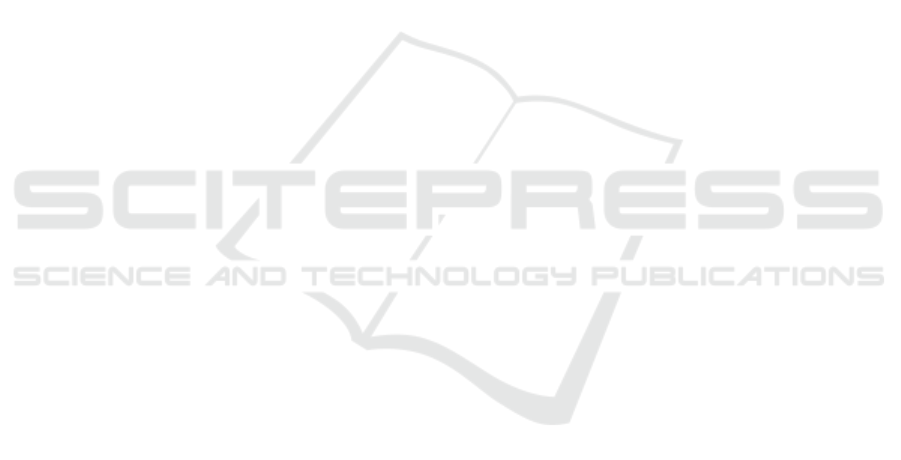
automation industry worldwide, is proven. Due to
their widespread use and the diversity of models and
systems, it is necessary to carry out this type of
research to create solid bases for the progressive
development of assisted manufacturing.
ACKNOWLEDGEMENTS
This work is supported by the research
management of the Universidad Autónoma de
Bucaramanga, where the research project has a grant
to supports Bachelor´s students in mechatronics
engineering.
REFERENCES
Abhishek, K., & Kumar Dalla, V. (2022). Formulation of
kinematics and gait locomotion for Hyper-
Redundant robot. Materials Today: Proceedings, 56,
976–979.
https://doi.org/10.1016/j.matpr.2022.03.110
Fortunato, G. M., Bonatti, A. F., Batoni, E., Macaluso, R.,
Vozzi, G., & De Maria, C. (2022). Motion
compensation system for robotic based in situ
bioprinting to balance patient physiological
movements. Bioprinting, 28(October), e00248.
https://doi.org/10.1016/j.bprint.2022.e00248
Kayastha, S., Katupitiya, J., Pearce, G., & Rao, A. (2022).
Comparative study of post-impact motion control of
a flexible arm space robot. European Journal of
Control, xxxx, 100738.
https://doi.org/10.1016/j.ejcon.2022.100738
Kouritem, S. A., Abouheaf, M. I., Nahas, N., & Hassan, M.
(2022). A multi-objective optimization design of
industrial robot arms. Alexandria Engineering
Journal, 61(12), 12847–12867.
https://doi.org/10.1016/j.aej.2022.06.052
Mendoza-Calderón, K. D., Jaimes, J. A. M., Maradey-
Lazaro, J. G., Rincón-Quintero, A. D., & Cardenas-
Arias, C. G. (2022). Design of an Automatic
Palletizer. Journal of Physics: Conference Series,
2224(1), 0–15. https://doi.org/10.1088/1742-
6596/2224/1/012095
Misra, A., Sharma, A., Singh, G., Kumar, A., & Rastogi, V.
(2020). Design and Development ofa Low-Cost
CNC Alternative SCARA Robotic Arm. Procedia
Computer Science, 171(2019), 2459–2468.
https://doi.org/10.1016/j.procs.2020.04.266
Narayan, J., Mishra, S., Jaiswal, G., & Dwivedy, S. K.
(2020). Novel design and kinematic analysis of a 5-
DOFs robotic arm with three-fingered gripper for
physical therapy. Materials Today: Proceedings, 28,
2121–2132.
https://doi.org/10.1016/j.matpr.2020.04.017
Ni, S., Chen, W., Ju, H., & Chen, T. (2022). Coordinated
trajectory planning of a dual-arm space robot with
multiple avoidance constraints. Acta Astronautica,
195(December 2021), 379–391.
https://doi.org/10.1016/j.actaastro.2022.03.024
Rahul, K., Raheman, H., & Paradkar, V. (2019). Design and
development of a 5R 2DOF parallel robot arm for
handling paper pot seedlings in a vegetable
transplanter. Computers and Electronics in
Agriculture, 166(February), 105014.
https://doi.org/10.1016/j.compag.2019.105014
Rincon-Quintero, A. D., Del Portillo-Valdés, L. A.,
Meneses-Jácome, A., Ascanio-Villabona, J. G.,
Tarazona-Romero, B. E., & Durán-Sarmiento, M. A.
(2021). Performance Evaluation and Effectiveness
of a Solar-Biomass Hybrid Dryer for Drying
Homogeneous of Cocoa Beans Using LabView
Software and Arduino Hardware BT - Recent
Advances in Electrical Engineering, Electronics and
Energy (M. Botto Tobar, H. Cruz, & A. Díaz Cadena
(eds.); pp. 238–252). Springer International
Publishing.
Rincon-Quintero, A. D., Del Portillo-Valdés, L. A.,
Meneses-Jácome, A., Sandoval-Rodríguez, C. L.,
Rondón-Romero, W. L., & Ascanio-Villabona, J. G.
(2021). Trends in Technological Advances in Food
Dehydration, Identifying the Potential Extrapolated
to Cocoa Drying: A Bibliometric Study BT - Recent
Advances in Electrical Engineering, Electronics and
Energy (M. Botto Tobar, H. Cruz, & A. Díaz Cadena
(eds.); pp. 167–180). Springer International
Publishing.
Rincon-Quintero, A. D., Del Portillo-Valdés, L. A.,
Zanabria-Ortigoza, N. D., Sandoval-Rodriguez, C.
L., Maradey-Lázaro, J. G., & Castillo-León, N. Y.
(2022). Exergy analysis and development of flat
plate solar collectors: A Review. IOP Conference
Series: Materials Science and Engineering, 1253(1),
012009. https://doi.org/10.1088/1757-
899x/1253/1/012009
Rincon-Quintero, A. D., Portillo-Valdés, L. A. Del,
Cárdenas-Arias, C. G., Tarazona-Romero, B. E.,
Rondón-Romero, W. L., & Durán-Sarmiento, M. A.
(2021). A bibliometric analysis of the uses of the
cocoa pod shell. IOP Conference Series: Materials
Science and Engineering, 1154(1), 012032.
https://doi.org/10.1088/1757-899x/1154/1/012032
Rincon-Quintero, A. D., Sandoval-Rodríguez, C. L.,
Lengerke-Perez, O., Rueda-Osma, M. F., & Mateus-
Ariza, J. A. (2022). Evaluation and Control of
Psychrometric Variables Present in an Automated
Greenhouse for the Production of Organic Tomato
BT - Recent Advances in Electrical Engineering,
Electronics and Energy (M. Botto-Tobar, H. Cruz, &
A. Díaz Cadena (eds.); pp. 165–180). Springer
International Publishing.
Rybus, T., Wojtunik, M., & Basmadji, F. L. (2022).
Optimal collision-free path planning of a free-
floating space robot using spline-based trajectories.
Acta Astronautica, 190(June 2021), 395–408.
https://doi.org/10.1016/j.actaastro.2021.10.012
Sanchez, M., Cruz-Ortiz, D., Ballesteros, M., Salgado, I., &
ISAIC 2022 - International Symposium on Automation, Information and Computing
502