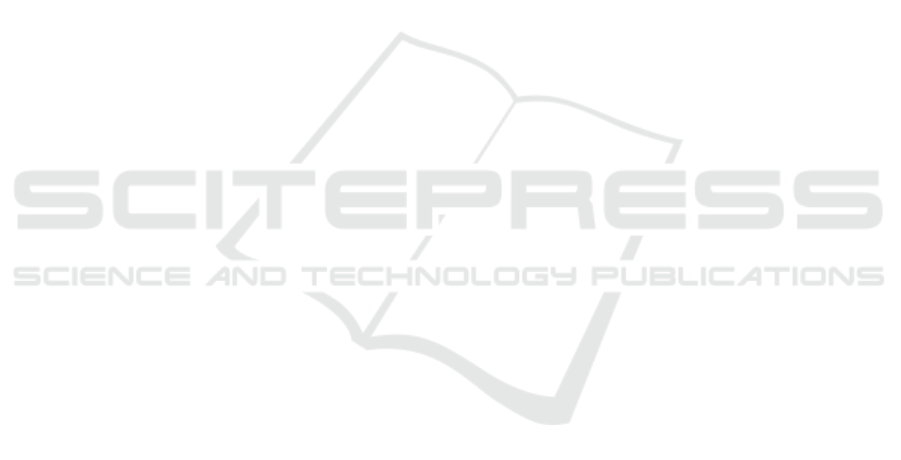
for further add-ons.
In the future, more complex scenarios, feedback
mechanisms, and the usefulness of the same sensors
for displaying different content will be investigated.
The sensor equipment can also be combined with
other tracking and interface methods such as optical
tracking or verbal commands. In case of a sensor
fusion with optical tracking, the inclusion of sensors
may compensate for shortcomings like tangibles with
only few features. At last, we will conduct a user
study to investigate the impact of tangible’s size and
weight on usability.
ACKNOWLEDGMENTS
This project (HA project no. 690/19-10) is financed
with funds of LOEWE – Landes-Offensive zur
Entwicklung Wissenschaftlich-
¨
okonomischer Exzel-
lenz, F
¨
orderlinie 3: KMU-Verbundvorhaben (State
Offensive for the Development of Scientific and Eco-
nomic Excellence).
REFERENCES
Bier, E. A., Stone, M. C., Pier, K., Buxton, W., and DeRose,
T. D. (1993). Toolglass and magic lenses: the see-
through interface. In Proceedings of the 20th con-
ference on Computer graphics and interactive tech-
niques, pages 73–80.
Billinghurst, M., Kato, H., and Poupyrev, I. (2008). Tangi-
ble augmented reality. ACM SIGGRAPH ASIA 2008
Courses.
D
¨
oring, D. C., Horst, R., Rau, L., and D
¨
orner, R. (2020).
Interface techniques for tangible augmented reality in
a mobile device setup for magic lens experiences. In
Weyers, B., L
¨
urig, C., and Zielasko, D., editors, GI
VR / AR Workshop. Gesellschaft f
¨
ur Informatik e.V.
Funk, M., Korn, O., and Schmidt, A. (2014). An augmented
workplace for enabling user-defined tangibles. In CHI
’14 Extended Abstracts on Human Factors in Com-
puting Systems, CHI EA ’14, page 1285–1290, New
York, NY, USA. Association for Computing Machin-
ery.
G
¨
unther, S., M
¨
uller, F., Schmitz, M., Riemann, J., Dez-
fuli, N., Funk, M., Sch
¨
on, D., and M
¨
uhlh
¨
auser, M.
(2018). Checkmate: Exploring a tangible augmented
reality interface for remote interaction. In Extended
Abstracts of the 2018 CHI Conference on Human Fac-
tors in Computing Systems, CHI EA ’18, page 1–6,
New York, NY, USA. Association for Computing Ma-
chinery.
Huber, J., Steimle, J., Liao, C., Liu, Q., and M
¨
uhlh
¨
auser,
M. (2012). Lightbeam: Interacting with augmented
real-world objects in pico projections. In Proceedings
of the 11th International Conference on Mobile and
Ubiquitous Multimedia, MUM ’12, New York, NY,
USA. Association for Computing Machinery.
Ishii, H. and Ullmer, B. (1997). Tangible bits: Towards
seamless interfaces between people, bits and atoms.
In Proceedings of the ACM SIGCHI Conference on
Human Factors in Computing Systems, CHI ’97, page
234–241, New York, NY, USA. Association for Com-
puting Machinery.
Kaltenbrunner, M. and Bencina, R. (2007). reactivision:
a computer-vision framework for table-based tangible
interaction. In TEI’07: First International Conference
on Tangible and Embedded Interaction.
Kaltenbrunner, M., Bovermann, T., Bencina, R., Costanza,
E., et al. (2005). Tuio: A protocol for table-top tangi-
ble user interfaces. In Proceedings of the 6th Interna-
tional Workshop on Gesture in Human-Computer In-
teraction and Simulation, pages 1–5.
Kaltenbrunner, M. and Echtler, F. (2018). The tuio 2.0 pro-
tocol: An abstraction framework for tangible inter-
active surfaces. Proc. ACM Hum.-Comput. Interact.,
2(EICS).
Lee, W. and Park, J. (2005). Augmented foam: A tangi-
ble augmented reality for product design. In Fourth
IEEE and ACM International Symposium on Mixed
and Augmented Reality (ISMAR’05), pages 106–109.
IEEE.
NXP Semiconductors (2014). I2C-bus specification and
user manual. Rev. 6.
NXP Semiconductors (2016). Kinetis K64F Sub-Family
Data Sheet. Rev. 7.
NXP Semiconductors (2017). 6-axis sensor with integrated
linear accelerometer and magnetometer. Rev. 8.
Seeed Technology Co., Ltd. (2020). Grove sen-
sors. https://www.seeedstudio.com/category/Sensor-
for-Grove-c-24.html. Accessed: 2020-10-02.
Watanabe, R., Itoh, Y., Asai, M., Kitamura, Y., Kishino, F.,
and Kikuchi, H. (2004). The soul of activecube: Im-
plementing a flexible, multimodal, three-dimensional
spatial tangible interface. In Proceedings of the 2004
ACM SIGCHI International Conference on Advances
in Computer Entertainment Technology, ACE ’04,
page 173–180, New York, NY, USA. Association for
Computing Machinery.
Zatulovsky, D. and El-Sana, J. (2019). Tangible stickers: A
sensor based tangible user interface. In International
Conference on Virtual Reality and Augmented Reality,
pages 297–304. Springer.
HUCAPP 2021 - 5th International Conference on Human Computer Interaction Theory and Applications
160