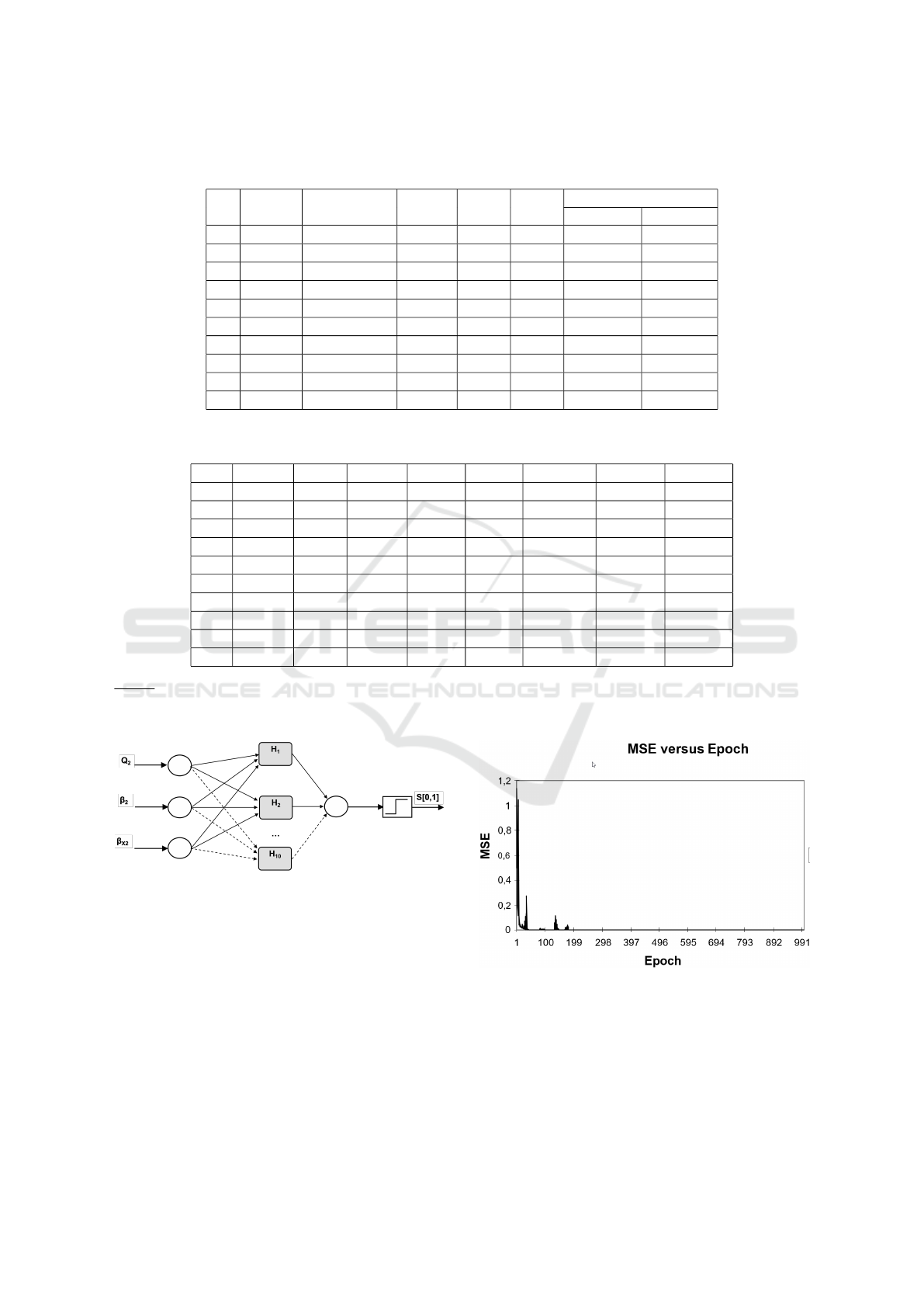
Table 3: A fragment of a cluster with elements that best correspond to the current technological situation in the vector of
output.
№ Q
2
,t/h βnn
2
(β
2
),% βx
2
,% γ
2
,% ε
2
,%
Limitation [min-max]
β
2
,% βx
2
,%
1 305,81 52,30 10,66 65,93 82,90 50,3-53,3 9,8-11,1
2 324,93 50,86 10,04 65,69 81,32 50,3-53,3 9,8-11,1
3 316,70 51,48 10,31 65,79 82,00 50,3-53,3 9,8-11,1
4* 328,69 50,61 9,93 65,65 81,04 50,3-53,3 9,8-11,1
5 303,31 52,87 10,91 66,02 83,53 50,3-53,3 9,8-11,1
6 312,47 51,91 10,50 65,86 82,48 50,3-53,3 9,8-11,1
7 311,58 51,98 10,53 65,88 82,55 50,3-53,3 9,8-11,1
8 297,56 52,91 10,93 66,03 83,58 50,3-53,3 9,8-11,1
9 324,34 51,29 10,23 65,76 81,79 50,3-53,3 9,8-11,1
10 294,15 53,20 11,05 66,08 83,89 50,3-53,3 9,8-11,1
Table 4: A fragment of a cluster with the corresponding elements according to the vector of control influences and mode
indicators.
№ C
2
,% d
2
,% Ph
2
,% ρ
k2
,% ρ
c2
,% Bm
2
,t/h Bk
2
,t/h Bc
2
,t/h
1 326,75 78,07 78,00 19,33 22,60 27,33 106,67 96,67
2 278,90 75,58 76,56 16,94 19,87 26,37 101,89 91,89
3 299,53 76,65 77,18 17,97 21,05 26,79 103,95 93,95
4** 270,38 75,13 76,31 16,51 19,39 26,20 101,03 91,03
5 345,86 79,06 78,57 20,29 23,69 27,71 108,58 98,58
6 313,97 77,40 77,61 18,69 21,87 27,07 105,39 95,39
7 316,19 77,52 77,68 18,80 22,00 27,12 105,61 95,61
8 347,32 79,14 78,61 20,36 23,77 27,74 108,73 98,73
9 293,27 76,33 76,99 17,66 20,69 26,66 103,32 93,32
10 356,73 79,63 78,90 20,83 24,31 27,93 109,67 99,67
Notes: where (*) is the class closest to the ideal on the basis of the analysis of values of initial (qualitative)
indicators; (**) is the corresponding vector of setting values (control effects and mode indicators) to ensure
quasi-optimal (close to ideal) output.
Figure 2: Neural network implementation scheme (3: 10:
1) for classification procedure.
choose the appropriate values of tolerance fields. This
can be done by varying the value of the tolerance and
its further study (figure 5).
As can be seen from figure 5 the number of classes
that are recognized linearly depends on the tolerance
values. This is evidenced by the linear trend, which is
determined on the basis of the known method of least
squares. The value of the coefficient of determination
R
2
= 99.8% indicates a sufficiently high reliability of
the approximation.
Analysis of the results of intellectual classification
Figure 3: Report on the course of parameterization of the
classification process.
(figures 3, 4, 5) and table 5 indicates the sufficient
quality of such a procedure. Thus, when changing the
normalized average tolerance fields within 4-4.5%, it
is possible to determine with sufficient adequacy from
1 to 13 vectors with potentially quasi-optimal settings
CSSE@SW 2022 - 5th Workshop for Young Scientists in Computer Science Software Engineering
10