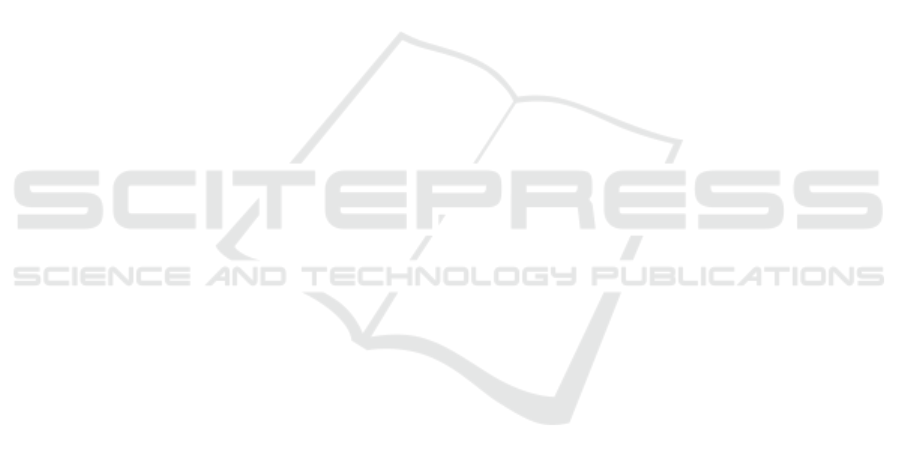
cipal component analysis. Industrial & Engineering
Chemistry Research, 49(17):7849–7857.
Bach, S., Binder, A., Montavon, G., Klauschen, F., M
¨
uller,
K.-R., and Samek, W. (2015). On pixel-wise explana-
tions for non-linear classifier decisions by layer-wise
relevance propagation. PLOS ONE, 10(7):1–46.
Bishop, C. (2011). Vacuum Deposition onto Webs, Films
and Foils. Elsevier Science.
Bishop, C. A. (2007). Vacuum deposition onto webs, films,
and foils. Second Edition, 91(2).
Bishop, C. A. and Mount, E. M. (2016). 15 - vacuum metal-
lizing for flexible packaging. In Wagner, J. R., editor,
Multilayer Flexible Packaging (Second Edition), Plas-
tics Design Library, pages 235 – 255. William Andrew
Publishing, 2nd ed. edition.
Borovec, J., Kybic, J., and Nava, R. (2017). Detection
and localization of drosophila egg chambers in mi-
croscopy images. In Wang, Q., Shi, Y., Suk, H.-I.,
and Suzuki, K., editors, Machine Learning in Medical
Imaging, pages 19–26, Cham. Springer International
Publishing.
Chollet, F. et al. (2015). Keras.
Dutta, S., Shen, H., and Chen, J. (2018). In situ predic-
tion driven feature analysis in jet engine simulations.
In 2018 IEEE Pacific Visualization Symposium (Paci-
ficVis), pages 66–75.
Fan, J. and Wang, Y. (2014). Fault detection and diagnosis
of non-linear non-gaussian dynamic processes using
kernel dynamic independent component analysis. In-
formation Sciences, 259:369–379.
I.F., G. (1993). Vacuum coating applications for snack food
packaging. 36th Ann. Tech. Conf. Proc. Society of Vac-
uum Coaters, pages 254—-258.
Kano, M. and Nakagawa, Y. (2008). Data-based pro-
cess monitoring, process control, and quality im-
provement: Recent developments and applications in
steel industry. Computers & Chemical Engineering,
32(1):12 – 24. Process Systems Engineering: Contri-
butions on the State-of-the-Art.
Lei, Y., Yao, X., Chen, W., Zhang, J., Mehnen, J., and Yang,
E. (2020). Multiple object detection of workpieces
based on fusion of deep learning and image process-
ing*. In 2020 International Joint Conference on Neu-
ral Networks (IJCNN), pages 1–7.
Liu, Y., Fan, Y., and Chen, J. (2017). Flame images for
oxygen content prediction of combustion systems us-
ing dbn. Energy & Fuels, 31(8):8776–8783.
Materials, A. (2016). Roll-to-roll web coating technology.
WEB Coating Products, 10.
Pajer, S., Streit, M., Torsney-Weir, T., Spechtenhauser, F.,
M
¨
oller, T., and Piringer, H. (2017). Weightlifter: Vi-
sual weight space exploration for multi-criteria deci-
sion making. IEEE Transactions on Visualization and
Computer Graphics, 23(1):611–620.
Perry, M. and Lentz, R. (2009). Susceptors in microwave
packaging. Development of Packaging and Products
for Use in Microwave Ovens, pages 207–236.
Qin, S. J. (2012). Survey on data-driven industrial process
monitoring and diagnosis. Annual Reviews in Control,
36(2):220 – 234.
Qin, S. J., Dong, Y., Zhu, Q., Wang, J., and Liu, Q. (2020).
Bridging systems theory and data science: A unifying
review of dynamic latent variable analytics and pro-
cess monitoring. Annual Reviews in Control, 50:29 –
48.
Shrikumar, A., Greenside, P., and Kundaje, A. (2017).
Learning important features through propagating ac-
tivation differences. In Precup, D. and Teh, Y. W.,
editors, Proceedings of the 34th International Con-
ference on Machine Learning, volume 70 of Pro-
ceedings of Machine Learning Research, pages 3145–
3153, International Convention Centre, Sydney, Aus-
tralia. PMLR.
Wongsuphasawat, K., Smilkov, D., Wexler, J., Wilson, J.,
Man
´
e, D., Fritz, D., Krishnan, D., Vi
´
egas, F. B.,
and Wattenberg, M. (2018). Visualizing dataflow
graphs of deep learning models in tensorflow. IEEE
Transactions on Visualization and Computer Graph-
ics, 24(1):1–12.
Wu, W., Zheng, Y., Chen, K., Wang, X., and Cao, N.
(2018). A visual analytics approach for equipment
condition monitoring in smart factories of process in-
dustry. In 2018 IEEE Pacific Visualization Symposium
(PacificVis), pages 140–149.
Wuest, T., Weimer, D., Irgens, C., and Thoben, K.-D.
(2016). Machine learning in manufacturing: advan-
tages, challenges, and applications. Production and
Manufacturing Research: An Open Access Journal,
4(1):3.
Xu, P., Mei, H., Ren, L., and Chen, W. (2017). Vidx: Visual
diagnostics of assembly line performance in smart fac-
tories. IEEE Transactions on Visualization and Com-
puter Graphics, 23(1):291–300.
VISAPP 2022 - 17th International Conference on Computer Vision Theory and Applications
386