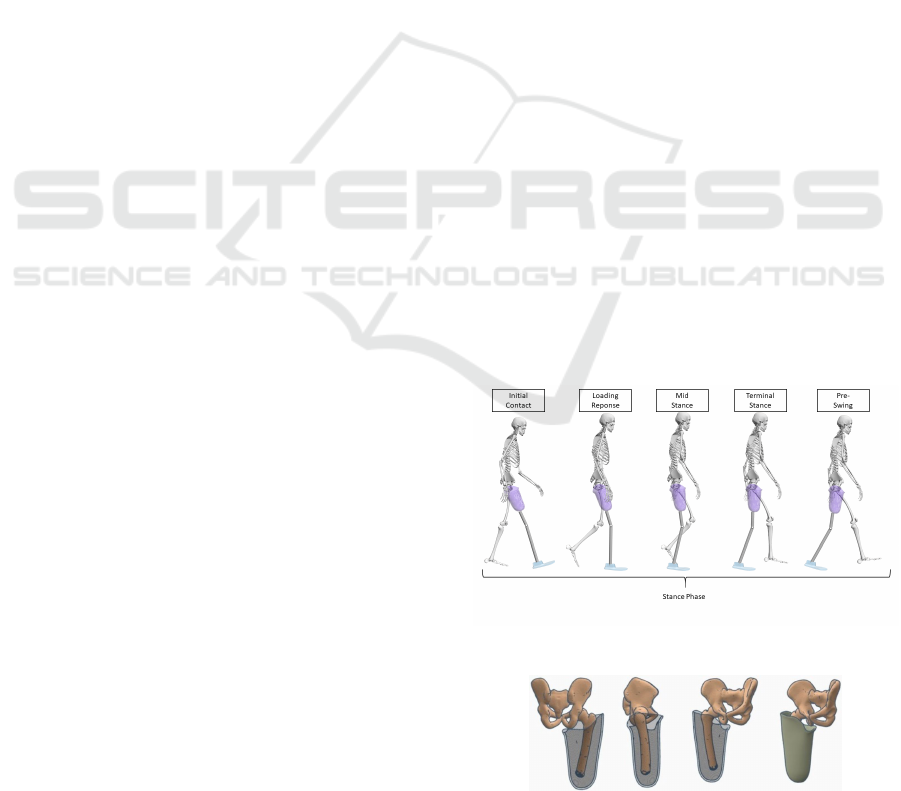
always a challenging task. Normally, direct sens-
ing of the pressure conditions is restricted by spe-
cific requirements on sensor deployment and perfor-
mance. For example, all modern pressure sensor tech-
nologies, including resistive transducer, piezoelectric
transducer, optical pressure transducer, and capac-
itive transducer (Bao., 2000), have their respective
disadvantages. For successful usage of such technolo-
gies, sensor testing and calibration become therefore
important. For the calibration of sensors, it is always
important to take the actual operational condition into
the consideration. One reason for this is that the
specific structural conditions of each individual pros-
thetic socket, relating for example to the curvature and
surface hardness, could lead to the problems of sen-
sor performance (Khodasevych et al., 2017). Differ-
ent bio-mechanical conditions and operational behav-
iors also lead to varying dynamic conditions that in
turn may interfere negatively with the sensor drift and
hysteresis, as well as other frequency response char-
acteristics (Buis and Convery, 1997). Moreover, sen-
sor re-calibration could also be necessary in order to
compensate for the drift over life cycle.
This paper presents an approach to a novel
mechatronics-twin framework for prosthetic devices
is similar to the notion of digital-twin in regard to the
replication of a physical target system on the basis
of measurements (Boschert and Rosen, 2016). The
approach addresses however in particular the chal-
lenge of complex biomechanical dynamics of pros-
thesis operation as well as the need of physical replica
for data generation and sensor calibration. Clearly,
any approaches that rely on repeated experimentation
on the amputees will not be preferable. This would
in the worst case cause further trauma to the am-
putees. Therefore, in the mechatronics-twin frame-
work, a six-degree-of-freedom parallel manipulator
referred to as SP (Stewart Platform) has been adopted
for a refinement of the digital virtual replication given
by modeling and simulation.
Since being firstly introduced in 1949, various SP
based solutions are widely used as the motion base
for antenna positioning systems, machine tool tech-
nology, flight simulators, etc. Today, there are over
1400 research articles about manipulators analysis
and design. See e.g. (Furqan et al., 2017), (Wapler
et al., 2003), (Grace et al., 1993), (Brandt et al.,
1999) and (Fichter et al., 2008). Our approach adopts
a PID (Proportional–Integral–Derivative) strategy to
the motion control of SP, with the control refer-
ence generated by biomechanical simulation and real-
time feedback from the operation of SP. Similar ap-
proaches to SP control can be found in (S¸umnu et al.,
2017) and (Rossell et al., 2015).
3 BIOMECHANICAL
MODELLING AND
SIMULATION
This technical step aims at eliciting the most fun-
damental operational characteristics of a prosthetic
device as an integral part of amputee. Within the
mechatronics-twin framework, it provides the support
for estimating the piston-forces and moments within
the amputee stump-socket assembly during walking.
Knowledge of such physical interactions is essential
for more detailed analysis of stump and prosthesis dy-
namics. All tasks are based on OpenSim, which is an
open source tool for the modeling, simulating and an-
alyzing of neuromusculoskeletal systems (Delp et al.,
2007).
The work starts with a quantification of amputee
body geometries, sizes of the pelvis-femur structure
and prosthetic socket based on a combination of mea-
surement and estimation. These geometries are not
only essential for visual representation of the bod-
ies, but are also important in the estimation of piston-
forces with inverse dynamics when combined with a
configuration of associated body masses. To achieve
a good scaling in biomechanical models, proper mea-
surement of the limbs are required to determine the
joints connecting the various bodies. The masses of
the residual limb are initially approximated by equat-
ing the volumetric density of the default healthy limb
to the residual limb. The Static Optimisation Tool of
OpenSim is then used for a further adjustment of these
masses regarding the kinematics and ground reaction
forces of test-subject. A similar approach is used
to develop a transfemoral biomechanical model in
Figure 2: A snapshot of biomechanical model and related
gait phases.
Figure 3: Positioning femur in a transfemoral socket model.
BIODEVICES 2022 - 15th International Conference on Biomedical Electronics and Devices
76