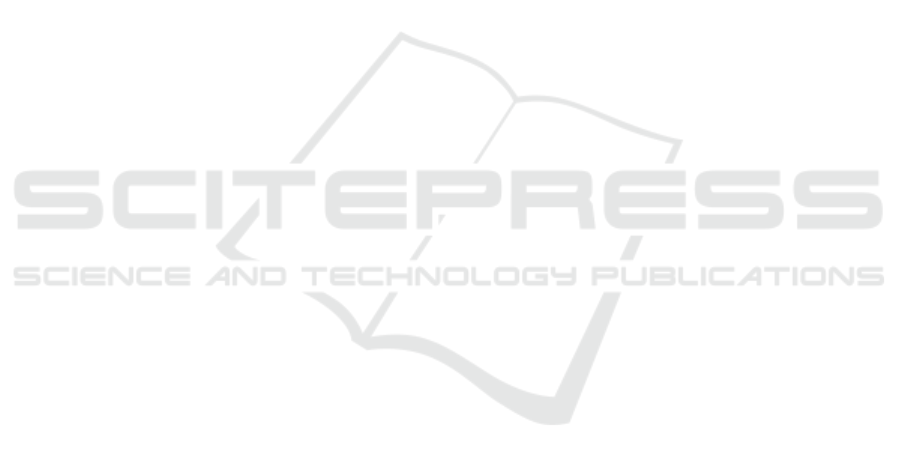
dustrie 4.0.
Arens, D., Hopfgartner, T., Jensen, T., Lamping, M.,
Pieper, M., and Seger, D. (2006). Packaging machine
language v3. 0 mode & states definition document.
OMAC Motion for Packaging Working Group.
Bader, S., Barnstedt, E., Bedenbender, H., Berres, B., Bill-
mann, M., and Boss, B. (2022). Details of the asset
administration shell: Part 1: The exchange of infor-
mation between partners in the value chain of indus-
trie 4.0.
Bayha, A., Bock, J., Boss, B., Diedrich, C., and Malakuti, S.
(2020). Describing capabilities of industrie 4.0 com-
ponents.
Bedenbender, H., Bock, J., Boss, B., Diedrich, C., Garrels,
K., Graf Gatterburg, A., Heidrich, K., Hillermeier, O.,
Rauscher, B., Sauer, M., Schmidt, J., Werner, T., and
Zimmermann, P. (2020). Verwaltungsschale in der
praxis: Wie definiere ich teilmodelle, beispielhafte
teilmodelle und interaktion zwischen verwaltungss-
chalen. Plattform Industrie 4.0, Discussion Paper.
Belyaev, A., Diedrich, C., Espen, D., L
¨
udicke, B., Miny,
T., Mrosowski, A., M
¨
uller, M., Neidig, J., Pollmeier,
S., Reich, J., R
¨
ubel, P., Sauer, M., Schr
¨
oder, T., Ul-
rich, O., Urban, C., Vojanec, B., and Wieczorek, M.
(2021). Vws-referenzmodellierung: Exemplarische
modellierung einer fertigungstechnischen anlage mit
aasx package explorer auf basis des vws-metamodells.
BMBF (2019). Basys 4.0 in der anwendung - verbundpro-
jekt openbasys 4.0.
Bouter, C., Pourjafarian, M., Simar, L., and Wilterdink, R.
(2021). Towards a comprehensive methodology for
modelling submodels in the industry 4.0 asset admin-
istration shell. In 2021 IEEE 23rd Conference on
Business Informatics (CBI), volume 2, pages 10–19.
IEEE.
Cavalieri, S. and Salafia, M. G. (2020). Asset administra-
tion shell for plc representation based on iec 61131–3.
IEEE Access, 8:142606–142621.
Di Orio, G., Mal
´
o, P., and Barata, J. (2019). Novaas: A ref-
erence implementation of industrie4. 0 asset adminis-
tration shell with best-of-breed practices from it en-
gineering. In IECON 2019-45th Annual Conference
of the IEEE Industrial Electronics Society, volume 1,
pages 5505–5512. IEEE.
Dorofeev, K. and Zoitl, A. (2018). Skill-based engineer-
ing approach using opc ua programs. In 2018 IEEE
16th international conference on industrial informat-
ics (INDIN), pages 1098–1103. IEEE.
Fathizadeh, M., Yen, J., and Werthman, M. (2013). Inte-
gration of packml in engineering education. In Pro-
ceedings of the World Congress on Engineering and
Computer Science, volume 1.
Grothoff, J., Porta, D., Espen, D., and Haque, A. (2021).
Basyx/documentation/api/controlcomponent.
Gr
¨
uner, S., David, A., Motsch, W., Grothoff, J., Fachinger,
G., Miny, T., Schaller, G., Hamann, T., Johann, P., and
Kr
¨
amer, N. (2021). D-4.8 entwurf einer generischen
plug & produce prozedur.
ISA (2015). Isa-tr88.00.02:2015.
Koulamas, C. and Kalogeras, A. (2018). Cyber-physical
systems and digital twins in the industrial inter-
net of things [cyber-physical systems]. Computer,
51(11):95–98.
Kuhn, T., Schnicke, F., and Antonino, P. O. (2020). Service-
based architectures in production systems: Chal-
lenges, solutions & experiences. In 2020 ITU Kaleido-
scope: Industry-Driven Digital Transformation (ITU
K), pages 1–7. IEEE.
L
¨
uder, A., Behnert, A.-K., Rinker, F., and Biffl, S. (2020).
Generating industry 4.0 asset administration shells
with data from engineering data logistics. In 2020
25th IEEE International Conference on Emerging
Technologies and Factory Automation (ETFA), vol-
ume 1, pages 867–874. IEEE.
Mu
ˇ
si
ˇ
c, G. (2015). A low-cost packml-based control
solution for a modular production line. IFAC-
PapersOnLine, 48(10):184–189.
OMAC (2009). Packml implementation guide.
Platform, E. B. (2021). Ready-to-use components and ex-
tendable software development kits (sdk).
Rayment, M. (2004). Flexible motion control using iec
61131-3. In 2004 Mini Symposia UKACC Control,
pages 27–36. IET.
Repository, G. (2022). A viewer/editor for the asset admin-
istration shell.
Sch
¨
afer, S., Sch
¨
ottke, D., K
¨
ampfe, T., Ralinovski, K.,
Tauber, B., and Lehmann, R. (2021). Design and de-
ployment of digital twins for programmable logic con-
trollers in existing plants. In IN4PL, pages 145–150.
Sch
¨
afer, S., Sch
¨
ottke, D., K
¨
ampfe, T., Lachmann, O., Ziel-
storff, A., and Tauber, B. (2022). Migration and syn-
chronization of plant segments with asset administra-
tion shells. unpublished - will be published in the
ETFA2022 conference proceeding.
Wallner, B., Trautner, T., Pauker, F., and Kittl, B. (2021).
Evaluation of process control architectures for agile
manufacturing systems. Procedia CIRP, 99:680–685.
Ye, X., Hong, S. H., Song, W. S., Kim, Y. C., and Zhang,
X. (2021). An industry 4.0 asset administration shell-
enabled digital solution for robot-based manufactur-
ing systems. IEEE Access, 9:154448–154459.
IN4PL 2022 - 3rd International Conference on Innovative Intelligent Industrial Production and Logistics
84