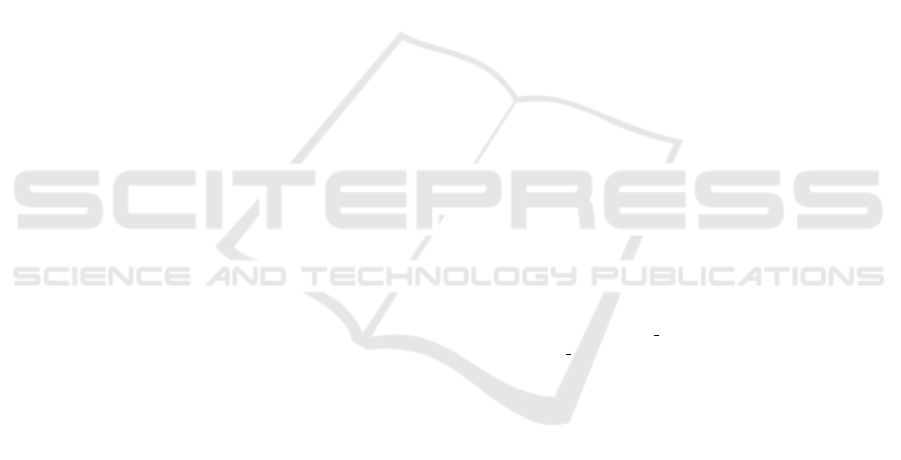
Comba, L., Biglia, A., Aimonino, D. R., Barge, P., Tortia,
C., and Gay, P. (2019). 2d and 3d data fusion for crop
monitoring in precision agriculture. In 2019 IEEE
International Workshop on Metrology for Agriculture
and Forestry (MetroAgriFor), pages 62–67. IEEE.
Crombez, N., Seulin, R., Morel, O., Fofi, D., and De-
monceaux, C. (2018). Multimodal 2d image to 3d
model registration via a mutual alignment of sparse
and dense visual features. In 2018 IEEE Inter-
national Conference on Robotics and Automation
(ICRA), pages 6316–6322. IEEE.
de Aguiar, M. A. P. F. (2015). 3d reconstruction from mul-
tiple rgb-d images with different perspectives.
Douarre, C., Crispim-Junior, C., Gelibert, A., Rousseau, D.,
and Tougne, L. (2019). A strategy for multimodal
canopy images registration. In 7th International Work-
shop on Image Analysis Methods in the Plant Sci-
ences.
Franzini, M., Ronchetti, G., Sona, G., and Casella, V.
(2019). Geometric and radiometric consistency of par-
rot sequoia multispectral imagery for precision agri-
culture applications. Applied Sciences, 9(24):5314.
Getman, A., Uvarov, T., Han, Y., Kim, B., Ahn, J., and Lee,
Y. (2007). Crosstalk, color tint and shading correction
for small pixel size image sensor. In International Im-
age Sensor Workshop, pages 166–169.
Hagen, N. (2014). Flatfield correction errors due to spectral
mismatching. Optical Engineering, 53(12):123107.
Islam, M. B. and Kabir, M. M. J. (2013). A new feature-
based image registration algorithm. Computer Tech-
nology and Application, 4(2).
Iwasaki, A. and Tonooka, H. (2005). Validation of a
crosstalk correction algorithm for aster/swir. IEEE
transactions on Geoscience and Remote Sensing,
43(12):2747–2751.
Jurado, J. M., Ortega, L., Cubillas, J. J., and Feito, F.
(2020). Multispectral mapping on 3d models and
multi-temporal monitoring for individual characteri-
zation of olive trees. Remote Sensing, 12(7):1106.
Kask, P., Palo, K., Hinnah, C., and Pommerencke, T.
(2016). Flat field correction for high-throughput imag-
ing of fluorescent samples. Journal of microscopy,
263(3):328–340.
Kokka, A., Pulli, T., Honkavaara, E., Markelin, L., K
¨
arh
¨
a,
P., and Ikonen, E. (2019). Flat-field calibration
method for hyperspectral frame cameras. Metrologia,
56(5):055001.
