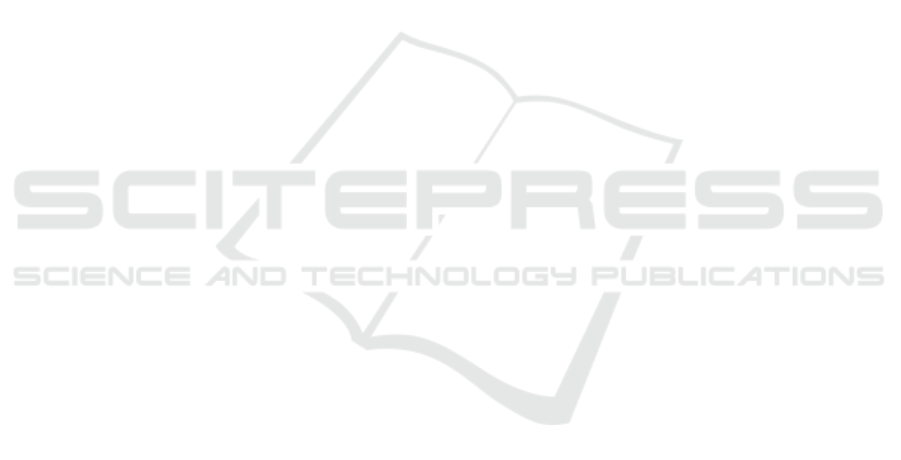
with industry map sampling distance 1 m. If the posi-
tion is provided with the required power within cov-
erage map, but the received signal power at these po-
sitions is less than the receiver sensitivity, the class
assignment is positive. If the positions is located out-
side the coverage map and has a large distance to the
transmitter or has received signal power more than the
receiver sensitivity, then the decision is for negative
class. In this way, SVC inspects the industry map at
each position with sampling distance of 1m.
Channel Data Generation. In training, validation
as well as model testing phase, the SVC needs chan-
nel measurement information in the industry envi-
ronment. This is generated using the channel mea-
surements in the QUAsi Deterministic RadIo chan-
nel GenerAtor (QuaDRiGa) model in industry sce-
nario. Multiple communication models are simulated
for line-of-sight (LOS) and non-line-of-sight (NLOS)
scenarios. The power map is generated under con-
sideration of all possible signal propagation path loss,
shadowing, multi path fading effect. Several differ-
ent power maps can be obtained for the same industry
layout with different communication system param-
eters. After that, each sampled position has to be la-
beled from prospective of the distance path loss power
map. Thereafter, the model is trained and L-fold is
validated.
Support Vector Classifier: the SVC can be con-
sidered as a function between input information and
output position classes. The input information is the
industrial wireless channel information, which is con-
sidered as a feature matrix [X] = x
j
(i); i = (1 : m); j =
(1 : n), whereas m is the number of features and n
is the number of positions to be considered. As the
output, the system must be able to assign the posi-
tion from industrial map in binary class assignments
y = {+1, −1}. The separation of the two classes
requires a nonlinear hyperplane. Moreover, a cor-
respondent linear separated hyperplane is preferred
based on the mapping Φ(x
i
) in the infinite dimension
using the radial basis kernel. With the kernel func-
tion, the nonlinear separation level can be achieved
without increasing the dimension value m of the vec-
tor space, i. e., either a mapping Φ(x
1
, x
2
) to the height
dimension space is used until linear separation is pos-
sible, or a kernel function K(x
i
, x
j
) = Φ(x
i
)
T
· Φ(x
j
)
is used, which has the condition that the kernel func-
tion must be an inner product in at least one feature
space. This will avoid the internal product in the op-
timization problem in the height-dimensional space.
The penalty parameter C represents the inverse effect
of the regularization parameter. The penalty param-
eter C and the kernel parameter σ can be optimally
configured using L-fold cross validation.
4 AGV TRAJECTORY PLANER
WITH BLIND SPOTS
AVOIDANCE SYSTEM
In this section, the AGV edge cloud control system
is considered. As shown in Figure 2, the AGVs are
moving on the factory floor. Due to low computation
power of the AGVs, they do not feature capabilities
for path planning or trajectory following. Any AGV
expects the control input signals to be provided by ex-
ternal control system, which is located on the edge
cloud. The AGVs follow the control signals and give
a feedback on their control states. The power consum-
ing computations of control signals are performed on
the edge cloud. Thus, edge cloud control system has
full control over the behaviour of the AGVs.
Edge cloud has to use wireless channel to com-
municate with AGVs, since these are highly mobile
platforms. In this case, wired communication chan-
nel is not feasible. However, the wireless link is the
critical part of the system, since both up- as well as
downlink may suffer deep fading effects, which af-
fects the whole control loop. This behaviour might be
mitigated by means of AI based blind spots detection
algorithm described in section 3.
The coverage blind spots elimination (CBSE) sys-
tem is the trajectory planning algorithm, which takes
periodic blind spots forecast updates into account in
order to avoid the communication link outage. In
following, detailed description of the CBSE system
components is presented.
Reference Trajectory Planning. Initially, a start as
well as a destination position, which must be reached
within a given time T , is reported to the controller.
The AGV has to follow a shortest blind spot free path
to the destination. Trajectory planning starts with a
creation of a binary occupation map of the factory
floor. As can be seeing in Figure 3, white areas can
be accessed by an AGV, whereas black areas rep-
resent obstacles. Those are physical obstacles such
as walls, pillars, machines etc. Besides, blind spot
areas are also declared as obstacles to be avoided.
Thereby, blind spot detection algorithm provides an
up-to-date blind spot forecast. Afterwards, proba-
bilistic roadmap (PRM) algorithm (Kavraki et al.,
1996) is utilised in order to find the optimal trajectory
from start to the destination. This path is represented
with the red color in Figure 3.
ETCIIM 2022 - International Workshop on Emerging Trends and Case-Studies in Industry 4.0 and Intelligent Manufacturing
310