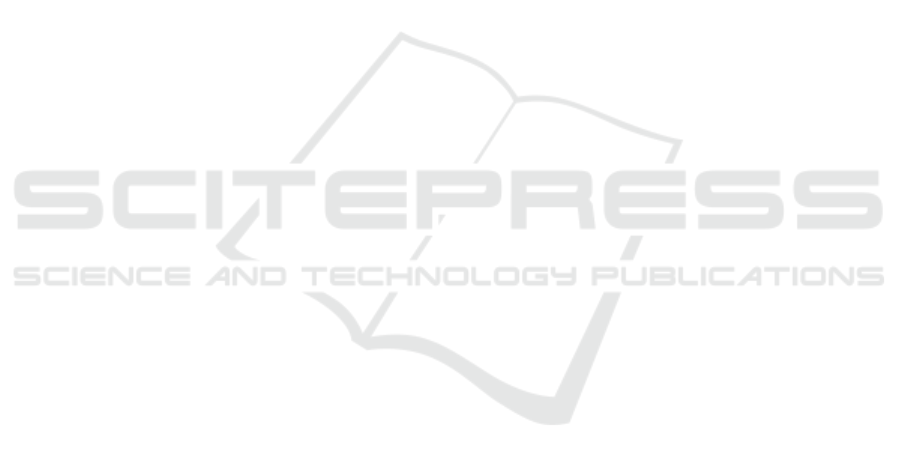
ACKNOWLEDGEMENTS
The contribution of this paper was written as part
of the joint project newAIDE under the consortium
leadership of BMW AG with the partners Altair En-
gineering GmbH, divis intelligent solutions GmbH,
MSC Software GmbH, Technical University of Mu-
nich, TWT GmbH. The project is supported by the
Federal Ministry of Economics and Energy (BMWi)
on the basis of a decision of the German Bundestag.
REFERENCES
Achlioptas, P., Diamanti, O., Mitliagkas, I., and Guibas, L.
(2018). Learning representations and generative mod-
els for 3d point clouds. In Dy, Krause (Hg.) 2018 –
Proceedings of the 35th International Conference on
Machine Learning, volume 80, pages 40–49.
Bai, J., Gao, S., Tang, W., Liu, Y., and Guo, S. (2010).
Design reuse oriented partial retrieval of cad models.
Computer-Aided Design, 42(12):1069–1084.
Bickel, S., Schleich, B., and Wartzack, S. (2023). A novel
shape retrieval method for 3d mechanical components
based on object projection, pre-trained deep learning
models and autoencoder. Computer-Aided Design,
154:103417.
Bustos, B., Keim, D. A., Saupe, D., Schreck, T., and Vrani
´
c,
D. V. (2005). Feature-based similarity search in 3d ob-
ject databases. ACM Computing Surveys, 37(4):345–
387.
Hanocka, R., Hertz, A., Fish, N., Giryes, R., Fleishman, S.,
and Cohen-Or, D. (2019). Meshcnn: A network with
an edge. ACM Transactions on Graphics, 38(4):1–12.
Hong, T., Lee, K., and Kim, S. (2006). Similarity com-
parison of mechanical parts to reuse existing designs.
Computer-Aided Design, 38(9):973–984.
Ji, B., Zhang, J., Li, Y., and Pang, J. (2023). Free-form cad
model retrieval approach for engineering reuse based
on local feature segmentation. Computers & Graph-
ics, 111:111–121.
Krahe, C., Marinov, M., Schmutz, T., Hermann, Y., Bonny,
M., May, M., and Lanza, G. (2022). Ai based geo-
metric similarity search supporting component reuse
in engineering design. Procedia CIRP, 109:275–280.
Li, M., Zhang, Y. F., Fuh, J., and Qiu, Z. M. (2011). De-
sign reusability assessment for effective cad model re-
trieval and reuse. International Journal of Computer
Applications in Technology, 40(1/2):3.
Ma, W., Wang, P., Cai, D., and Wang, D. (102019). Re-
search on 3d cad model retrieval algorithm based on
global and local similarity. In 2019 IEEE Interna-
tional Conferences on Ubiquitous Computing & Com-
munications (IUCC) and Data Science and Computa-
tional Intelligence (DSCI) and Smart Computing, Net-
working and Services (SmartCNS), pages 349–355.
IEEE.
Maturana, D. and Scherer, S. (9/28/2015 - 10/2/2015).
Voxnet: A 3d convolutional neural network for real-
time object recognition. In 2015 IEEE/RSJ Interna-
tional Conference on Intelligent Robots and Systems
(IROS), pages 922–928. IEEE.
Muffatto, M. (1999). Introducing a platform strategy in
product development. International Journal of Pro-
duction Economics, 60-61:145–153.
Qi, C. R., Su, H., Mo, K., and Guibas, L. J. (2017). Pointnet:
Deep learning on point sets for 3d classification and
segmentation. In Proceedings of the IEEE Conference
on Computer Vision and Pattern Recognition (CVPR).
Saha, S., Rios, T., Minku, L., van Stein, B., Wollstadt,
P., Yao, X., B
¨
ack, T., Sendhoff, B., and Menzel, S.
(2021). Exploiting generative models for performance
predictions of 3d car designs. In IEEE Symposium Se-
ries on Computational Intelligence (IEEE SSCI 2021).
IEEE.
Shi, W. and Rajkumar, R. (2020). Point-gnn: Graph neural
network for 3d object detection in a point cloud. In
The IEEE Conference on Computer Vision and Pattern
Recognition (CVPR).
Starly, B., Lau, A., Sun, W., Lau, W., and Bradbury, T.
(2005). Direct slicing of step based nurbs models
for layered manufacturing. Computer-Aided Design,
37(4):387–397.
Su, H., Maji, S., Kalogerakis, E., and Learned-Miller, E.
(12/7/2015 - 12/13/2015). Multi-view convolutional
neural networks for 3d shape recognition. In 2015
IEEE International Conference on Computer Vision
(ICCV), pages 945–953. IEEE.
Tao, S., Huang, Z., Ma, L., Guo, S., Wang, S., and Xie,
Y. (2013). Partial retrieval of cad models based on
local surface region decomposition. Computer-Aided
Design, 45(11):1239–1252.
Xu, X., Peng, W., Cheng, C.-Y., Willis, K. D., and Ritchie,
D. (62021). Inferring cad modeling sequences using
zone graphs. In 2021 IEEE/CVF Conference on Com-
puter Vision and Pattern Recognition (CVPR), pages
6058–6066. IEEE.
Yang, Y., Feng, C., Shen, Y., and Tian, D. (2018). Fold-
ingnet: Point cloud auto-encoder via deep grid defor-
mation. In 2018 IEEE/CVF Conference on Computer
Vision and Pattern Recognition (CVPR 2018), pages
206–215, Piscataway, NJ. IEEE.
Zehtaban, L. and Roller, D. (2013). Beyond similarity
comparison: Intelligent data retrieval for cad/cam
designs. Computer-Aided Design and Applications,
10(5):789–802.
Zhu, Z., Wang, X., Bai, S., Yao, C., and Bai, X. (2016).
Deep learning representation using autoencoder for 3d
shape retrieval. Neurocomputing, 204:41–50.
Zhuang, T., Zhang, X., Hou, Z., Zuo, W., and Liu, Y. (2017).
A novel 3d cad model retrieval method based on ver-
tices classification and weights combination optimiza-
tion. Mathematical Problems in Engineering, 2017:1–
12.
A Flexible Approach for Retrieving Geometrically Similar Finite Element Models Using Point Cloud Autoencoders
195