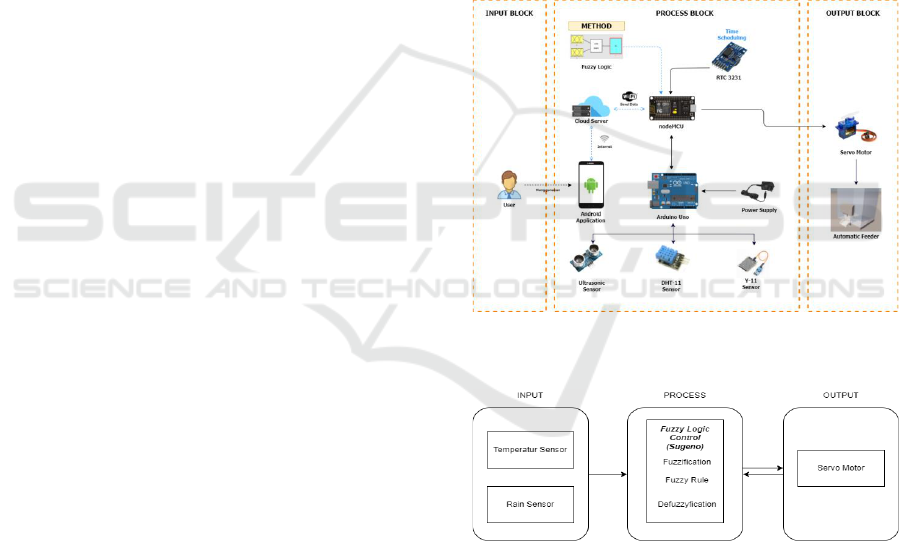
environmental sensors collects data on water
conditions (aquatic), and sends it to a data centre for
further data storage and processing (Sousa, 2019).
Sun et al. proposed an integrated water quality
monitoring system with GIS and IoT technology. The
system performs remote monitoring, management
and control of water temperature, dissolved oxygen,
pH, and water level. The system performs packet loss
rate analysis using a Wi-Fi network and analyses
dissolved oxygen conditions (Sun, 2019).
Lee et al. proposed an IoT-based urban aquaponic
system. The system consists of a fish tank,
hydroponic tank, IoT monitor (pH), and a water test
kit (pH, NO2, NO3). Case study using hydroponics
plant lettuces and breed goldfish (Lee, 2019). Ismail
et al. proposed a model for direct measurement and
IoT-based fishpond water parameter monitoring
system. The system consists of a Raspberry Pi
microcontroller, DO sensor, temperature sensor, pH
sensor. Data from the sensor is sent to the
microcontroller, and then sent to the database server
(Ismail, 2020).
Uddin et al. proposed a real-time freshwater
shrimp monitoring system. The system detects the
sensor values for temperature, pH, dissolved oxygen,
salinity level, and turbidity. The system will give an
alert if it is out of the range value that has been set.
The system analyses the size, weight, and percentage
of live shrimp (Uddin, 2020). Ouyang et al. proposed
a monitoring framework for aquaculture farms. The
framework consists of a robotic sensing platform
equipped with water quality sensors, an automatic
charging system and sensor cleaning, a data
processing system using machine learning, and an
aquaculture farm control centre (Ouyang, 2021).
2 SYSTEM DESIGN
Figure 1 shows an overview of the proposed system
design. In the design of this system, the data to be
processed will be obtained directly from the data on
the feed container in the fish pond. Where there are
three parts contained in the design of this system,
namely, block input, process, and output.
In the input block section there are users who can
monitor the status of feed conditions and feeding
schedules in real time with the Android application.
And also, users can receive notifications of feeding
schedules.
In the process block, there is an Arduino Uno as
the sensor control centre. The sensor used is an
ultrasonic sensor, which functions to measure the
availability of feed. The DHT sensor and Rain
detector for monitoring weather conditions as an
output of the amount of feed measured using the
fuzzy method. NodeMCU will receive the data value
sent from Arudino Uno. The data values are sent by
nodeMCU to Firebase.
At the output, nodeMCU gives commands to the
servo motor to move the feed container valve to open
it according to the specified time and the amount of
feed depends on the fuzzy calculation.
After the data is processed, the data will be sent
and stored on the Firebase real-time database server.
The android application will display the data in the
database in real-time to the application user via
internet communication. The main features of the
Android application as data visualization are
monitoring feeder, control schedule, and monitoring
weather.
Figure 1: Design of an automatic feeder system in a koi
fishpond.
Figure 2: Design of an automatic feeder system in a koi
fishpond.
Fuzzy logic control is applied to the servo motor.
The function of this control is to control the length of
time the servo motor opens the valve. The input of the
fuzzy logic control system is data from temperature
and humidity sensors and rain sensors. Both sensors
are used to determine the outdoor weather conditions
in the koi fish pond. The final desired result from this
fuzzy logic control application is that fish feed can be
distributed on a scheduled basis and according to the
iCAST-ES 2022 - International Conference on Applied Science and Technology on Engineering Science
922