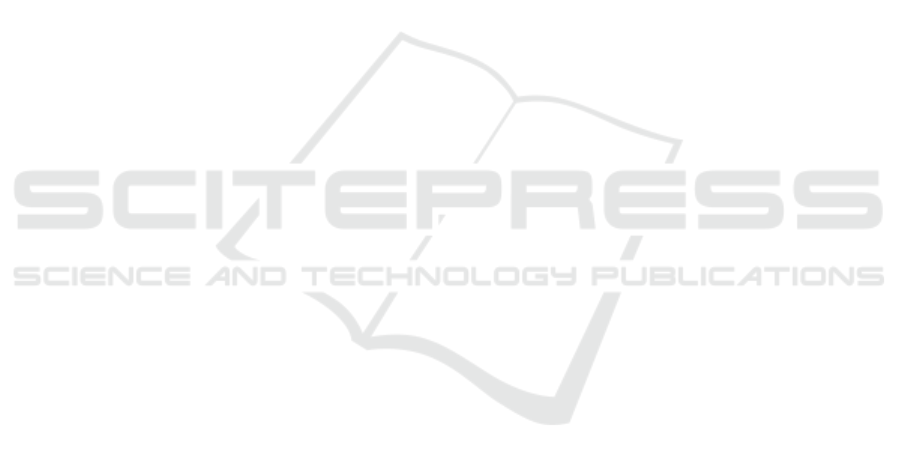
and contributions of this work are presented. Then,
in Section 5 different experiments of the approach are
exposed. Finally, in Section 6, some conclusions are
described.
2 RELATED WORKS
Nowadays, the manipulation of soft and flexible
pieces is a common research field which covers many
different kind of objects, as described in (Lahoud
et al., 2021), where authors developed a robotic sys-
tem to manipulate fabric clothes to perform the stitch-
ing task. Similarities can be observed in relation to the
demoulding task, given that the precision required for
its execution must be exceptionally elevated. How-
ever, the stitching task does not require high forces
and it is more difficult to damage or to break the ob-
ject, in contrast to the demoulding task.
In (Navarro-Alarcon et al., 2016), it is presented
an automatic method to compute the parameters of
the deformation model of the soft object in real time
with an external camera. They prepared a clear set-
up where the piece is always visible. However, in
our use case, the soft piece is inside the mould and
when the robot is demoulding it, the piece is occlud-
ing all possible views, so it is needed to estimate the
applied force before the performance of the task. In
(Ubeda et al., 2021), authors present a development
based on a collaborative robotic system able to per-
form sanding tasks using a force control loop with the
feedback of a force sensor. Force control is an impor-
tant fact when manipulating soft objects, but they ap-
plied the sanding task to rigid materials, so they had
not to worry about deformations. In (Ortenzi et al.,
2018), a vision-based manipulation system of plas-
tic objects was developed. In that paper, it is sum-
marized clearly the challenges of the manipulation of
soft pieces: the lack of deformation models for the
pieces, the difficulty to perform a visual tracking, and
the drawbacks to generate inputs and outputs for the
visual error obtained. In addition, the paper describes
how to handle kinetic sand whose dynamic model is
unknown. However, they manipulate the material in
the same temperature conditions, which makes easier
the estimation of the deformation model. In the case
of our approach, the deformation level depends on the
temperature of the pieces which varies a lot during the
extraction.
Regarding the manipulation of soft objects, there
are many different applications. In (Herguedas et al.,
2019), authors classify soft objects in groups depend-
ing on the deformation model used, dimension of
the object, the control strategy followed, perception-
based classification and predominant actions they
deal with. In this description, the use case faced in
this paper is classified in some of the most compli-
cated groups because we are handling 3D shaped ob-
jects with no previous deformation model and the per-
ception system is only about the feedback force of the
own robot due to the occlusions during the task. To
solve problems related to the lack of knowledge about
the deformation model, in (Navarro-Alarc
´
on et al.,
2013), authors propose a vision-based method to
servo control the deformation of a deformable object
applying a model-free method that estimates the ob-
ject’s deformation Jacobian matrix in real time. They
detect some points of interest of the piece to carry out
the manipulation. However, this work presents the
same drawback regarding the field of view and the
approach does not face the problem of partially oc-
cluded objects as in this case, and it is necessary to
control the force without any visual feedback.
In contrast to the classic control methods to ap-
ply force during the robot manipulation, in (Lin et al.,
2019) authors present a safe control system based on
Reinforcement Learning and force sensors to improve
the control and to avoid dangerous and unpredictable
situations, especially in the simulation - real world
transition. Implementing this kind of algorithms is
really useful to obtain general solutions; however, sta-
bility and reliability are not usually guaranteed. The
problem of this work is clearly delimited, so the accu-
racy, stability and repeatability of the trajectories are
priority. Another similar case is explained in (Huang
et al., 2019), where authors apply Deep Reinforce-
ment Learning to improve the interaction between the
robot and fragile objects based on curiosity (reward-
ing the robot the exploring actions) in pushing tasks.
The main disadvantage of the possible application of
this system in our work is the penalization of large
forces its algorithm uses to learn, because the avail-
ability of huge forces are really important for us, as
will be explained in the following sections. Main dis-
advantage is the penalization of large forces, which
are important parameters to consider for the develop-
ment of this work.
In conclusion, nowadays there are many contribu-
tions related to the manipulation of deformable ob-
jects, integration of collaborative robots in industrial
environments and force controllers. However, cur-
rently, there is not any significant advance in a real in-
dustrial case which involves the robotic manipulation
of soft pieces with high force requirements in collab-
orative tasks of the toy manufacturing process. This
work aims to fill this gap and brings about a relevant
improvement in this sector.
RoboToy Demoulding: Robotic Demoulding System for Toy Manufacturing Industry
547