Li, W., Ogunbona, P., Shi, Y., and Kharitonenko, I. (2002).
Cmos sensor cross-talk compensation for digital cam-
eras. IEEE Transactions on Consumer Electronics,
48(2):292–297.
Limare, N., Lisani, J.-L., Morel, J.-M., Petro, A.-B., and
Sbert, C. (2011). Simplest color balance. Image Pro-
cessing On Line, 1.
Liu, H., Lee, S.-H., and Chahl, J. S. (2018). Registration of
multispectral 3d points for plant inspection. Precision
Agriculture, 19(3):513–536.
Ly, D. S., Demonceaux, C., Vasseur, P., and P
´
egard, C.
(2014). Extrinsic calibration of heterogeneous cam-
eras by line images. Machine vision and applications,
25(6):1601–1614.
Malvar, H. S., He, L.-w., and Cutler, R. (2004). High-
quality linear interpolation for demosaicing of bayer-
patterned color images. In 2004 IEEE International
Conference on Acoustics, Speech, and Signal Process-
ing, volume 3, pages iii–485. IEEE.
Meyers, G., Zhu, C., Mayfield, M., Tingley, D. D., Will-
mott, J., and Coca, D. (2019). Designing a vehi-
cle mounted high resolution multi-spectral 3d scanner:
Concept design. In Proceedings of the 2nd Workshop
on Data Acquisition To Analysis, pages 16–21.
Motohka, T., Nasahara, K. N., Oguma, H., and Tsuchida,
S. (2010). Applicability of green-red vegetation index
for remote sensing of vegetation phenology. Remote
Sensing, 2(10):2369–2387.
Nag, S. (2017). Image registration techniques: a survey.
arXiv preprint arXiv:1712.07540.
OECD (2020). Agriculture and the environ-
ment. https://www.oecd.org/agriculture/topics/
agriculture-and-the-environment.
Otsu, N. (1979). A threshold selection method from gray-
level histograms. IEEE transactions on systems, man,
and cybernetics, 9(1):62–66.
Palmero, C., Clap
´
es, A., Bahnsen, C., Møgelmose, A.,
Moeslund, T. B., and Escalera, S. (2016). Multi-modal
rgb-depth-thermal human body segmentation. Inter-
national Journal of Computer Vision, 118(2):217–
239.
Panda, S. S., Ames, D. P., and Panigrahi, S. (2010). Appli-
cation of vegetation indices for agricultural crop yield
prediction using neural network techniques. Remote
Sensing, 2(3):673–696.
Precision Agriculture, I. S. (2020). Precision ag defini-
tion - language modal. https://www.ispag.org/about/
definition.
Robotnik (2020). summit-xl. https://www.robotnik.eu/
mobile-robots/summit-xl.
ROS (2020a). camera calibration. http://wiki.ros.org/
camera calibration.
ROS (2020b). Robot operating system. https://www.ros.
org.
Salvi, J. et al. (1998). An approach to coded structured light
to obtain three dimensional information. Universitat
de Girona.
Sauget, V., Hubert, M., Faiola, A., and Tisserand, S. (2018).
Application note for cms camera and cms sensor
users: post-processing method for crosstalk reduction
in multispectral data and images. white paper, Silios
Technologies.
Schneider, N., Piewak, F., Stiller, C., and Franke, U. (2017).
Regnet: Multimodal sensor registration using deep
neural networks. In 2017 IEEE intelligent vehicles
symposium (IV), pages 1803–1810. IEEE.
Seibert, J. A., Boone, J. M., and Lindfors, K. K. (1998).
Flat-field correction technique for digital detectors. In
Medical Imaging 1998: Physics of Medical Imaging,
volume 3336, pages 348–354. International Society
for Optics and Photonics.
Silios (2020). Multispectral cameras cms series. https://
www.silios.com/cms-series.
Staranowicz, A., Brown, G. R., Morbidi, F., and Mariottini,
G. L. (2013). Easy-to-use and accurate calibration of
Real-time Multispectral Image Processing and Registration on 3D Point Cloud for Vineyard Analysis
397