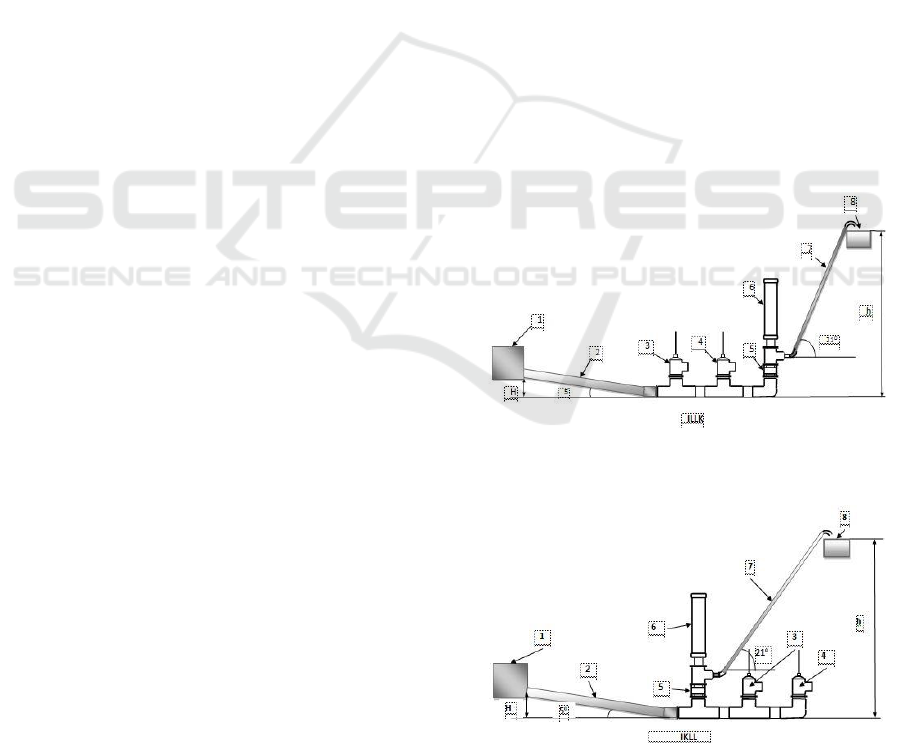
Various studies have been carried out in an effort
to improve the efficiency of the hydraulic ram pump
performance, such as (Asep Supriyanto et al., 2017)
conducted a study entitled “Pengaruh Variasi Jarak
Sumbuh Katub Limbah dengan Sumbuh Tabung
Udara Terhadap Efisiensi Pompa Hidram”, in which
the results showed that the variation of the shortest
distance (0.25 m) get an output discharge of 0.0041
m³/second with an efficiency of 14%.
(Aris Eko Sulistiawan, et al., 2006), also
conducted a study entitled “Pengaruh Berat Katub
Limbah dan Ketinggian Discharge Terhadap Kerja
Pompa Hidram”. The results showed that, the best
capacity at the west of the waste valve is 200 grams
with a value of 7.75 liters/minute at 3 meters
discharge, volumetric efficiency is 52.961% and
pump efficiency is 60.623%.
Another study conducted by (Muhamad Jafri et
al., 2017), entitled “Analisa Beda Tinggi Katub
Limbah dan Variasi Diameter Pipa Inlet Terhadap
Unjuk Kerja Pompa Hidram Ukuran Dua Inchi”.
The results showed that the minimum efficiency of
59.15% was obtained at a valve height difference of
15 cm and an inlet pipe diameter of 3 inches, while
the highest efficiency was obtained at 95.29% at a
different valve height of 10 cm and an inlet pipe
diameter of 2 inches.
(Muhamad Fajri et al., 2015), also conducted a
study entitled “Pengaruh Diameter Katub Limbah
dan Jarak Antara Katub Limbah dengan Katub
Penghantar Terhadap Efisiensi Pompa Hidram. The
results showed that the highest efficiency obtained
was 79.7535% at a waste valve diameter of 0.041
meters and a distance between valves of 0.130
meters.
From previous studies, no researcher has raised
the issue of the number of waste valves used in
increasing the efficiency of hydraulic ram pump
performance.
The purpose of this study was to design and
manufacture a hydraulic ram pump and to test the
use of a double valve in series arrangement in three
positions: Input-Waste-Waste-Compressor (IWWC),
Input-Compressor-Waste-Waste (ICWW) and Input-
Waste-Compressor-Waste (IWCW).
The main issue that will be raised in this research
is the use of new and renewable energy in meeting
the needs of clean water for rural communities,
especially those that have not been reached by the
State Electricity Company.
The results of this study are expected to solve the
problems mentioned above, so that people can take
advantage of the natural resources that are around
them (river water), for their daily needs such as
drinking water, watering plants and giving water to
their livestock. Thus the standard of living of the
people will be better.
2 RESEARCH METHOD
2.1 Design and Manufacture of 2 Inch
Ram Hydraulic Pump with Double
Drain Valve Series Arrangement
The hydraulic ram pump is designed with an input
pipe diameter of 2” or 5.075 cm, an output pipe
diameter of 1.27 cm, a compressor tube volume of
3000 ml, with variations in the arrangement of
ICWW, IWWC and IWCW. The inclination angle of
the inlet pipe is 5
0
, water drop height is 1.5 meters,
and water lift height is 5 meters. The hydraulic ram
pump is made using iron pipe (T shock) ø 2 inch,
double nipple 2 inch, elbow 2 inch, elbow inch, steel
pipe ø 2½ inch, elbow iron 70x70x6000 mm, solid
stainless ø 10 mm, steel axle ø 40 mm , paralon pipe
ø 2 inch and ½ inch, 5 mm thick rubber, bolts and
nuts. The results of the design of the hydraulic ram
pump as shown in Figures 1, 2 and 3 below:
Figure 1: Installation of Hydraulic Ram Pump in IWWC
Arrangement.
Figure 2: Installation of Hydraulic Ram Pump in ICWW
Arrangement.
Analysis of the Effect of Double Waste Valves in Series Arrangement and Compressor Tube Layout on the Performance Efficiency of 2 Inch
Hydraulic Ram Pump
159