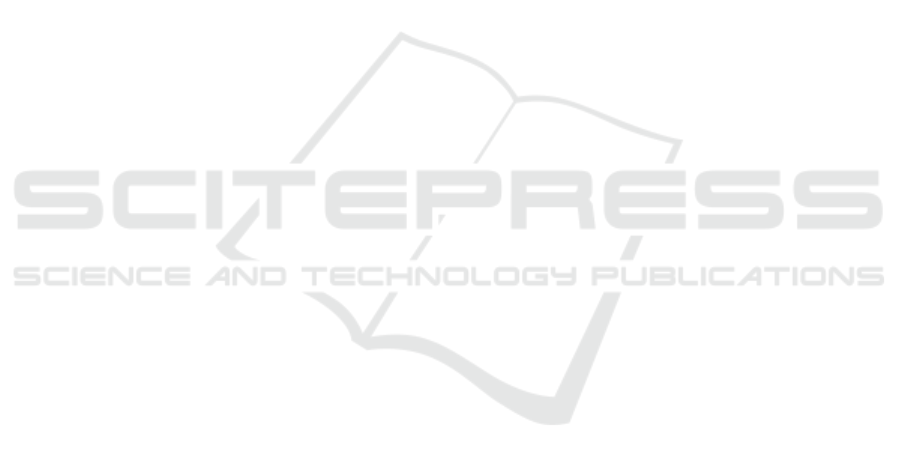
pipeline that can be used for automatizing the current
STS cranes.
6 FUTURE WORK
Future work includes extending the inspection tasks
in order to automatize even further the current man-
ual tasks and increase the performance of the cur-
rent ones, as some still have room for improvements.
Also, we would like to investigate state-of-the art
deep learning models using temporal information in
order to provide better results to the heuristic algo-
rithm. In addition, we would like to study with an
extended research regarding the potential domain gap
between synthetic data and real data.
ACKNOWLEDGEMENTS
This work has been partially done under the frame
of the project 5GLOGINNOV (Grant agreement ID:
957400) funded by the European Comission under
the H2020-ICT-2018-20 programme, within the topic
ICT-42-2020 - 5G PPP – 5G core technologies inno-
vation.
REFERENCES
Aranjuelo, N., Garc
´
ıa, J., Unzueta, L., Garc
´
ıa, S., Elordi,
U., and Otaegui, O. (2021). Building synthetic simu-
lated environments for configuring and training multi-
camera systems for surveillance applications. In VISI-
GRAPP (5: VISAPP), pages 80–91.
Baek, Y., Lee, B., Han, D., Yun, S., and Lee, H. (2019).
Character region awareness for text detection. In
CVPR, pages 9365–9374.
Bahrami, Z., Zhang, R., Rayhana, R., Wang, T., and Liu,
Z. (2020). Optimized deep neural network architec-
tures with anchor box optimization for shipping con-
tainer corrosion inspection. In 2020 IEEE SSCI, pages
1328–1333. IEEE.
Bu, W., Yan, S., Chen, J., Yang, C., and Liu, C. (2018).
Visual recognition of container number with arbitrary
orientations based on deep convolutional neural net-
work. In 2018 10th IHMSC, volume 2, pages 204–
207. IEEE.
Cai, Z. and Vasconcelos, N. (2019). Cascade r-cnn: high
quality object detection and instance segmentation.
IEEE transactions on pattern analysis and machine
intelligence, 43(5):1483–1498.
Chen, K., Wang, J., Pang, J., Cao, Y., Xiong, Y., Li, X.,
Sun, S., Feng, W., Liu, Z., Xu, J., Zhang, Z., Cheng,
D., Zhu, C., Cheng, T., Zhao, Q., Li, B., Lu, X., Zhu,
R., Wu, Y., Dai, J., Wang, J., Shi, J., Ouyang, W.,
Loy, C. C., and Lin, D. (2019). MMDetection: Open
mmlab detection toolbox and benchmark.
Cort
´
es, A., Rodr
´
ıguez, C., V
´
elez, G., Barandiar
´
an, J., and
Nieto, M. (2022). Analysis of classifier training
on synthetic data for cross-domain datasets. IEEE
Transactions on Intelligent Transportation Systems,
23(1):190–199.
Delgado, G., Cort
´
es, A., Garc
´
ıa, S., Aranjuelo,
N., Loyo, E., and Berasategi, M. (2022).
Seafront: Synthetic dataset for visual container
inspection. https://datasets.vicomtech.org/di21-
seafront/readme.txt.
Feng, X., Wang, Z., and Liu, T. (2020a). Port container
number recognition system based on improved yolo
and crnn algorithm. In 2020 AIEA, pages 72–77.
IEEE.
Feng, X. Q., Liu, Q., and Wang, Z. W. (2020b). Port con-
tainer number detection based on improved east algo-
rithm. In Journal of Physics: Conference Series, vol-
ume 1651, page 012088. IOP Publishing.
Filom, S., Amiri, A. M., and Razavi, S. (2022). Applica-
tions of machine learning methods in port operations–
a systematic literature review. Transportation Re-
search Part E: Logistics and Transportation Review,
161:102722.
He, K., Zhang, X., Ren, S., and Sun, J. (2016). Deep resid-
ual learning for image recognition. In CVPR, pages
770–778.
ISO (2022). ISO 6346:2022 Freight containers — Coding,
identification and marking. International Organization
for Standardization.
Jocher, G., Stoken, A., Chaurasia, A., Borovec, J.,
NanoCode012, TaoXie, Kwon, Y., Michael, K.,
Changyu, L., Fang, J., V, A., Laughing, tkianai,
yxNONG, Skalski, P., Hogan, A., Nadar, J., imyhxy,
Mammana, L., AlexWang1900, Fati, C., Montes, D.,
Hajek, J., Diaconu, L., Minh, M. T., Marc, albinx-
avi, fatih, oleg, and wanghaoyang0106 (2021). ul-
tralytics/yolov5: v6.0 - YOLOv5n ’Nano’ models,
Roboflow integration, TensorFlow export, OpenCV
DNN support.
Li, X., Liu, Q., Wang, J., and Wu, J. (2020). Container dam-
age identification based on fmask-rcnn. In Interna-
tional Conference on Neural Computing for Advanced
Applications, pages 12–22. Springer.
Verma, A., Sharma, M., Hebbalaguppe, R., Hassan, E., and
Vig, L. (2016). Automatic container code recognition
via spatial transformer networks and connected com-
ponent region proposals. In 2016 15th ICMLA, pages
728–733. IEEE.
Wang, Z., Gao, J., Zeng, Q., and Sun, Y. (2021). Multi-
type damage detection of container using cnn based
on transfer learning. Mathematical Problems in Engi-
neering, 2021.
Zhiming, W., Wuxi, W., and Yuxiang, X. (2019). Automatic
container code recognition via faster-rcnn. In 2019 5th
ICCAR, pages 870–874. IEEE.
Pipeline for Visual Container Inspection Application using Deep Learning
411