N., Untereiner, L., and Lévy, B. (2016).
Hexahedral-dominant meshing. ACM Transactions on
Graphics, 35(5).
Tagliasacchi, A., Alhashim, I., Olson, M., and Zhang, H.
(2012). Mean curvature skeletons. Computer Graph-
ics Forum (Proc. of the Symposium on Geometry Pro-
cessing).
Usai, F., Livesu, M., Puppo, E., Tarini, M., and Scateni,
R. (2015). Extraction of the quad layout of a triangle
mesh guided by its curve skeleton. ACM Transactions
on Graphics, 35:1–13.
Verhetsel, K., Pellerin, J., and Remacle, J.-F. (2019). Find-
ing hexahedrizations for small quadrangulations of the
sphere. ACM Transactions on Graphics, 38(4).
Wang, W., Jüttler, B., Zheng, D., and Liu, Y. (2008). Com-
putation of rotation minimizing frames. ACM Trans-
actions on Graphics, 27.
GRAPP 2021 - 16th International Conference on Computer Graphics Theory and Applications
54