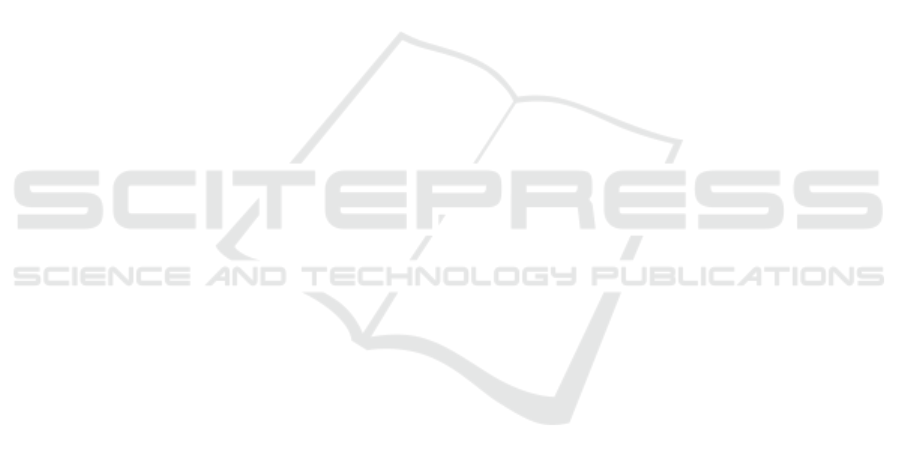
The convolutional neural networks as proposed
and tested with simulated images of baked anodes can
be used in a real industrial environment. As can be
seen with our experiments regarding formatting and
merging, the data can have a significant influence on
the accuracy of a neural network.
The capturing of training data is the biggest chal-
lenge in using machine learning techniques to tackle
a task of object tracking in an industrial context. To
generate examples for training it is necessary to track
the objects manually during production. But this
method allows to track objects that can not be tracked
with tags or chips because of the nature of the object
or the processing steps. The collected data can also be
used for tasks like predictive maintenance or quality
control.
Conclusive it can be said, that the proposed neural
network is the core of a system, that can track objects
through identifying them in images during a manufac-
turing process on a production line. Future work in-
cludes the development of a data storage and acquisi-
tion solution. Furthermore, more tests should be done
with different objects, and techniques of continuous
learning can be tested to enhance the neural network
with the capability to be retrained while already being
deployed.
ACKNOWLEDGEMENTS
The work of the academic authors were funded by
the federal state of North Rhine-Westphalia and the
European Regional Development Fund FKZ: ERFE-
040021.
REFERENCES
Abdel-Qader, I., Abudayyeh, O., and Kelly, M. (2003).
Analysis of edge-detection techniques for crack iden-
tification in bridges. Journal of Computing in Civil
Engineering - J COMPUT CIVIL ENG, 17.
Benhimane, S., Najafi, H., Grundmann, M., Malis, E.,
Genc, Y., and Navab, N. (2008). Real-time ob-
ject detection and tracking for industrial applications.
VISAPP 2008: Third International Conference on
Compter Vision Theory and Applications, 2.
Bromley, J., Guyon, I., LeCun, Y., S
¨
ackinger, E., and Shah,
R. (1993). Signature verification using a ”siamese”
time delay neural network. In Proceedings of the 6th
International Conference on Neural Information Pro-
cessing Systems, NIPS’93, page 737–744.
Brusey, J. and Mcfarlane, D. C. (2009). Effective rfid-
based object tracking for manufacturing. Interna-
tional Journal of Computer Integrated Manufactur-
ing, pages 638–647.
Cha, Y.-J., Choi, W., and Buyukozturk, O. (2017). Deep
learning-based crack damage detection using convo-
lutional neural networks. Computer-Aided Civil and
Infrastructure Engineering, 32:361–378.
Chicco, D. (2020). Siamese Neural Networks: An
Overview. Methods in molecular biology.
Chopra, S., Hadsell, R., and Lecun, Y. (2005). Learning a
similarity metric discriminatively, with application to
face verification. volume 1, pages 539– 546 vol. 1.
de Jes
´
us Rubio, J., Lughofer, E., Pieper, J., Cruz, P., Mar-
tinez, D. I., Ochoa, G., Islas, M. A., and Garcia, E.
(2021). Adapting h-infinity controller for the desired
reference tracking of the sphere position in the maglev
process. Information Sciences, 569:669–686.
Deshpande, A. M., Minai, A. A., and Kumar, M. (2020).
One-shot recognition of manufacturing defects in steel
surfaces. Procedia Manufacturing, 48:1064–1071.
48th SME North American Manufacturing Research
Conference, NAMRC 48.
Graves, A. (2013). Generating sequences with recurrent
neural networks.
Koch, G., Zemel, R., and Salakhutdinov, R. (2015).
Siamese neural networks for one-shot image recog-
nition. 32nd International Conference on Machine
Learning.
K
¨
uhl, N., Goutier, M., Baier, L., Wolff, C., and Martin, D.
(2020). Human vs. supervised machine learning: Who
learns patterns faster?
LeCun, Y., Bottou, L., Bengio, Y., and Haffner, P. (1998).
Gradient-based learning applied to document recogni-
tion. In Proceedings of the IEEE.
Mahamkali, N. and Ayyasamy, V. (2015). Opencv for com-
puter vision applications. National Conference on Big
Data and Cloud Computing.
Mahieu, P., Genin, X., Bouche, C., and Brismalein, D.
(2019). Carbon Block Tracking Package Based on Vi-
sion Technology, pages 1221–1228.
Minderer, M., Sun, C., Villegas, R., Cole, F., Murphy, K.,
and Lee, H. (2019). Unsupervised learning of object
structure and dynamics from videos. 33rd Conference
on Neural Information Processing Systems.
Scherer, D., M
¨
uller, A., and Behnke, S. (2010). Evalua-
tion of pooling operations in convolutional architec-
tures for object recognition. 20th International Con-
ference on Artificial Neural Networks (ICANN), pages
92–101.
Taigman, Y., Yang, M., Ranzato, M., and Wolf, L. (2014).
Deepface: Closing the gap to human-level perfor-
mance in face verification.
NCTA 2021 - 13th International Conference on Neural Computation Theory and Applications
350