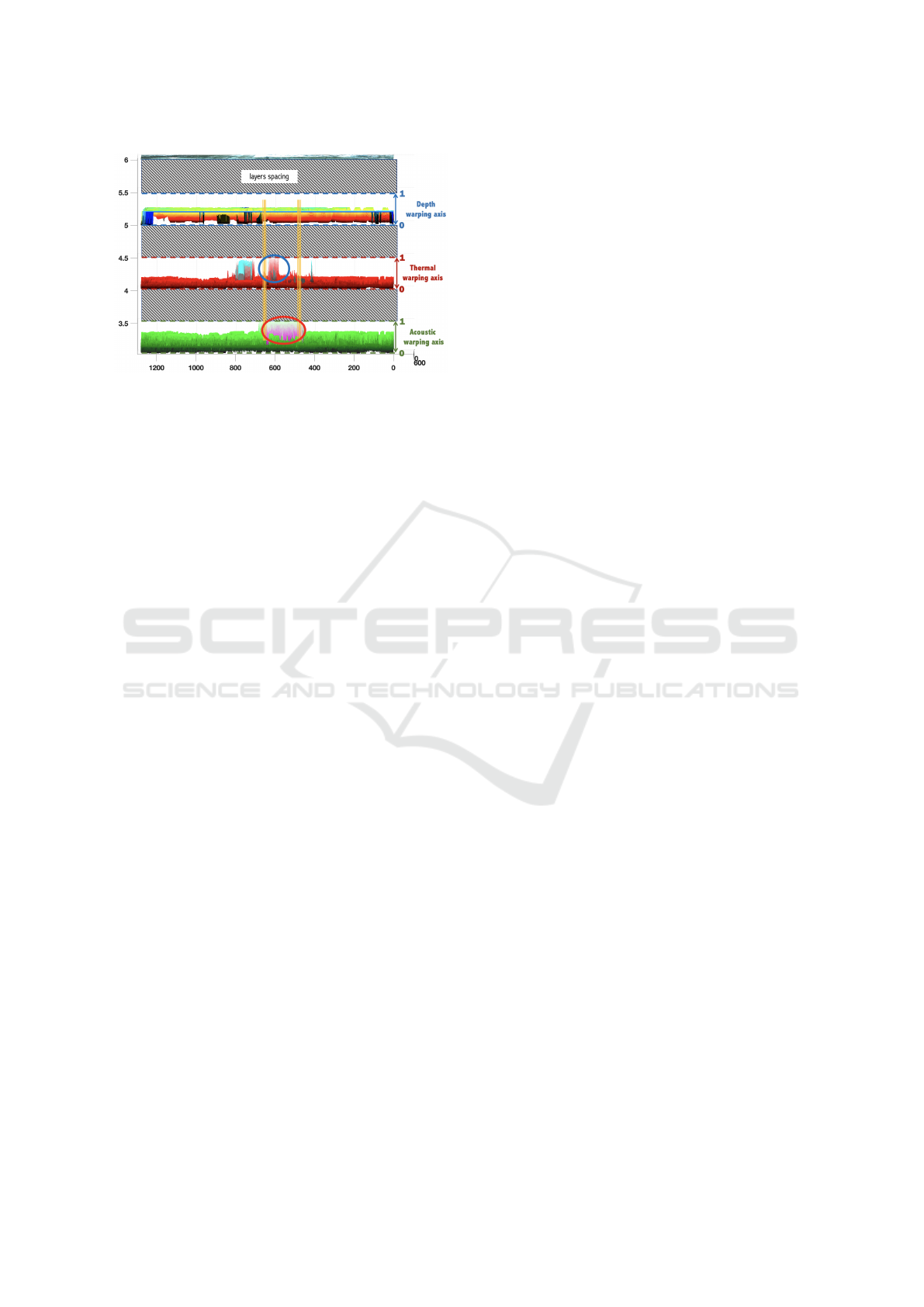
Figure 12: X-Z overview of MultiSpectrum Inspection
Map.
spectra, thereby enabling more reliable inspections
and predictive maintenance. The system has been de-
signed for and expected to be incorporated into cable
inspection robots and moves over cables to provide a
direct point of view of transmission line components.
Future works will discuss the analysis of the Multi-
Spectrum inspection map to determine faults, dam-
ages and to predict future issues.
ACKNOWLEDGEMENTS
The project is supported by National Council for
Scientific and Technological Development – CNPq
(process CNPq 407984/2022-4); Fund for Scientific
and Technological Development – FNDCT; Ministry
of Science, Technology and Innovations – MCTI of
Brazil; Araucaria Foundation; and the General Super-
intendence of Science, Technology and Higher Edu-
cation (SETI).
