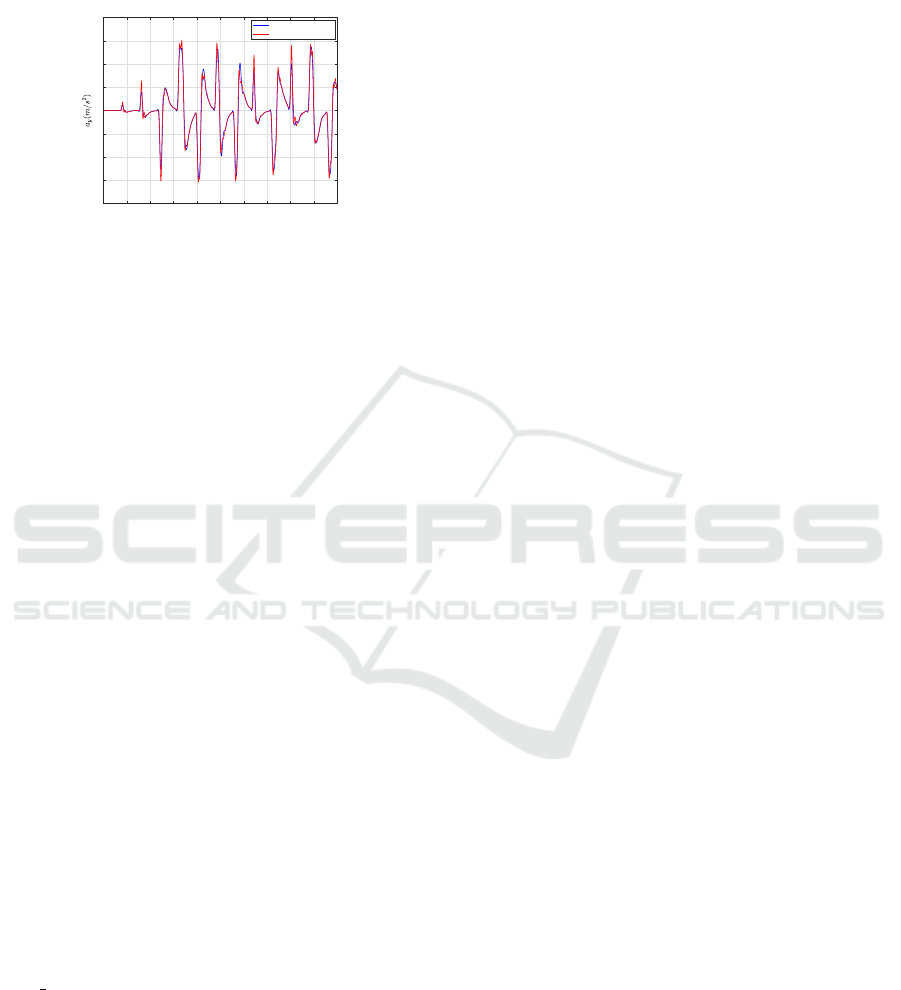
Finally, the lateral accelerations are presented. It
can be seen, the maximum value of the acceleration
reaches 3m/s
2
, which is an appropriate value for ev-
eryday traffic situations.
10 20 30 40 50 60 70 80 90 100 110
Simulation time (s)
-4
-3
-2
-1
0
1
2
3
4
Dynamical MPC
Kinematic MPC + UL
Figure 8: Lateral accelerations during the test scenarios.
6 CONCLUSIONS
The paper has presented a novel control design ap-
proach, which took the advantages of low computa-
tional cost MPC and error-based ultra-local model.
The proposed control algorithm was able to guarantee
a high-performance level and to take into account the
state constraints of the system. The efficiency and the
operation of the proposed method have been demon-
strated through a vehicle-oriented control problem,
trajectory tracking. The designed controller has been
compared to a high-computational cost MPC to show
the performance level of the presented algorithm. The
comparison has been carried out in the high-fidelity
simulation software, CarMaker.
ACKNOWLEDGEMENTS
The research was supported by the European Union
within the framework of the National Laboratory for
Autonomous Systems (RRF-2.3.1-21-2022-00002).
