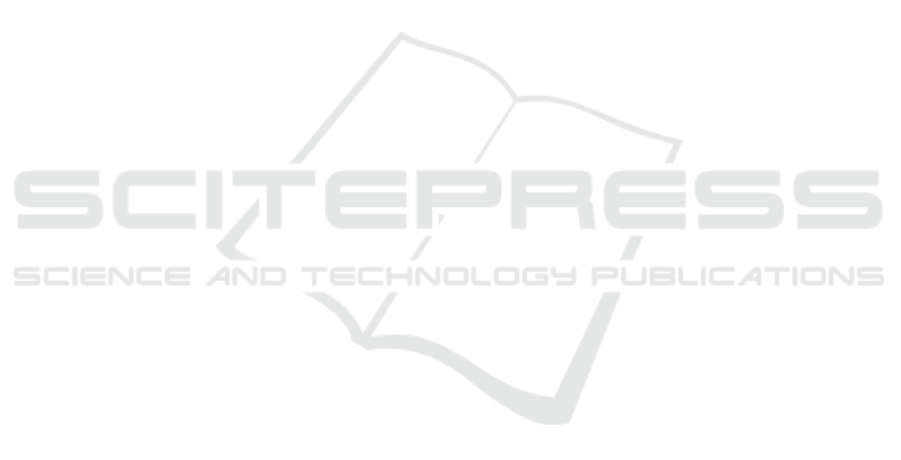
verted to images of the scanned surface. These are
called the Range Image and the Intensity Image (Fig-
ure 2). The Range data is good for detecting distresses
that are evident by a change in height, such as rut
depths, potholes, texture values and cracking. The in-
tensity data highlights different materials and picks up
objects like road markings and sealed cracking. Pave-
metrics has its own processing algorithms that use this
data to automatically detect distresses such as crack-
ing, potholes and patching. Patches are a common
pavement defect. Patches are used to provide a per-
manent restoration of the stability and quality of the
pavement, for example after installing, replacing, or
repairing underground utilities. Improperly installed
patches and deterioration of the surrounding pave-
ment, combined with challenging weather, can reduce
the life of a patch and turn patches into defects and
decrease the quality of a pavement.
The shape and quality of a patch can vary signifi-
cantly depending on the type of repair that is required.
Patches can be a temporary or a long term solution,
can use similar or different material to the existing
pavement, can cover a large area such as utility patch-
ing or cover a single pothole distress. The variety of
patching that is encountered is a huge challenge in de-
tecting pavement patches and often requires manual
involvement whereby engineers manually label/draw
bounding boxes around each patch.
In this study, we aim to address the patch detection
problem by answering the following research ques-
tion. “To what extent can object detection methods
accurately detect patches on images acquired using
3D laser profiling systems?” The dataset used in this
study was acquired from Pavement Management Sys-
tem (PMS) Ltd. PMS is a civil engineering consul-
tancy firm in Ireland, specializing in testing, evalua-
tion, and management of roads, airports, and ports.
2 RELATED WORK
Automatic pavement defect detection has attracted the
interest of many researchers and several studies pro-
pose various approaches to improve the current man-
ual visual inspection of pavements. 3D laser profiling
technology (Zhang et al., 2018) (Tsai and Chatterjee,
2018) is widely used in the assessment of pavement
surfaces which includes highways and airport run-
ways (Laurent et al., 2012) (Mulry et al., 2015). 3D
laser profiling technology such as LCMS provides de-
tailed information about pavement defects and auto-
matically detects pavement defects, including cracks,
raveling, rutting, roughness, etc. The detection of
pavement patches using LCMS requires manual in-
volvement and has not been significantly addressed.
The LCMS detects patching by finding areas of the
pavement that have similar smoothness (small vari-
ations in range data) and intensity that are different
to the surrounding pavement. This method of detec-
tion can have problems when it encounters bleeding
in the pavement surface, ravelling, areas of polished
aggregate, well installed patches using similar ma-
terial to the original pavement, brand new surfaces
and patches with sealed edges. Some researchers
propose different approaches to automatically detect
and localize pavement patches, but they use images
or videos acquired through conventional imaging de-
vices such as digital or smartphone cameras. How-
ever these common imaging devices are not com-
monly used in the professional pavement inspection
process. Therefore, it is necessary to build an auto-
matic patch detection system that can integrate into
the existing professional visual inspection systems.
For example, (Ajeesha and Kumar, 2016) propose an
automatic patch detection using an active contour seg-
mentation technique. The proposed method consists
of three main steps; 1) image pre-processing, 2) de-
tection of patches using active contour segmentation,
and 3) video tracking. In the first step, the image
is passed through multiple filters for image enhance-
ment and to remove unnecessary objects; in the sec-
ond step, patches from the intact pavement are seg-
mented using active contouring. Moreover, to trace
the patch in subsequent video frames, the detected
patches are passed to the kernel tracker to avoid de-
tection and report the patch only once. The pro-
posed method achieved an overall 82.75% precision
and 92.31% recall. Using traditional machine learn-
ing approach (Hadjidemetriou et al., 2018) propose a
method for the classification of patch and non-patch
images using Support Vector Machines (SVM). The
authors recorded road surface video frames using a
smartphone camera mounted inside and outside on
a vehicle. The method trains the SVM classifier to
distinguish patch and non-patch areas inside images.
The proposed classification system was evaluated on
video frames and achieved a detection accuracy of
87.3% and 82.5%, respectively.
Other techniques used in the automatic pavement
inspection process are based on the object detection
approach (Hassan et al., 2021). The goal of object
detection is to detect and localize pavement defects,
such as potholes, patches and cracks by drawing a
bounding box around the above defects. For exam-
ple, (Maeda et al., 2018) propose a multiple pavement
defect detection and localization system. The author
collected 9053 images using a smartphone camera
mounted on a vehicle windscreen. The proposed de-
VISAPP 2022 - 17th International Conference on Computer Vision Theory and Applications
414