REFERENCES
Acharya, T. and Tsai, P.-S. (2007). Computational foun-
dations of image interpolation algorithms. Ubiquity,
2007(October):4–1.
Boufares, F., Doudech, I., and Bahrami, M. R. (2022).
Electrical transmission lines robot inspector: Design
challenges. In 2022 International conference on in-
dustrial engineering, applications and manufacturing
(ICIEAM), pages 746–754. IEEE.
Cantieri, A., Ferraz, M., Szekir, G., Ant
ˆ
onio Teix-
eira, M., Lima, J., Schneider Oliveira, A., and
Aur
´
elio Wehrmeister, M. (2020). Cooperative uav–
ugv autonomous power pylon inspection: An investi-
gation of cooperative outdoor vehicle positioning ar-
chitecture. Sensors, 20(21):6384.
FLIR (2022). Using acoustic imaging for partial discharge
monitoring. https://www.flir.com/discover/industrial/
using-acoustic-imaging-for-partial-discharge-monitoring/.
Last checked on Jun 04, 2023.
Gonc¸alves, R. S., Souza, F. C., Homma, R. Z., Sud-
brack, D. E. T., Trautmann, P. V., and Clasen, B. C.
(2022). Robots for inspection and maintenance of
power transmission lines. In Robot Design: From The-
ory to Service Applications, pages 119–142. Springer.
Hu, Y. and Liu, K. (2017). Inspection and monitoring tech-
nologies of transmission lines with remote sensing.
Academic Press.
Ji, H., Lei, X., Xu, Q., Huang, C., Ye, T., and Yuan, S.
(2022). Research on characteristics of acoustic signal
of typical partial discharge models. Global Energy
Interconnection, 5(1):118–130.
Jin, Y., Quan, M., Yan, S., Yan, Y., Cui, M., and Liu,
Y. (2020). Analysis of overhead transmission lines
fusing failure due to poor contact between conduc-
tors and clamps. Engineering Failure Analysis,
118:104858.
Li, Z., Zhang, Y., Wu, H., Suzuki, S., Namiki, A., and
Wang, W. (2023). Design and application of a uav
autonomous inspection system for high-voltage power
transmission lines. Remote Sensing, 15(3):865.
NLAcoustics (2022). Partial discharges: Who needs
to detect them and why? https://nlacoustics.com/
partial-discharges-who-needs-to-detect-them-and-why.
Last checked on Jun 04, 2023.
Pihera, J., Hornak, J., Trnka, P., Turecek, O., Zuzjak, L.,
Saksela, K., Nyberg, J., and Albrecht, R. (2020).
Partial discharge detection using acoustic camera.
In 2020 IEEE 3rd International Conference on Di-
electrics (ICD), pages 830–833. IEEE.
Raymond, W. J. K., Illias, H. A., Mokhlis, H., et al. (2015).
Partial discharge classifications: Review of recent
progress. Measurement, 68:164–181.
Souza, B. J., Stefenon, S. F., Singh, G., and Freire, R. Z.
(2023). Hybrid-yolo for classification of insulators
defects in transmission lines based on uav. Interna-
tional Journal of Electrical Power & Energy Systems,
148:108982.
Stolper, R., Hart, J., and Mahatho, N. (2005). The de-
sign and evaluation of a multi-spectral imaging cam-
era for the inspection of transmission lines and sub-
station equipment. In World Insulator Congress and
Exhibition, Hong Kong, China.
Stone, G. C., Sasic, M., Wendel, C., and Shaikh, A. (2021).
Initial experience with acoustic imaging of pd on high
voltage equipment. In 2021 IEEE Electrical Insula-
tion Conference (EIC), pages 13–17. IEEE.
Teixeira, M. A. S., Neves-JR, F., Koubaa, A., de Arruda,
L. V. R., and de Oliveira, A. S. (2020). Deepspatial:
Intelligent spatial sensor to perception of things. IEEE
Sensors Journal, 21(4):3966–3976.
Wang, B., Ren, M., Xia, C., Li, Q., Dong, M., Zhang, C.,
Guo, C., Liu, W., and Pischler, O. (2022a). Evalu-
ation of insulator aging status based on multispectral
imaging optimized by hyperspectral analysis. Mea-
surement, 205:112058.
Wang, Z., Gao, Q., Xu, J., and Li, D. (2022b). A re-
view of uav power line inspection. In Advances in
MultiSpectrum Inspection of Overhead Power Lines
125