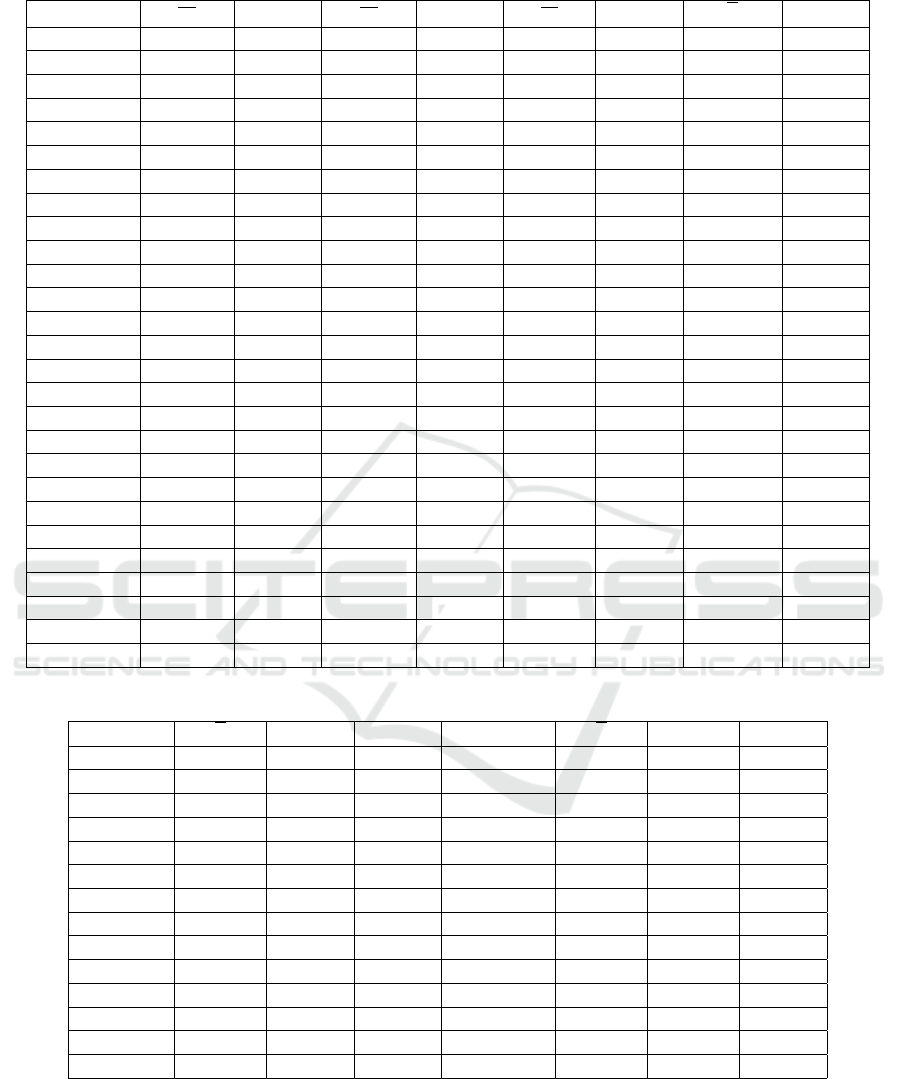
Table 7: Camera precision in terms of plane modelling consistency.
Cam
dist
n
x
σ
n
x
n
y
σ
n
y
n
z
σ
n
z
d σ
d
D415
0,5m
3,9E-03 2,5E-04 4,1E-03 2,1E-04 1,0E+00 1,5E-06 -5,0E-01 1,1E-04
D415
0,75m
3,7E-03 3,0E-04 -8,8E-03 2,0E-04 1,0E+00 1,5E-06 -7,5E-01 2,2E-04
D415
1m
1,7E-02 7,2E-04 -1,3E-03 2,6E-04 1,0E+00 1,3E-05 -1,0E+00 1,6E-04
D415
1,25m
1,4E-02 1,6E-03 -2,7E-03 3,6E-04 1,0E+00 1,8E-05 -1,3E+00 3,1E-04
D415
1,5m
1,8E-02 8,7E-04 3,0E-03 4,3E-04 1,0E+00 1,6E-05 -1,5E+00 4,6E-04
D415
1,75m
2,2E-02 8,5E-04 3,4E-04 5,8E-04 1,0E+00 1,8E-05 -1,8E+00 4,9E-04
D415
2m
1,3E-02 2,9E-03 2,4E-03 8,6E-04 1,0E+00 2,9E-05 -2,0E+00 1,1E-03
D415
2,5m
1,0E-02 1,5E-03 -3,2E-03 9,3E-04 1,0E+00 1,4E-05 -2,5E+00 2,8E-03
D415
3m
1,4E-02 3,2E-03 -5,8E-04 1,1E-03 1,0E+00 3,3E-05 -3,0E+00 1,8E-03
D415
3,5m
6,6E-03 1,8E-03 1,8E-03 1,3E-03 1,0E+00 1,2E-05 -3,5E+00 3,2E-03
L515
0,5m
-4,6E-05 6,1E-04 -2,9E-03 2,3E-04 1,0E+00 7,9E-07 -5,0E-01 3,5E-04
L515
0,75m
1,8E-03 4,6E-04 -2,7E-03 1,6E-04 1,0E+00 7,1E-07 -7,5E-01 3,3E-04
L515
1m
-1,9E-03 6,1E-04 -5,7E-03 1,5E-04 1,0E+00 1,9E-06 -1,0E+00 3,5E-04
L515
1,25m
-6,8E-06 3,1E-04 2,1E-03 7,6E-05 1,0E+00 1,9E-07 -1,3E+00 3,1E-04
L515
1,5m
-3,1E-03 5,2E-04 -9,2E-04 1,9E-04 1,0E+00 1,7E-06 -1,5E+00 3,3E-04
L515
1,75m
1,8E-03 3,3E-04 3,1E-04 1,0E-04 1,0E+00 6,2E-07 -1,8E+00 3,1E-04
L515
2m
-8,0E-04 4,5E-04 -5,1E-04 1,7E-04 1,0E+00 4,4E-07 -2,0E+00 3,9E-04
L515
2,5m
3,2E-04 3,5E-04 -8,7E-04 1,4E-04 1,0E+00 1,7E-07 -2,5E+00 3,5E-04
L515
3m
-2,1E-03 3,3E-04 -3,9E-03 1,5E-04 1,0E+00 1,1E-06 -3,0E+00 3,3E-04
L515
3,5m
1,7E-03 4,0E-04 -6,8E-03 8,3E-05 1,0E+00 7,7E-07 -3,5E+00 3,5E-04
SR305
0,3m
