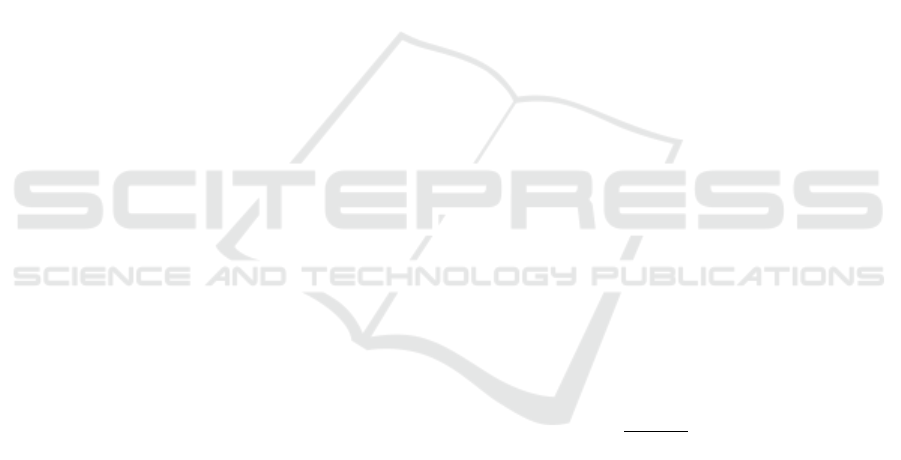
to melt. The melted content is tapped to a container
called ladle which determines the size or weight of
the main unit called heat and can be seen as the prod-
uct. The secondary metallurgy starts in the ladle and
involves a set of processes which aim at giving the
heat a specific, desired chemical composition, defined
as steel grade. After the desired composition is ob-
tained, the steel will be solidified in a continuous cast-
ing machine to the required semiproduct size, the so-
called format. The formats of long products can be
divided into billets and blooms, billets are smaller and
blooms are bigger; steel flat semiproducts use differ-
ent names. The important fact about the casting ma-
chine is that it is best suited for continuous operation.
Starting and ending a heat cast requires some time and
resources for preparation. Therefore heats with equal
formats and similar steel grades are grouped into so
called sequences. The heats of one such group are cast
one after another in the casting machine. If the casted
heats are not of the same grade, this results in mixed
steel in between two heats and the mixed steel in this
part of the cast has to be scrapped. The amount of
scrapped material depends on the difference in com-
position of the two heats and can at least aproximately
be calculated. This scrap costs are the basis of the ob-
ject function that is to be minimized in the planning
system. Intuitively, one would group as many heats
as possible of the same steel grade into a long se-
quence, but that approach would most often not fulfill
the commercial demand of the steel producer. Fur-
thermore, it is not possible to group an arbitrary num-
ber of heats in a sequence and the sequences can not
be ordered completely arbitrarily, due to metallurgical
rules and safety measures given by the plant. These
form the constraints of the optimization problem, that
should be satisfied if possible.
3 PRELIMINARIES
In this section, we formally define the structure of
the travelling salesman problem (TSP) that is used to
model the problem at hand and roughly describe the
simulated annealing algorithm as a solution method
for the TSP.
Travelling Salesman Problem: Let V = {1, . . . , n}
a set of vertices. The Travelling Salesman Problem
(TSP) can be seen as an undirected graph G = (V, E)
or directed graph G = (V, A) where E = {(i, j) : i, j ∈
V, i < j} is a set of edges or A = {(i, j) : i, j ∈ V, i 6= j}
a set of arcs. The graphs are 2-regular and path-
connected. A distance matrix D = (d
i j
) ∈ R
n×n
is
defined on E or on A where d
i, j
is the travelling
distance between the vertices i, j ∈ V (Matai et al.,
2010). In our case we consider the asymmetric TSP.
A very typical formulation is a linear integer program-
ming formulation (LP) (Liu et al., 2008; Matai et al.,
2010). Because of complexity of some real world
problems, it can be very difficult to formulate their
extra constraints as LP’s. Therefore a metaheuristic
approach can be more suitable alternative (Pasotti and
Zavanella, 2007). A route can be described as permu-
tation of V (Johnson and McGeoch, 1997):
π = (π(1), π(2), . . . , π(n)) (1)
In most definitions the route has to be closed, but in
our case we leave out the last edge between the start
and end point. The objective of the TSP is to mini-
mize the total distance
min
π
f (π) (2)
with
f (π) =
n−1
∑
i=1
d
π(i),π(i+1)
. (3)
A typical solution method for this problem is the
simulated annealing algorithm.
Simulated Annealing is a tour improvement method.
After an initial generated route x, the algorithm tries
to improve the quality of the route by generating a
new route y with small changes like swap, inverse
or insert operations (Zhan et al., 2016). Here, we
call them shuffle functions. Key of the simulated
annealing is that in principle moves can be accepted
that make the route worse. The probability of accept-
ing worse solutions decreases over the time and is
depicted by the decreasing temperature parameter T
and the acceptance function:
p(T ) =
(
1 , if f (y) ≤ f (x)
exp(
f (x)− f (y)
T
) , else
(4)
That can help to avoid local minima. A pseudo code
desciption of the SA algorithm can be seen in table 1.
4 MODELING OF THE PROBLEM
As explained in the previous section, the TSP is a
combinatorial graph problem. The cities are the nodes
and the connections with distances are the edges.
Given a list of n cities, the TSP is to find the short-
est route visiting each city just once.
4.1 Use Case TSP Connection
In the case of steel production, the input of the algo-
rithm is a given order list with n heats that have be
ETCIIM 2022 - International Workshop on Emerging Trends and Case-Studies in Industry 4.0 and Intelligent Manufacturing
292