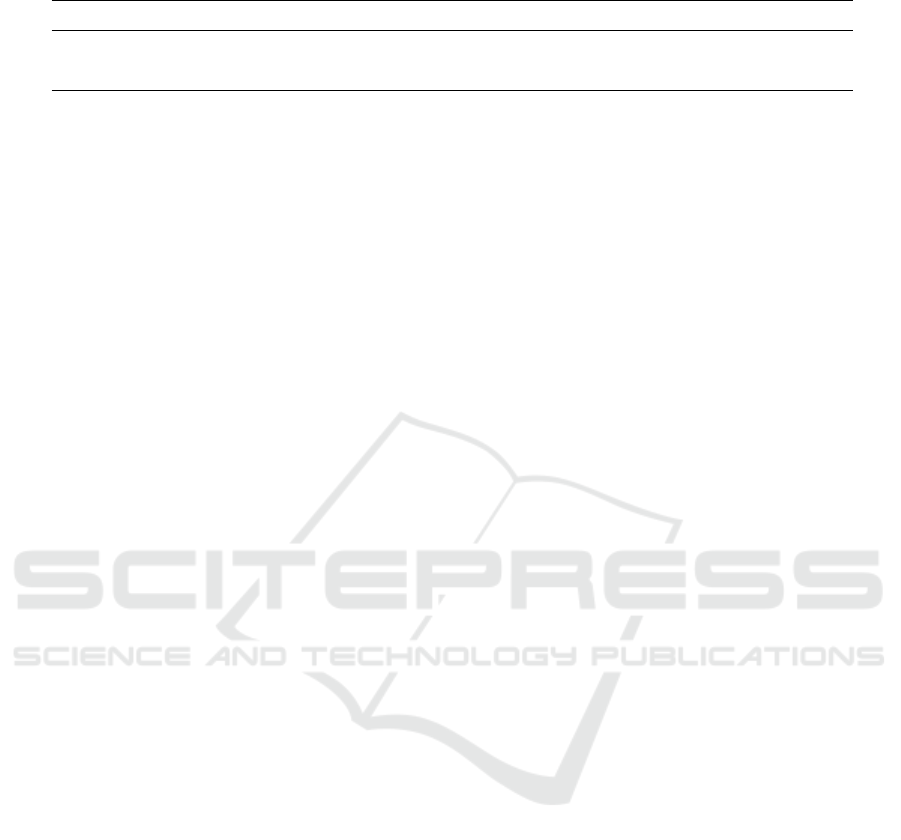
Table 2: Accuracy of three siamese networks on untrained traffic signs for three independent tests.
Test cases (distribution of images) SNN (Koch, 2015) SNN (Koch, 2015)
with VGG16 features
FCSNN
12 traffic sign classes, 66 faded and 162 errorless 43.3% 80.6% 92%
21 traffic sign classes, 92 covered and 195 errorless 7.5% 27.9% 28.9%
6 traffic sign classes, 34 scribbled and 54 errorless 9.4% 11.5% 25.8%
Weighted average 22.32% 43.12% 52.81%
REFERENCES
Bromley, J., Guyon, I., LeCun, Y., S
¨
ackinger, E., and Shah,
R. (1994). Signature verification using a” siamese”
time delay neural network. In Advances in neural in-
formation processing systems, pages 737–744.
Cao, J., Zhang, J., Wen, Z., Wang, N., and Liu, X. (2015).
Fabric defect inspection using prior knowledge guided
least squares regression. Multimedia Tools and Appli-
cations, 76:4141–4157.
Czimmermann, T., Ciuti, G., Milazzo, M., Chiurazzi, M.,
Roccella, S., Oddo, C. M., and Dario, P. (2020).
Visual-based defect detection and classification ap-
proaches for industrial applications—a survey. Sen-
sors, 20(5):1459.
Deshpande, A. M., Minai, A. A., and Kumar, M. (2020).
One-shot recognition of manufacturing defects in steel
surfaces. arXiv preprint arXiv:2005.05815.
