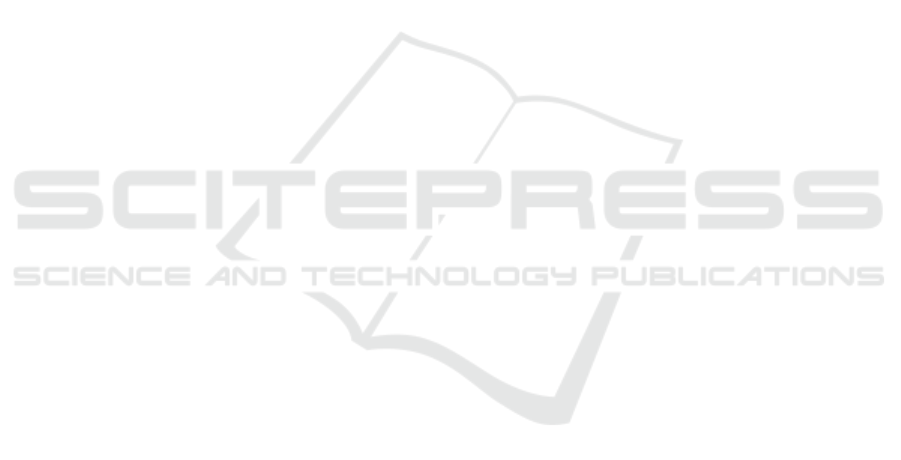
ing other objectives. To achieve this, a method dedi-
cated to solving multi-objective problems should be
applied in order to produce more useful results in
terms of the objectives that will be considered in fu-
ture work on this production environment. Another
perspective to consider is the improvement of our ap-
proach to be capable to solve scheduling problems
with transportation in a dynamic environment char-
acterized by other dynamic events such as machines
or robot breakdowns.
REFERENCES
Ali, K. B., Telmoudi, A. J., and Gattoufi, S. (2020).
Improved genetic algorithm approach based on new
virtual crossover operators for dynamic job shop
scheduling. IEEE Access, 8:213318–213329.
Brandimarte, P. (1993). Routing and scheduling in a flex-
ible job shop by tabu search. Annals of Operations
research, 41(3):157–183.
Chen, R., Yang, B., Li, S., and Wang, S. (2020). A self-
learning genetic algorithm based on reinforcement
learning for flexible job-shop scheduling problem.
Computers & Industrial Engineering, 149:106778.
Ding, H. and Gu, X. (2020). Improved particle swarm opti-
mization algorithm based novel encoding and decod-
ing schemes for flexible job shop scheduling problem.
Computers & Operations Research, 121:104951.
Fan, H., Xiong, H., and Goh, M. (2021). Ge-
netic programming-based hyper-heuristic approach
for solving dynamic job shop scheduling problem
with extended technical precedence constraints. Com-
puters & Operations Research, 134:105401.
Garey, M. R., Johnson, D. S., and Sethi, R. (1976).
The complexity of flowshop and jobshop scheduling.
Mathematics of operations research, 1(2):117–129.
Li, X., Peng, Z., Du, B., Guo, J., Xu, W., and Zhuang, K.
(2017). Hybrid artificial bee colony algorithm with
a rescheduling strategy for solving flexible job shop
scheduling problems. Computers & Industrial Engi-
neering, 113:10–26.
Long, X., Zhang, J., Zhou, K., and Jin, T. (2022). Dynamic
self-learning artificial bee colony optimization algo-
rithm for flexible job-shop scheduling problem with
job insertion. Processes, 10(3):571.
Martinsons, M. G. and Davison, R. M. (2007). Strategic de-
cision making and support. Decision support systems,
43(1):284–300.
Marzouki, B., Driss, O. B., and Gh
´
edira, K. (2017). Multi
agent model based on chemical reaction optimization
with greedy algorithm for flexible job shop scheduling
problem. Procedia Computer Science, 112:81–90.
Marzouki, B., Driss, O. B., and Gh
´
edira, K. (2018). Multi-
agent model based on combination of chemical reac-
tion optimisation metaheuristic with tabu search for
flexible job shop scheduling problem. International
Journal of Intelligent Engineering Informatics, 6(3-
4):242–265.
Mihoubi, B., Bouzouia, B., and Gaham, M. (2021). Reac-
tive scheduling approach for solving a realistic flexi-
ble job shop scheduling problem. International Jour-
nal of Production Research, 59(19):5790–5808.
Mohan, J., Lanka, K., and Rao, A. N. (2019). A review
of dynamic job shop scheduling techniques. Procedia
Manufacturing, 30:34–39.
Nouiri, M., Bekrar, A., Jemai, A., Niar, S., and Ammari,
A. C. (2018). An effective and distributed particle
swarm optimization algorithm for flexible job-shop
scheduling problem. Journal of Intelligent Manufac-
turing, 29(3):603–615.
Nouri, H. E., Belkahla Driss, O., and Gh
´
edira, K. (2018).
Solving the flexible job shop problem by hybrid
metaheuristics-based multiagent model. Journal of In-
dustrial Engineering International, 14(1):1–14.
Nouri, H. E., Driss, O. B., and Gh
´
edira, K. (2015). Genetic
algorithm combined with tabu search in a holonic
multiagent model for flexible job shop scheduling
problem. In ICEIS (1), pages 573–584.
Wiers, V. C. (1997). A review of the applicability of or
and ai scheduling techniques in practice. Omega,
25(2):145–153.
Xie, J., Gao, L., Peng, K., Li, X., and Li, H. (2019). Review
on flexible job shop scheduling. IET Collaborative
Intelligent Manufacturing, 1(3):67–77.
Zadeh, P. M., Fakoor, M., and Mohagheghi, M. (2018). Bi-
level optimization of laminated composite structures
using particle swarm optimization algorithm. Journal
of Mechanical Science and Technology, 32(4):1643–
1652.
Zhang, S. and Wong, T. N. (2017). Flexible job-shop
scheduling/rescheduling in dynamic environment: a
hybrid mas/aco approach. International Journal of
Production Research, 55(11):3173–3196.
A Bi-Level Genetic Algorithm to Solve the Dynamic Flexible Job Shop Scheduling Problem
759