4,4E-03 4,6E-03 -5,6E-03 1,0E-04 1,0E+00 2,7E-05 -3,0E-01 1,8E-04
SR305
0,4m
7,7E-03 5,2E-03 -8,2E-04 8,7E-05 1,0E+00 6,2E-05 -4,0E-01 2,3E-04
SR305
0,5m
1,7E-02 7,8E-03 5,2E-03 1,2E-04 1,0E+00 1,6E-04 -5,0E-01 2,7E-04
SR305
0,75m
-1,7E-02 1,3E-02 -1,3E-04 2,8E-04 1,0E+00 2,6E-04 -7,5E-01 6,3E-04
SR305
1m
-1,7E-02 7,3E-03 6,6E-03 1,8E-04 1,0E+00 1,0E-04 -1,0E+00 7,7E-04
SR305
1,25m
-2,7E-02 1,2E-02 -2,3E-03 5,0E-04 1,0E+00 2,6E-04 -1,3E+00 1,3E-03
SR305
1,5m
-2,3E-02 2,0E-02 -2,9E-03 1,1E-03 1,0E+00 5,8E-04 -1,5E+00 2,8E-03
Table 8: Camera precision in terms of plane normal vector angles standard deviation and spherical variance.
Cam
dist
φ σ
φ
V C am
dist
φ σ
φ
V
D415
0,5m
9,0E+01 1,5E-02 5,3E-08 L515
1,5m
9,0E+01 3,1E-02 1,5E-07
D415
0,75m
8,9E+01 9,2E-03 6,5E-08 L515
1,75m
9,0E+01 1,9E-02 5,9E-08
D415
1m
8,9E+01 4,1E-02 2,9E-07 L515
2m
9,0E+01 2,4E-02 1,2E-07
D415
1,25m
8,9E+01 8,5E-02 1,3E-06 L515
2,5m
9,0E+01 8,6E-03 7,3E-08
D415
1,5m
8,9E+01 4,9E-02 4,7E-07 L515
3m
9,0E+01 1,4E-02 6,5E-08
D415
1,75m
8,9E+01 4,9E-02 5,3E-07 L515
3,5m
9,0E+01 6,2E-03 8,3E-08
D415
2m
8,9E+01 1,6E-01 4,6E-06 SR305
0,3m
9,0E+01 1,5E-01 1,1E-05
D415
2,5m
8,9E+01 7,9E-02 1,6E-06 SR305
0,4m
9,0E+01 3,0E-01 1,4E-05
D415
3m
8,9E+01 1,7E-01 5,6E-06 SR305
0,5m
8,9E+01 4,2E-01 3,1E-05
D415
3,5m
9,0E+01 1,0E-01 2,5E-06 SR305
0,75m
8,9E+01 7,0E-01 9,0E-05
L515
0,5m
9,0E+01 1,4E-02 2,1E-07 SR305
1m
8,9E+01 3,2E-01 2,7E-05
L515
0,75m
9,0E+01 1,2E-02 1,2E-07 SR305
1,25m
8,8E+01 5,6E-01 7,4E-05
L515
1m
9,0E+01 1,8E-02 2,0E-07 SR305
1,5m
8,9E+01 1,0E+00 2,1E-04
L515
1,25m
9,0E+01 4,8E-03 5,2E-08 — — — —
Intel RealSense SR305, D415 and L515: Experimental Evaluation and Comparison of Depth Estimation
369