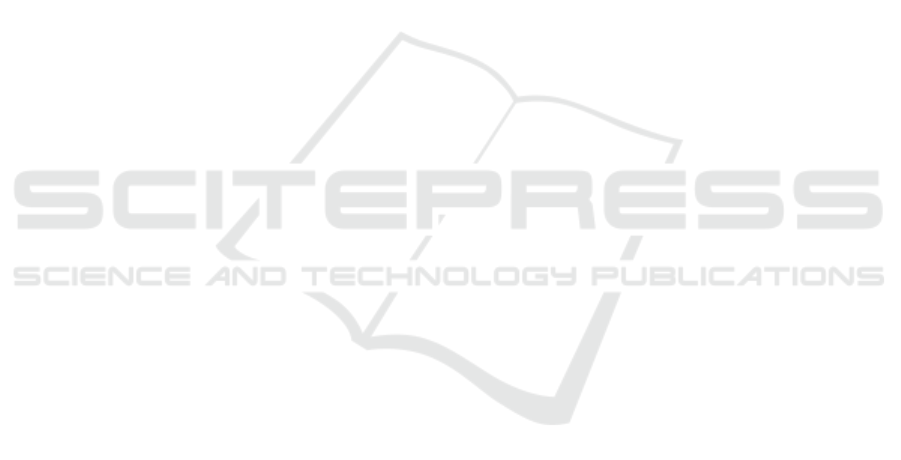
ical fault field and the data collected from the CWRU
rolling bearing data center, we extract the relation-
ship between entities and entities using a seven-step
process, store the obtained entities and inter-entity re-
lationships in the Neo4j graph database to complete
the construction of the bearing fault event knowledge
graph, and implement the four types of visual query
functions based on the constructed event kdb. Then,
we construct a deep convolutional neural network
with a wide convolutional kernel on the first layer
in order to diagnose the operational status of rolling
bearings. The experimentally established WDCNN
model has an accuracy rate of greater than 99.8% on
the training dataset and greater than 97.3% on the test
dataset. Finally, we predict bearing faults by com-
bining an event knowledge graph with a deep con-
volutional neural network. By acquiring newly col-
lected data during rolling bearing operation, setting
fault thresholds, and applying WDCNN to predict and
analyze them, new nodes and their relationships are
added to the event knowledge graph.
In rolling bearing fault diagnosis, the introduction
of the event knowledge graph and convolutional neu-
ral network provides support for fault diagnosis and
prediction, enhances the accuracy of fault diagnosis
and prediction, and reduces the need for expertise and
expert system domain knowledge.
ACKNOWLEDGEMENTS
This work is supported by the National Natural Sci-
ence Foundation of China (62002207, 62072290,
62073201), the Shandong Provincial Natural Sci-
ence Foundation (ZR2022YQ05, ZR2020MA102)
and Shandong Provincial Key Laboratory for Novel
Distributed Computer Software Technology.
REFERENCES
An, M. (2008). A survey on fault diagnosis expert systems.
Computer Measurement & Control, 16(9):3.
CWRU (2023). Case western reserve university bearing
data center. accessed on March 11, 2023.
Fern
´
andez-L
´
opez, M., Gomez-Perez, A., and Juristo, N.
(1997). Methontology: Fromontological art towards
ontological engineering. Proceedings of International
Conference on Software, Services & Semantic tech-
nologies, pages 33 – 40.
Gomez-Perez, A. and Su
´
arez-Figueroa, M. C. (2009).
Neon methodology for building ontology networks: a
scenario-based methodology. Proceedings of Interna-
tional Conference on Software, Services & Semantic
technologies.
Han, Y.-J., Park, S.-Y., Park, S.-B., Lee, Y.-H., and Kim,
K.-Y. (2007). Reconstruction of people informa-
tion based on an event ontology. In 2007 Interna-
tional Conference on Natural Language Processing
and Knowledge Engineering, pages 446–451.
Krizhevsky, A., Sutskever, I., and Hinton, G. (2012). Im-
agenet classification with deep convolutional neural
networks. Advances in neural information processing
systems, pages 1097–1105.
Liu, X. (2019). Research on Knowledge Graph Construc-
tion Technology for Fault Analysis. PhD thesis, Bei-
jing University of Posts and Telecommunications.
Noy, N. and Mcguiness, D. (1995). A guide to creating your
first ontology. Biomedical Informatics Reseach, page
7–25.
Simonyan, K. and Zisserman, A. (2014). Very deep con-
volutional networks for large-scale image recognition.
Computer Science.
Szegedy, C., Liu, W., Jia, Y., Sermanet, P., Reed, S.,
Anguelov, D., Erhan, D., Vanhoucke, V., and Rabi-
novich, A. (2015). Going deeper with convolutions. In
2015 IEEE Conference on Computer Vision and Pat-
tern Recognition (CVPR), pages 1–9, Los Alamitos,
CA, USA. IEEE Computer Society.
Tian, L., Zhang, J., Zhang, J., Zhou, W., and Zhou, X.
(2021). Knowledge graph survey: representation, con-
struction, reasoning and knowledge hypergraph the-
ory. Journal of Computer Applications, 41(8):26.
Yan, W., Shi, Y., Wang, C., Zhang, L., and Wang, J.
(2022). Knowledge graph-based predictive mainte-
nance method and system for mechanical failures.
CN113887751A.
Yu Shi, Y. H. (2022). Mechanical fault diagnosis model
based on knowledge graph and fuzzy inference. Mod-
ern Information Technology, 6:72–76+81.
Zeiler, M. D. (2012). ADADELTA: an adaptive learning
rate method. CoRR, abs/1212.5701.
Zhang, L., Wang, Z., and Zhao, S. (2007). Short-term fault
prediction of mechanical rotating parts on the basis of
fuzzy-grey optimising method. Mechanical Systems
and Signal Processing, 21(2):856–865.
Zhang, W. (2017). Study on Bearing fault Diagnosis Algo-
rithm Based on Convolutional Neural Network. PhD
thesis, Harbin Institute of Technology.
Zhao, X., Wang, W., Li, L., and Xu, Y. (2022). Framework
design and improvement about knowledge graph con-
struction in dynamic military field. In Proceedings
of the 10th China Command and Control Conference
(Previous), pages 212–217.
Mechanical Fault Prediction Based on Event Knowledge Graph
173