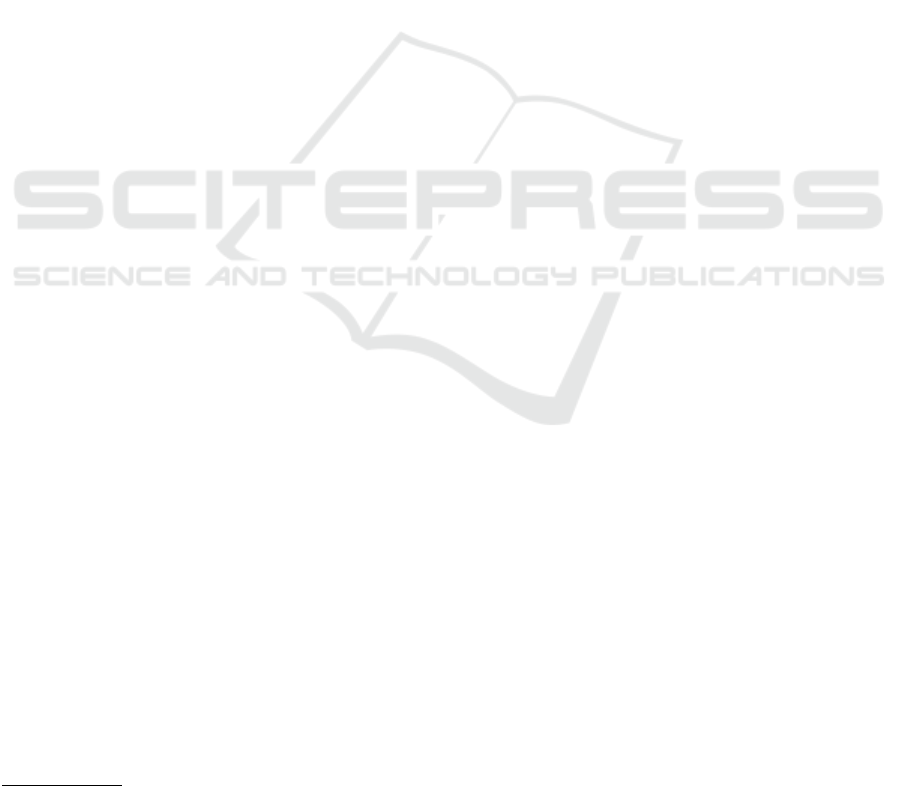
5 CONCLUSIONS
In the manufacturing industry, production line break-
downs cost ∼ 50,000 US$ per hour, worldwide. Fur-
ther, maximum availability of machines and systems
must be preserved in order to meet the demands of
Industry 4.0. This paper presented a scalable data
pipeline along with several condition monitoring and
predictive maintenance techniques to detect anoma-
lous behaviour. The proposed techniques may help
manufacturing industry to reduce unplanned down-
time due to asset failures. These techniques are prac-
tical, easy-to-use and easy-to-maintain. In addition,
they work well in the case of streaming data, unla-
beled data and/or lack of historical data.
In the future, the proposed data pipeline as well
as condition monitoring and predictive maintenance
techniques presented in this paper should be deployed
to production in SMEs.
ACKNOWLEDGEMENTS
Special thanks to Kai Waehner
17
for his inspirational
tutorials, videos and GitHub repository especially in
relation to Kafka Streams and KSQL by Confluent
18
.
In addition, most of the CM and PdM techniques pre-
sented in this paper are based on the ideas suggested
by Kai Waehner.
REFERENCES
Boniol, P., Paparrizos, J., Palpanas, T., and Franklin,
M. J. (2021). Sand: streaming subsequence anomaly
detection. Proceedings of the VLDB Endowment,
14(10):1717–1729.
Butler, Q., Ziada, Y., Stephenson, D., and Gadsden, S. A.
(2022). Condition monitoring of machine tool feed
drives: A review. Journal of Manufacturing Science
and Engineering, 144(10):100802.
Chatterjee, A. and Ahmed, B. S. (2022). Iot anomaly detec-
tion methods and applications: A survey. Internet of
Things, page 100568.
de Rizzio, R. (2021). Apache kafka and time series.
Available online at: https://rogerio-rizzio.medium.
com/apache-kafka-and-time-series-7f1a9db47053.
Dinardo, G., Fabbiano, L., and Vacca, G. (2018). A smart
and intuitive machine condition monitoring in the in-
dustry 4.0 scenario. Measurement, 126:1–12.
Guo, J. and Shen, Y. (2022). Online anomaly detection of
industrial iot based on hybrid machine learning ar-
17
https://www.kai-waehner.de
18
https://www.confluent.io
chitecture. Computational Intelligence and Neuro-
science.
Hsieh, R. J., Chou, J., and Ho, C. H. (2019). Unsuper-
vised online anomaly detection on multivariate sens-
ing time series data for smart manufacturing. In 12th
Conference on Service-Oriented Computing and Ap-
plications. IEEE.
Iftikhar, N., Baattrup-Andersen, T., Nordbjerg, F. E., and
Jeppesen, K. (2020). Outlier detection in sensor data
using ensemble learning. Procedia Computer Science,
176:1160–1169.
Iftikhar, N., Nordbjerg, F. E., Baattrup-Andersen, T., and
Jeppesen, K. (2019). Industry 4.0: sensor data analy-
sis using machine learning. In International Confer-
ence on Data Management Technologies and Applica-
tion, pages 37–58. Springer.
Lin, J. (2017). The lambda and the kappa. IEEE Internet
Computing, 21(5):60–66.
Liu, X., Iftikhar, N., Nielsen, P. S., and Heller, A. (2016).
Online anomaly energy consumption detection using
lambda architecture. In International Conference on
Big Data Analytics and Knowledge Discovery, pages
193–209. Springer.
Marz, N. and Warren, J. (2015). Big Data: Principles and
Best Practices of Scalable Real-time Data Systems.
Manning Publications Co., New York.
Paolanti, M., Romeo, L., Felicetti, A., Mancini, A., Fron-
toni, E., and Loncarski, J. (2018). Machine learn-
ing approach for predictive maintenance in industry
4.0. In 14th IEEE/ASME International Conference
on Mechatronic and Embedded Systems and Applica-
tions. IEEE.
Pimenov, D. Y., Bustillo, A., Wojciechowski, S., Sharma,
V. S., Gupta, M. K., and Kunto
˘
glu, M. (2022). Artifi-
cial intelligence systems for tool condition monitoring
in machining: Analysis and critical review. Journal of
Intelligent Manufacturing, 109(3):1–43.
Pittino, F., Puggl, M., Moldaschl, T., and Hirschl, C. (2020).
Automatic anomaly detection on in-production manu-
facturing machines using statistical learning methods.
Sensors, 20(8):2344.
Serin, G., Sener, B., Ozbayoglu, A. M., and Unver, H. O.
(2020). Review of tool condition monitoring in ma-
chining and opportunities for deep learning. The In-
ternational Journal of Advanced Manufacturing Tech-
nology, 109(3):953–974.
Waehner, K. (2021). Condition monitoring and predictive
maintenance with apache kafka. https://www.kai-
waehner.de/blog/2021/10/25/apache-kafka-condition-
monitoring-predictive-maintenance-industrial-iot-
digital-twin.
Weaver, S., Dai, D., Stauber, C. E., and Luo, R. (2014). The
urban health index: a handbook for its calculation and
use.
IN4PL 2022 - 3rd International Conference on Innovative Intelligent Industrial Production and Logistics
144