The paper was partially funded by the National Re-
search, Development and Innovation Office under
OTKA Grant Agreement No. K 143599. The research
was also supported by the National Research, De-
velopment and Innovation Office through the project
”Cooperative emergency trajectory design for con-
nected autonomous vehicles” (NKFIH: 2019-2.1.12-
T
´
ET VN).
REFERENCES
Allg
¨
ower, F., Findeisen, R., and Nagy, Z. (2004). Nonlinear
model predictive control: From theory to application.
Journal of The Chinese Institute of Chemical Engi-
neers, 35:299–315.
Barth, J. M., Condomines, J.-P., Bronz, M., Moschetta, J.-
M., Join, C., and Fliess, M. (2020). Model-free con-
trol algorithms for micro air vehicles with transition-
ing flight capabilities. International Journal of Micro
Air Vehicles, 12.
Batista, J. G., Souza, D. A., dos Reis, L. L., Filgueiras,
L. V., Ramos, K. M., Junior, A. B., and Correia, W. B.
(2019). Performance comparison between the PID
and LQR controllers applied to a robotic manipula-
tor joint. In IECON 2019 - 45th Annual Conference
of the IEEE Industrial Electronics Society, volume 1,
pages 479–484.
Camacho, E. F. and Bordons, C. (2007). Model predictive
control. Springer London.
Fliess, M. and Join, C. (2013). Model-free control. Inter-
national Journal of Control, 86(12):2228–2252.
Ghazally I. Y. Mustafa, Haoping Wang, Y. T. (2019).
Model-free adaptive fuzzy logic control for a half-car
active suspension system. Studies in Informatics and
Control, 28.
Heged
˝
us, T., F
´
enyes, D., N
´
emeth, B., Szab
´
o, Z., and
G
´
asp
´
ar, P. (2022). Design of model free control with
tuning method on ultra-local model for lateral vehicle
control purposes. pages 4101–4106.
Heged
˝
us, T., F
´
enyes, D., Szab
´
o, Z., N
´
emeth, B., Luk
´
acs,
L., Csikja, R., and G
´
asp
´
ar, P. (2023). Implementation
and design of ultra-local model-based control strategy
for autonomous vehicles. Vehicle System Dynamics,
0(0):1–24.
Katriniok, A. and Abel, D. (2011). LTV-MPC approach for
lateral vehicle guidance by front steering at the limits
of vehicle dynamics. In 2011 50th IEEE Conference
on Decision and Control and European Control Con-
ference, pages 6828–6833.
Lima, P. F., Trincavelli, M., Martensson, J., and Wahlberg,
B. (2015). Clothoid-based model predictive control
for autonomous driving. In 2015 European Control
Conference (ECC), pages 2983–2990.
Mondek, M. and Hrom
ˇ
c
´
ık, M. (2017). Linear analysis of
lateral vehicle dynamics. In 2017 21st International
Conference on Process Control (PC), pages 240–246.
Polack, P., Altch
´
e, F., d
´
Andr
´
ea Novel, B., and
de La Fortelle, A. (2017). The kinematic bicycle
model: A consistent model for planning feasible tra-
jectories for autonomous vehicles? 2017 IEEE Intel-
ligent Vehicles Symposium (IV), pages 812–818.
Polack, P., Delprat, S., and d
´
Andr
´
ea Novel, B. (2019).
Brake and velocity model-free control on an actual ve-
hicle. Control Engineering Practice, 92:104072.
Rajamani, R. (2005). Vehicle dynamics and control.
Springer.
Schwenzer, M., Ay, M., and Abel, D. (2021). Review on
model predictive control: an engineering perspective.
The International Journal of Advanced Manufactur-
ing Technology, 117:1327–1349.
Wang, Z. and Wang, J. (2020). Ultra-local model predictive
control: A model-free approach and its application on
automated vehicle trajectory tracking. Control Engi-
neering Practice, 101:104482.
Zhou, K. and Doyle, J. C. (1998). Essentials of Robust Con-
trol. Prentice-Hall.
Lateral Control for Automated Vehicles Based on Model Predictive Control and Error-Based Ultra-Local Model
149