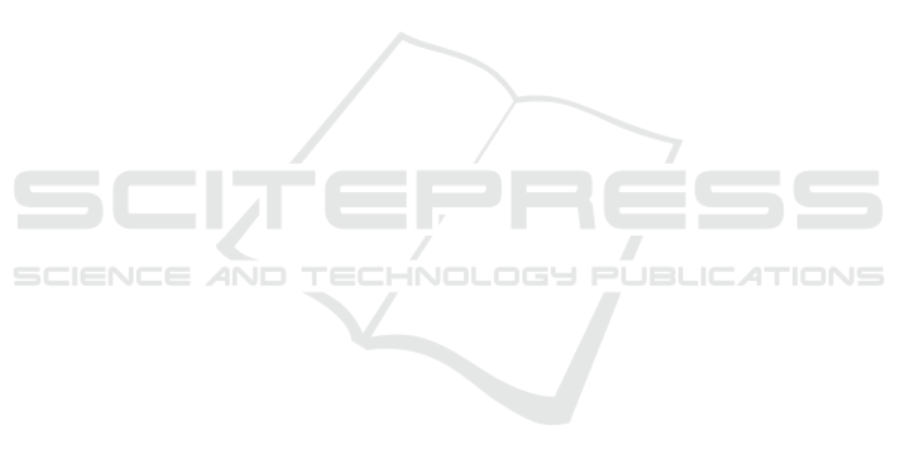
flows/pipelines can dynamically be adapted to current
situations, for example reacting to sensor drifts. This
enables heterogeneous collaboration and meets the re-
quirement of R5.
Evaluation of R6: Time Constraints. By opti-
mally utilizing the resources of the Raspberry Pi and
the MCC118 GPIO HAT, a maximum recording rate
of 80 kHz per worker, resulting in a 2 MB/sec network
load, could be achieved without causing queue jam-
ming. The CPU load of the local streaming system
node implemented with Redis was utilized by 3 work-
ers at an average of 60%, enabling fast processing of
events. A reaction to incoming events takes place im-
mediately after their occurrence. If more workers are
added in the future, Redis can be scaled both hori-
zontally and vertically to continue ensuring a fast re-
sponse time. The system met the time requirements in
the DQ-Meister project and thus fulfills requirement
R4.
6 CONCLUSION
In this work, a Data Acquisition System for dis-
tributed sensors was discussed with respect to pro-
totypical ML operations. This hierarchical system
consists of multiple embedded sensing devices, which
are synchronized. The system has been shown to be
easily extendable and it is not dependent on specific
technologies like OPC-UA. ARTHUR supports data
pre-processing close to the resource to reduce net-
work load and can additionally be tailored to spe-
cific data pre-processing use cases. The same goes
for specific data quality assessments where thresholds
for data values can be defined and acted upon on with
customized events. The proposed system was evalu-
ated with several Raspberry Pis and low cost sensors
making it affordable, even for early stages of proto-
typing. The provided interface enables a heteroge-
neous collaboration between domain experts and data
scientists. In order to uphold the time constraints of
different use cases, appropriate hardware can be used
without a problem as the architecture of the system is
hardware agnostic.
For the future, it is planned to integrate cam-
eras for visual surface quality inspection and integrate
ARTHUR into non-Raspberry Pi hardware. Addition-
ally we intend to add more complex hardware, like a
precision RTP oscilloscope with a max. sample rate
of 40 G sample/s in order to further test the limits of
the system. Furthermore a thorough security analy-
sis of the system has to be conducted in order to be
prepared for future Machine Learning audit require-
ments. Finally, the system will be evaluated with a
complex manufacturing use case.
ACKNOWLEDGMENT
This work as outcome of the project DQ-Meister*in
with the project number P2021-01-013 has received
funding from the Carl Zeiss Stiftung.
REFERENCES
Anik, S. M. H., Gao, X., Meng, N., Agee, P. R., and McCoy,
A. P. (2022). A cost-effective, scalable, and portable
iot data infrastructure for indoor environment sensing.
Journal of Building Engineering, 49:104027.
Asplund, F., Macedo, H. D., and Sassanelli, C. (2021).
Problematizing the service portfolio of digital innova-
tion hubs. In Camarinha-Matos, L. M., Boucher, X.,
and Afsarmanesh, H., editors, Smart and Sustainable
Collaborative Networks 4.0, pages 433–440, Cham.
Springer International Publishing.
Chu, Y. B. and Yap, W. K. (2021). Raspberry pi based
wireless interface system for automated microfabrica-
tion in the context of industry 4.0. In Zakaria, Z. and
Emamian, S. S., editors, Advances in Electrical and
Electronic Engineering and Computer Science, pages
117–123, Singapore. Springer Singapore.
Cioffi, R., Travaglioni, M., Piscitelli, G., Petrillo, A.,
and De Felice, F. (2020). Artificial intelligence and
machine learning applications in smart production:
Progress, trends, and directions. Sustainability, 12(2).
D., D. (2017). Industrial automation using iot with rasp-
berry pi. International Journal of Computer Applica-
tions, 168:44–48.
Ferencz, K. and Domokos, J. (2018). Iot sensor data ac-
quisition and storage system using raspberry pi and
apache cassandra. In 2018 International IEEE Confer-
ence and Workshop in
´
Obuda on Electrical and Power
Engineering (CANDO-EPE), pages 000143–000146.
Grimaldi, D. and Marinov, M. (2001). Distributed measure-
ment systems. Measurement, 30(4):279–287.
Hafeez, S. and Kathirisetty, N. (2022). Effects and compar-
ison of different data pre-processing techniques and
ml and deep learning models for sentiment analysis:
Svm, knn, pca with svm and cnn. In 2022 First Inter-
national Conference on Artificial Intelligence Trends
and Pattern Recognition (ICAITPR), pages 1–6.
Haizad, M., Ibrahim, R., Adnan, A., Chung, T. D., and Has-
san, S. M. (2016). Development of low-cost real-time
data acquisition system for process automation and
control. In 2016 2nd IEEE International Symposium
on Robotics and Manufacturing Automation (ROMA),
pages 1–5, Ipoh, Malaysia. IEEE.
IndustryARC (2021). Industrial raspberry pi market
2022 - 2027. IndustryARC, Report Code: AIR 0372.
CLOSER 2023 - 13th International Conference on Cloud Computing and Services Science
162