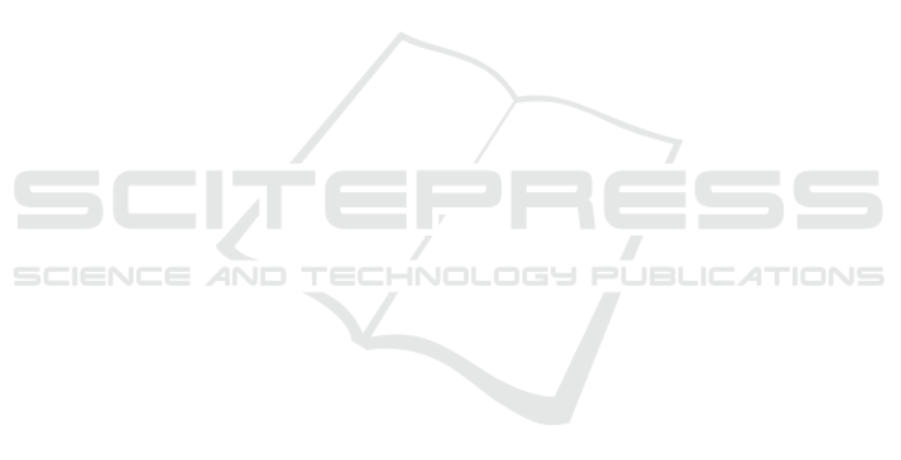
REFERENCES
3D Systems, I. (2022). Specifications — 3D Sys-
tems. http://3dsystems.com/haptics-devices/touch-x/
specifications. [Online; accessed 10-June-2022].
Abdul Aziz, F. and Mousavi, M. (2009). A review of haptic
feedback in virtual reality for manufacturing industry.
Journal of Mechanical Engineering, 40:68.
Alabdulmuhsin, A. (2015). A force feedback haptic in-
terface for atomic force microscopy. Master’s thesis,
Missouri University of Science and Technology.
Albrecht, T. R., Gr
¨
utter, P., Horne, D., and Rugar, D.
(1991). Frequency modulation detection using high-q
cantilevers for enhanced force microscope sensitivity.
Journal of Applied Physics, 69(2):668–673.
Bian, K., Gerber, C., Heinrich, A. J., M
¨
uller, D. J., Scheur-
ing, S., and Jiang, Y. (2021). Scanning probe mi-
croscopy. Nature Reviews Methods Primers, 1.
Binnig, G., Quate, C. F., and Gerber, C. (1986). Atomic
force microscope. Phys. Rev. Lett., 56:930–933.
Binnig, G., Rohrer, H., Gerber, C., and Weibel, E. (1982).
Surface studies by scanning tunneling microscopy.
Phys. Rev. Lett., 49:57–61.
Burdea, G. (1999). Haptic feedback for virtual reality. Pro-
ceedings of International Workshop on Virtual Proto-
typing, pages 17–29.
Drebin, R. A., Carpenter, L., and Hanrahan, P. (1988).
Volume rendering. SIGGRAPH Comput. Graph.,
22(4):65–74.
Galin, E., Gu
´
erin, E., Paris, A., and Peytavie, A. (2020).
Segment Tracing Using Local Lipschitz Bounds.
Computer Graphics Forum.
Giessibl, F. J., Hembacher, S., Bielefeldt, H., and Mannhart,
J. (2000). Subatomic features on the silicon (111)-
(7×7) surface observed by atomic force mi-
croscopy. Science, 289(5478):422–425.
Gross, L., Schuler, B., Pavli
ˇ
cek, N., Fatayer, S., Ma-
jzik, Z., Moll, N., Pe
˜
na, D., and Meyer, G. (2018).
Atomic force microscopy for molecular structure elu-
cidation. Angewandte Chemie International Edition,
57(15):3888–3908.
Hart, J. (1995). Sphere tracing: A geometric method for the
antialiased ray tracing of implicit surfaces. The Visual
Computer, 12.
Heile, D., Olbrich, R., Reichling, M., and Rahe, P.
(2021). Alignment method for the accurate and pre-
cise quantification of tip-surface forces. Phys. Rev. B,
103:075409.
Huang, F., Gillespie, B., and Kuo, A. (2007). Visual and
haptic feedback contribute to tuning and online con-
trol during object manipulation. Journal of motor be-
havior, 39:179–93.
Karhu, K. (2002). Displacement mapping. In: Helsinki
University of Techonology, Tik-111.500 Seminar on
computer graphics.
Ladjal, H., Hanus, J.-L., Pillarisetti, A., Keefer, C., Fer-
reira, A., and Desai, J. (2009). Realistic visual and
haptic feedback simulator for real-time cell indenta-
tion. In IEEE/RSJ International Conference on Intel-
ligent Robots and Systems, pages 3993 – 3998, Taipei,
China.
Ljung, P., Kr
¨
uger, J., Groller, E., Hadwiger, M., Hansen,
C. D., and Ynnerman, A. (2016). State of the art in
transfer functions for direct volume rendering. Com-
put. Graph. Forum, 35(3):669–691.
Maclean, K. (2000). Designing with haptic feedback. Pro-
ceedings - IEEE International Conference on Robotics
and Automation, 1:783–788.
Massie, T. and Salisbury, J. (1994). The phantom haptic
interface: A device for probing virtual objects. Pro-
ceedings of the ASME Winter Annual Meeting, Sym-
posium on Haptic Interfaces for Virtual Environment
and Teleoperator Systems, pages 295–300.
Ne
ˇ
cas, D. and Klapetek, P. (2012). Gwyddion: an open-
source software for spm data analysis. Open Physics,
10(1):181–188.
Rubio-Sierra, F., Stark, R., Thalhammer, S., and Heckl, W.
(2003). Force-feedback joystick as a low-cost haptic
interface for an atomic-force-microscopy nanomanip-
ulator. Applied Physics A, 76.
Siu, A. F., Gonzalez, E. J., Yuan, S., Ginsberg, J., Zhao, A.,
and Follmer, S. (2017). Shapeshift: A mobile table-
top shape display for tangible and haptic interaction.
In Adjunct Publication of the 30th Annual ACM Sym-
posium on User Interface Software and Technology,
UIST ’17, page 77–79, New York, NY, USA. Associ-
ation for Computing Machinery.
Steed, A., Ofek, E., Sinclair, M., and Gonzalez Franco, M.
(2021). A mechatronic shape display based on auxetic
materials. Nature Communications, 12(4758 (2021)).
Stipe, B. C., Rezaei, M. A., and Ho, W. (1998). Single-
molecule vibrational spectroscopy and microscopy.
Science, 280(5370):1732–1735.
Taffanel, A., Rousselot, B., Danielsson, J., McGuire, K.,
Richardsson, K., Eliasson, M., Antonsson, T., and
H
¨
onig, W. (2021). Lighthouse positioning system:
Dataset, accuracy, and precision for UAV research.
CoRR, abs/2104.11523.
Weiss, J. and Navab, N. (2021). Deep direct volume ren-
dering: Learning visual feature mappings from exem-
plary images. CoRR, abs/2106.05429.
An Immersive Feedback Framework for Scanning Probe Microscopy
187