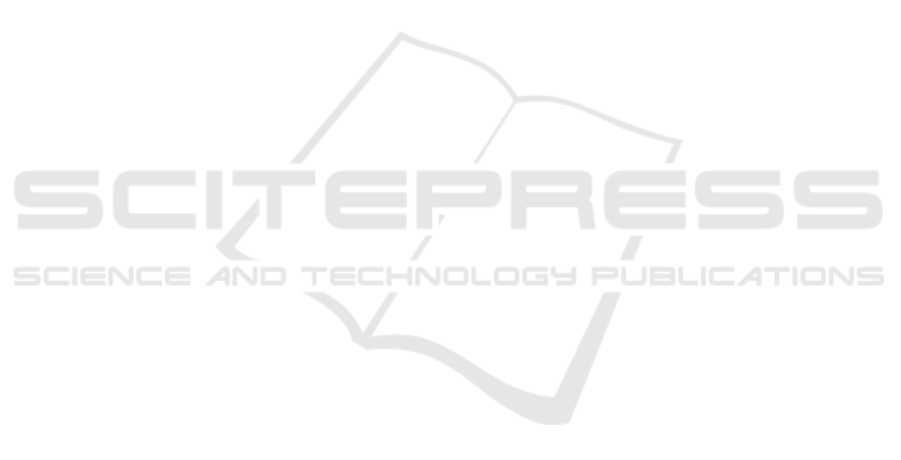
duction of Semantic Web technologies to represent
data on which services are built, as well as standard
service taxonomies. The introduction of an infrastruc-
ture based on micro-services and containers as soft-
ware architectural patterns will also be investigated.
REFERENCES
Alexopoulos, K., Sipsas, K., Xanthakis, E., Makris, S., and
Mourtzis, D. (2018). An industrial internet of things
based platform for context-aware information services
in manufacturing. International Journal of Computer
Integrated Manufacturing, 31(11):1111–1123.
Bagozi, A., Bianchini, D., and Rula, A. (2022). Multi-
perspective data modelling in cyber physical produc-
tion networks: Data, services and actors. Data Science
and Engineering, pages 1–20.
Cagnin, R. L., Guilherme, I. R., Queiroz, J., Paulo, B., and
Neto, M. F. (2018). A multi-agent system approach
for management of industrial iot devices in manufac-
turing processes. In 2018 IEEE 16th International
Conference on Industrial Informatics (INDIN), pages
31–36.
Catarci, T., Firmani, D., Leotta, F., Mandreoli, F., Mecella,
M., and Sapio, F. (2019). A conceptual architecture
and model for smart manufacturing relying on service-
based digital twins. In 2019 IEEE International Con-
ference on Web Services, ICWS 2019, Milan, Italy,
July 8-13, 2019, pages 229–236. IEEE.
Derhamy, H., Eliasson, J., and Delsing, J. (2019). Sys-
tem of system composition based on decentralized
service-oriented architecture. IEEE Systems Journal,
13(4):3675–3686.
Glock, T., Betancourt, V. P., Kern, M., Liu, B., Reiß, T.,
Sax, E., and Becker, J. (2019). Service-based indus-
try 4.0 middleware for partly automated collaborative
work of cranes. In 2019 8th International Conference
on Industrial Technology and Management (ICITM),
pages 229–235. IEEE.
Harrison, R., Vera, D., and Ahmad, B. (2021). A Con-
nective Framework to Support the Lifecycle of Cy-
ber–Physical Production Systems. Proceedings of
IEEE, 109(4):568 – 581.
Hawkins, M. (2021). Cyber-Physical Production Networks,
Internet of Things-enabled Sustainability, and Smart
Factory Performance in Industry 4.0-based Manufac-
turing Systems. Economics, Management, and Finan-
cial Markets, 16(2):73 – 83.
Jiang, Z., Yuan, S., Ma, J., and Wang, Q. (2021). The
evolution of production scheduling from Industry 3.0
through Industry 4.0. International Journal of Pro-
duction Research.
Kayabay, K., G
¨
okalp, M. O., Eren, P. E., and Koc¸yi
˘
git, A.
(2018). [WiP] a workflow and cloud based service-
oriented architecture for distributed manufacturing in
industry 4.0 context. In 2018 IEEE 11th Confer-
ence on Service-Oriented Computing and Applica-
tions (SOCA), pages 88–92. IEEE.
Lee, J., Bagheri, B., and Kao, H.-A. (2015). A cyber-
physical systems architecture for industry 4.0-based
manufacturing systems. Manufacturing letters, 3:18–
23.
Liu, B., Glock, T., Betancourt, V. P., Kern, M., Sax, E., and
Becker, J. (2020). Model driven development process
for a service-oriented industry 4.0 system. In 2020
9th International Conference on Industrial Technol-
ogy and Management (ICITM), pages 78–83. IEEE.
Margaria, T. and Schieweck, A. (2019). The Digital Thread
in Industry 4.0. In Proceedings of Int. Conference on
Integrated Formal Methods (IFM), pages 3–24.
Matsunaga, F., Zytkowski, V., Valle, P., and Deschamps,
F. (2022). Optimization of energy efficiency in
smart manufacturing through the application of cyber-
physical systems and industry 4.0 technologies. Jour-
nal of Energy Resources Technology, pages 1 – 8.
Mohammed, I. K. and Trzcielinski, S. (2021). The Intercon-
nections Between ICT, Industry 4.0 and Agile Manu-
facturing. Management and Production Engineering
Review, 12(4).
Nica, E. and Stehel, V. (2021). Internet of Things Sens-
ing Networks, Artificial Intelligence-based Decision-
Making Algorithms, and Real-Time Process Monitor-
ing in Sustainable Industry 4.0. International Journal
of Production Research, 3:35–47.
Nordal, H. and E-Thalji, I. (2020). Modeling a predictive
maintenance management architecture to meet indus-
try 4.0 requirements: A case study. Systems Engineer-
ing, 24(1):34–50.
Park, K., Lee, J., Kim, H., and Noh, S. (2020). Digital
twin-based cyber physical production system architec-
tural framework for personalized production. Interna-
tional Journal of Advanced Manufacturing Technol-
ogy, 106:1787–1810.
Park, K. T., Im, S. J., Kang, Y.-S., Noh, S. D., Kang, Y. T.,
and Yang, S. G. (2019). Service-oriented platform for
smart operation of dyeing and finishing industry. In-
ternational Journal of Computer Integrated Manufac-
turing, 32(3):307–326.
Qi, L., Yang, Y., Zhou, X., Rafique, W., and Ma, J. (2021).
Fast anomaly identification based on multi-aspect data
streams for intelligent intrusion detection toward se-
cure industry 4.0. IEEE Transactions on Industrial
Informatics, pages 1–1.
Siqueira, F. and Davis, J. G. (2021). Service Comput-
ing for Industry 4.0: State of the Art, Challenges,
and Research Opportunities. ACM Computing Survey,
54(9):188:1 – 188:38.
Tao, F., Zhang, H., Liu, A., and Nee, A. Y. (2018). Digital
twin in industry: State-of-the-art. IEEE Transactions
on Industrial Informatics, 15(4):2405–2415.
Zhang, H., Yan, Q., and Wen, Z. (2020). Information
modeling for cyber-physical production system based
on digital twin and automationml. The interna-
tional journal of advanced manufacturing technology,
107(3):1927–1945.
A Distributed Registry of Multi-perspective Data Services in Cyber Physical Production Networks
181