Faghih-Roohi, S., Hajizadeh, S., N
´
u
˜
nez, A., Babuska, R.,
and De Schutter, B. (2016). Deep convolutional neu-
ral networks for detection of rail surface defects. In
2016 International joint conference on neural net-
works (IJCNN), pages 2584–2589. IEEE.
Gai, S. (2016). New banknote defect detection algorithm
using quaternion wavelet transform. Neurocomputing,
196:133–139.
He, D., Xu, K., and Zhou, P. (2019). Defect detection of hot
rolled steels with a new object detection framework
called classification priority network. Computers &
Industrial Engineering, 128:290–297.
Hoskere, V., Narazaki, Y., Hoang, T., and Spencer Jr, B.
(2018). Vision-based structural inspection using mul-
tiscale deep convolutional neural networks. arXiv,
pages arXiv–1805.
Jinsong Zhu, Chi Zhang, H. Q. . Z. L. (2020). Vision-based
defects detection for bridges using transfer learning
and convolutional neural networks. Structure and In-
frastructure Engineering, pages 1037–1049.
Kang, X., Yang, P., and Jing, J. (2015). Defect detec-
tion on printed fabrics via gabor filter and regular
band. Journal of Fiber Bioengineering and Informat-
ics, 8(1):195–206.
Koch, G. R. (2015). Siamese neural networks for one-shot
image recognition.
Lake, B. M., Salakhutdinov, R. R., and Tenenbaum, J.
(2013). One-shot learning by inverting a composi-
tional causal process. In Advances in neural infor-
mation processing systems, pages 2526–2534.
Mei, S., Yang, H., and Yin, Z. (2018). An unsupervised-
learning-based approach for automated defect inspec-
tion on textured surfaces. IEEE Transactions on In-
strumentation and Measurement, 67(6):1266–1277.
P. Liatsis, J.Y. Goulermas, X.-J. Z. . E. M. (2009). A flexible
visual inspection system based on neural networks.
International Journal of Systems Science, pages 173–
186.
Russakovsky, O., Deng, J., Su, H., Krause, J., Satheesh, S.,
Ma, S., Huang, Z., Karpathy, A., Khosla, A., Bern-
stein, M., et al. (2015). Imagenet large scale visual
recognition challenge. International journal of com-
puter vision, 115(3):211–252.
Wang, J., Ma, Y., Zhang, L., Gao, R. X., and Wu, D. (2018).
Deep learning for smart manufacturing: Methods
and applications. Journal of Manufacturing Systems,
48:144–156.
Weimer, D., Scholz-Reiter, B., and Shpitalni, M. (2016).
Design of deep convolutional neural network archi-
tectures for automated feature extraction in industrial
inspection. CIRP Annals, 65(1):417–420.
Xi, J., Shentu, L., Hu, J., and Li, M. (2017). Automated
surface inspection for steel products using computer
vision approach. Applied optics, 56(2):184–192.
Yang, L., Li, B., Yang, G., Chang, Y., Liu, Z., Jiang, B., and
Xiaol, J. (2019). Deep neural network based visual in-
spection with 3d metric measurement of concrete de-
fects using wall-climbing robot. In 2019 IEEE/RSJ In-
ternational Conference on Intelligent Robots and Sys-
tems (IROS), pages 2849–2854.
Yun, J. P., Lee, S. J., Koo, G., Shin, C., and Park, C.
(2019). Automatic defect inspection system for steel
products with exhaustive dynamic encoding algorithm
for searches. Optical Engineering, 58(2):023107.
Zhang, Y., Xing, Y., Gong, Y., Jin, D., Li, H., and Liu, F.
(2020). A variable-level automated defect identifica-
tion model based on machine learning. Soft Comput-
ing, 24(2):1045–1061.
Zhu, D., Pan, R., Gao, W., and Zhang, J. (2015). Yarn-dyed
fabric defect detection based on autocorrelation func-
tion and glcm. Autex research journal, 15(3):226–232.
Detecting Object Defects with Fusioning Convolutional Siamese Neural Networks
163