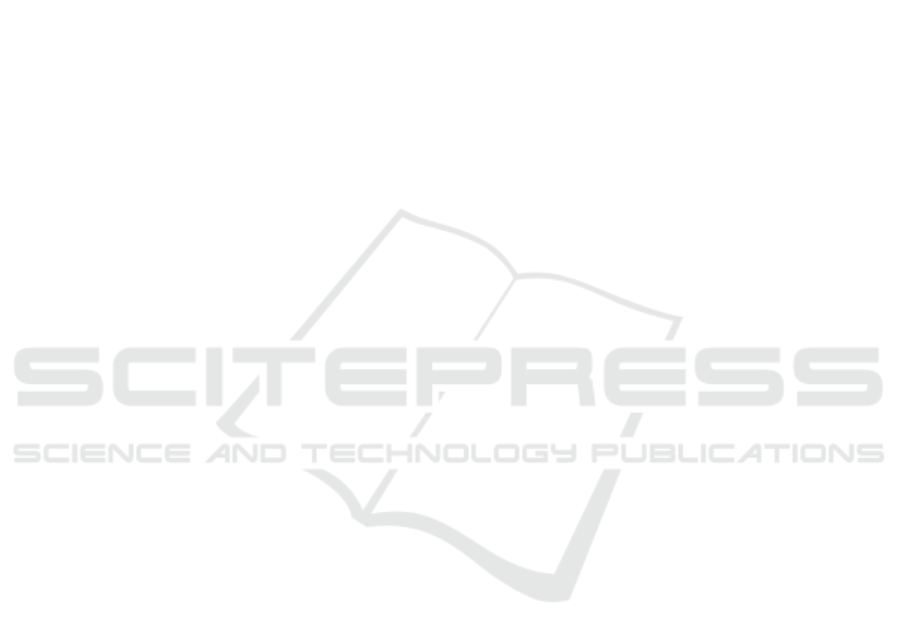
Implementation of Particle Swarm Optimization (PSO) Method in
Minimum Quantity Lubrication (MQL) Optimization to Obtain
Optimal Machining in CNC Milling Machine
Yogi Muldani Hendrawan, Faza Husnan Anshori, Andri Pratama, Herman Budi Harja, Pandoe
and Akil Priyamanggala Danadibrata
Department of Manufacturing Engineering, Manufacturing Polytechnic Bandung, Jalan Kanayakan No. 21, Dago,
Coblong, Bandung, 40135, Indonesia
herman@polman-bandung.ac.id, pandoe@polman-bandung.ac.id, akil_pd@polman-bandung.ac.id
Keywords: Minimum Quantity Lubricant, Particle Swarm Optimization, CNC Milling Machine, ISO 14001, Regression.
Abstract: One of the machining processes used is the milling process with CNC milling machines equipped with cutting
fluid to reduce the impact of the cutting process. One of the techniques of cutting fluid is to use MQL
(Minimum Quantity Lubricant) as an application of ISO 140001 in reducing coolant waste in the environment
which has the advantage of being more economical in reducing friction between the tool and the workpiece,
thereby reducing the temperature rate in the cutting tool. The CNC tool machine of Politeknik Manufaktur
Bandung is equipped with MQL (Minimum Quantity Lubricant) with Arduino control which has no
parameters for optimum coolant discharge during the machining process.
In this study, the Particle Swarm Optimization (PSO) method was used, which is one of the optimization
methods for making decisions used in the manufacturing process by looking for a minimum value. There
sulting from the milling process becomes a response in the process on CNC milling machines to obtain the
characteristics of an effective discharged lubricant discharge. Some parameters such as cutting depth and
feeding speed for aluminum and steel materials St37 were identified as experimental data for response. The
data was searched for equations with regression, so in this study a polynomial regression model was chosen
that could describe the data value better than linear regression.
Polynomial equations are calculated with the Particle Swarm Optimization (PSO) algorithm to find the
optimum flowrate. So that the minimum discharge obtained on aluminum material for a feeding depth of less
than 0.85 mm is 25ml/h, and more than 0.85mm is 85ml/h. while for St.37 material the feeding depth of less
than 0.35 mm is 25ml/h, and more than 0.35mm is 85ml/h.
1 INTRODUCTION
One of the machine tools that uses automation
systems that are commonly used by industry today is
CNC (Computer Numerical Control) machines. In the
machining process, it cannot be separated from the
use of coolant or coolant to clean and cool the
workpiece and cutting tools. Related to
environmental issues regulated in ISO 140001 on
recommendations for reducing coolant waste in the
machining process. Therefore, a method is needed by
using a coolant that is as minimal as possible with
more environmentally friendly materials. One of the
methods used is minimum quantity lubricant (MQL).
Related to environmental issues regulated in ISO
140001 on recommendations for reducing coolant
waste in the machining process. Therefore, a method
is needed by using a coolant that is as minimal as
possible with more environmentally friendly
materials. One of the methods used is minimum
quantity lubricant (MQL).
Be advised The development of POLMAN CNC
machine tools already has a cooling system by
installing a minimum quantity lubricant (MQL)
method cooling system with Arduino control on a
MINI CNC Milling machine made by POLMAN.
However, the Minimum Quantity Lubricant (MQL)
does not yet have an optimum discharge. The Particle
Swarm Optimization (PSO) method is used as one of
the optimization algorithms that can solve complex
optimization problems if solved in an exact manner.
Hendrawan, Y., Anshori, F., Pratama, A., Harja, H., Pandoe, . and Danadibrata, A.
Implementation of Particle Swarm Optimization (PSO) Method in Minimum Quantity Lubrication (MQL) Optimization to Obtain Optimal Machining in CNC Milling Machine.
DOI: 10.5220/0011891500003575
In Proceedings of the 5th International Conference on Applied Science and Technology on Engineering Science (iCAST-ES 2022), pages 821-827
ISBN: 978-989-758-619-4; ISSN: 2975-8246
Copyright © 2023 by SCITEPRESS – Science and Technology Publications, Lda. Under CC license (CC BY-NC-ND 4.0)
821