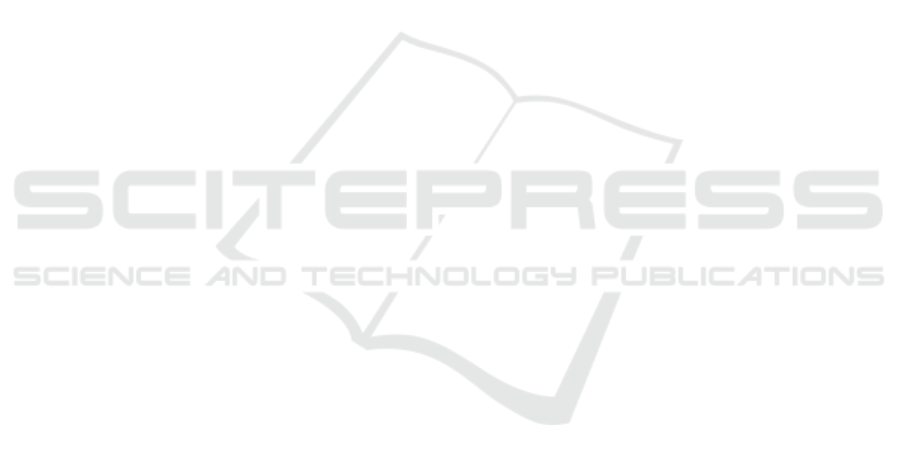
REFERENCES
Agarwal, S., Mierle, K., and Team, T. C. S. (2022). Ceres
Solver.
Alcantarilla, P. F., Nuevo, J., and Bartoli, A. (2013). Fast
explicit diffusion for accelerated features in nonlin-
ear scale spaces. In British Machine Vision Conf.
(BMVC).
Alzuhiri, M., Rathnakumar, R., Liu, Y., and Deng, Y.
(2021). CAAP: A Novel Structured Light Based Sens-
ing and Probabilistic Diagnostic Technique for Pipe
Internal Corrosion Detection and Localization. Tech-
nical report.
Bahnsen, C. H., Johansen, A. S., Philipsen, M. P., Hen-
riksen, J. W., Nasrollahi, K., and Moeslund, T. B.
(2021). 3D Sensors for Sewer Inspection: A Quanti-
tative Review and Analysis. Sensors (Basel, Switzer-
land), 21(7):2553.
Brown, D. C. (1966). Decentering distortion of lenses. Pho-
tometric Engineering, 32(3).
Dong, Y., Fang, C., Zhu, L., Yan, N., and Zhang, X. (2021).
The calibration method of the circle-structured light
measurement system for inner surfaces considering
systematic errors. Measurement Science and Technol-
ogy, 32(7):075012.
Esquivel, S., Koch, R., and Rehse, H. (2009). Pattern
Recognition, 31st DAGM Symposium, Jena, Ger-
many, September 9-11, 2009. Proceedings. In [”Den-
zler, {Notni, Joachim and}, {S
¨
uße, Gunther and}, and
Herbert”], editors, Pattern Recognition, volume 5748
of Lecture Notes in Computer Science, pages 332–
341. Springer Berlin Heidelberg. Series Title: Lecture
Notes in Computer Science.
Esquivel, S., Koch, R., and Rehse, H. (2010). Time budget
evaluation for image-based reconstruction of sewer
shafts. In Proceedings of SPIE, Real-Time Image and
Video Processing 2010, pages 77240M–77240M–12.
Furch, J. and Eisert, P. (2013). An Iterative Method for Im-
proving Feature Matches. In 2013 International Con-
ference on 3D Vision, 2013 International Conference
on 3D Vision, pages 406–413. IEEE.
Grisetti, G., K
¨
ummerle, R., Stachniss, C., and Burgard, W.
(2010). A Tutorial on Graph-Based SLAM. IEEE In-
telligent Transportation Systems Magazine, 2(4):31–
43.
Hansen, P., Alismail, H., Rander, P., and Browning, B.
(2015). Visual mapping for natural gas pipe inspec-
tion. The International Journal of Robotics Research,
34(4-5):532–558.
Hartley, R. and Zisserman, A. (2003). Multiple View Geom-
etry in Computer Vision. Cambridge University Press,
New York, NY, USA, 2nd edition.
Kannala, J., Brandt, S. S., and Heikkil
¨
a, J. (2008). Measur-
ing and modelling sewer pipes from video. Machine
Vision and Applications, 19(2):73–83.
K
¨
unzel, J., M
¨
oller, R., Waschnewski, J., Werner, T., Eis-
ert, P., and Hilpert, R. (2018). Automatic Analysis of
Sewer Pipes Based on Unrolled Monocular Fisheye
Images. 2018 IEEE Winter Conference on Applica-
tions of Computer Vision (WACV), pages 2019–2027.
Li, Y., Wang, H., Dang, L. M., Song, H.-K., and Moon, H.
(2022). Vision-Based Defect Inspection and Condi-
tion Assessment for Sewer Pipes: A Comprehensive
Survey. Sensors (Basel, Switzerland), 22(7):2722.
Morano, R. A., Ozturk, C., Conn, R., Dubin, S., Zietz, S.,
and Nissanov, J. (1998). Structured light using pseu-
dorandom codes. IEEE Transactions on Pattern Anal-
ysis and Machine Intelligence, 20(3):322–327.
Moreno, D. and Taubin, G. (2012). Simple, accurate, and
robust projector-camera calibration. Proceedings -
2nd Joint 3DIM/3DPVT Conference: 3D Imaging,
Modeling, Processing, Visualization and Transmis-
sion, 3DIMPVT 2012, pages 464–471.
Murli, A., D’Amore, L., and De Simone, V. (1999). The
wiener filter and regularization methods for image
restoration problems. In Proceedings 10th Interna-
tional Conference on Image Analysis and Processing,
pages 394–399.
Niblack, W. (1985). An Introduction to Digital Image Pro-
cessing. Strandberg Publishing Company, Topstykket
17, DK-3460 Birkeroed, Denmark.
Reiling, M. (2014). Implementation of a monocular struc-
tured light vision system for pipe inspection robot pi-
rate.
Vehar, D., Nestler, R., and Franke, K.-H. (2018). 3D-
EasyCalib – toolkit for the geometric calibration of
cameras and robots. In 22. Anwendungsbezogener
Workshop zur Erfassung, Modellierung, Verarbeitung
und Auswertung von 3D-Daten, 3D-NordOst, pages
15–26. GFaI e. V.
Wang, Y., Jin, C., and Zhang, Y. (2013). Pipe Defect Detec-
tion and Reconstruction Based on 3D Points Acquired
by the Circular Structured Light Vision. Advances in
Mechanical Engineering, 2013:670487.
Xie, Q., Li, D., Xu, J., Yu, Z., and Wang, J. (2019). Au-
tomatic Detection and Classification of Sewer Defects
via Hierarchical Deep Learning. IEEE Transactions
on Automation Science and Engineering, 16(4):1836–
1847.
Zhang, R., Evans, M. H., Worley, R., Anderson, S. R., and
Mihaylova, L. (2021). Improving SLAM in pipe net-
works by leveraging cylindrical regularity. TAROS
2021: Towards Autonomous Robotic Systems.
Zhang, Y., Hartley, R., Mashford, J., Wang, L., and Burn, S.
(2011). Pipeline Reconstruction from Fisheye Images.
J. WSCG, 19:49–57.
VISAPP 2023 - 18th International Conference on Computer Vision Theory and Applications
1006