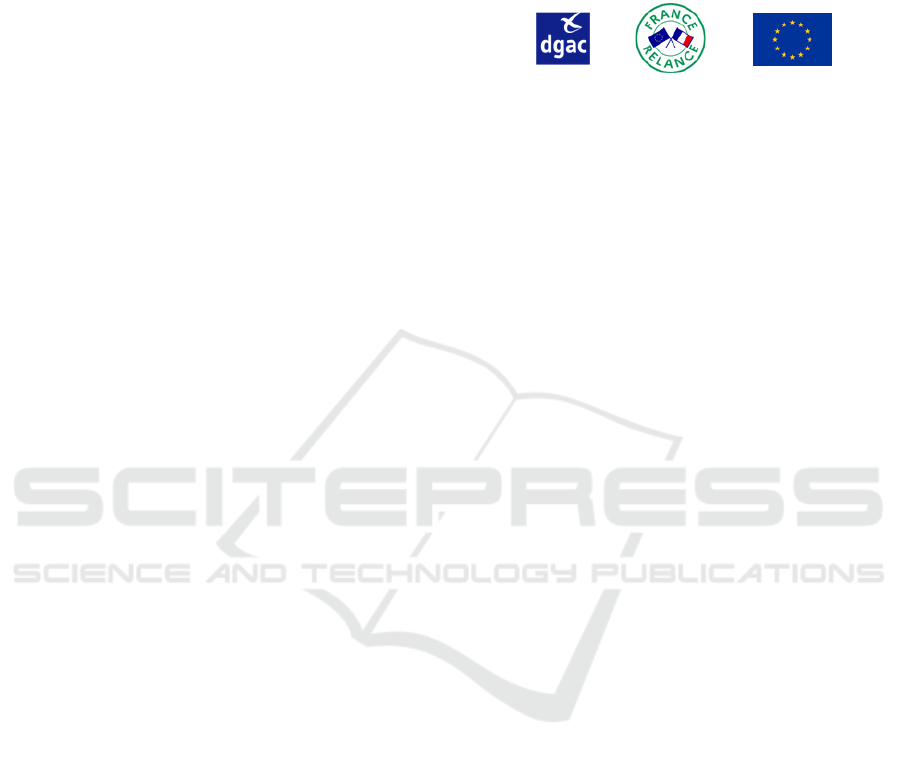
θ
1
∈ [−π; +π]. The cells q = (i, j) of the precom-
puted offline global inspection path Q are converted
into waypoints with coordinates
θ
w
z
w
ρ
w
=
i · δθ j · δz R (i · δθ, j · δz)
The path tracking performed by the robot is a
waypoint-based navigation method based on a uni-
cycle model. Thus, the robot aligns itself towards
the next waypoint by adjusting its yaw angle in the
2D plane with the angular set-point ψ
s
= atan2(z
w
−
z,ρ
w
· θ
w
− ρ
·
θ) using a proportional angular con-
troller. A velocity controller is then applied once the
angular error is below a small threshold. This control
logic leads to the expected correction in the 3D space
and the simulated robot model was successfully able
to track the inspection path on the surface of the air-
craft (Figure 10).
5 CONCLUSIONS AND
PERSPECTIVES
A method for planning a covering path on a curved
surface in the context of an automated inspection mis-
sion has been proposed in this paper. A 2D un-
folded model of this surface was established using
a parametrization of an input 3D model in cylindri-
cal coordinates. It was discretized to obtain two sur-
face functions, one describing the shape of the sur-
face and the other its semantics. Inspection segments
were sampled in this 2D space, taking into account
various constraints related to the robot. A method for
decomposing this discrete space into areas has been
defined to order these segments efficiently. Connec-
tion segments have been inserted between the inspec-
tion segments and calculated to pass through locations
that minimize the robot’s efforts using a weighted A∗
search procedure. This method has been tested nu-
merically on a representative aircraft 3D mesh where
the relevance of sorting the inspection path segments
by areas was demonstrated, and in a Gazebo simula-
tion with a simplified climbing robot model.
In the context of aircraft inspection, approximating
its surface with a cylindrical parametrization presents
some limitations, e.g. to exclude the wings in the
model. It would be interesting to investigate in fu-
ture work the extension of the path planning method
to surfaces of different shapes, or the possibility of di-
viding a 3D model into multiple sub-models that can
be individually approximated by a collection of geo-
metrical primitives.
ACKNOWLEDGMENTS
This research was partially supported by DGAC
France Relance project EXAM, in the frame of the
NextGenerationEU program.
REFERENCES
Acar, E. U., Choset, H., Rizzi, A. A., Atkar, P. N., and
Hull, D. (2002). Morse decompositions for cover-
age tasks. The International Journal of Robotics Re-
search, 21(4):331–344.
Achat, S., Marzat, J., and Moras, J. (2022). Path planning
incorporating semantic information for autonomous
robot navigation. In 19th International Conference
on Informatics in Control, Automation and Robotics
(ICINCO), Lisbonne, Portugal.
Andrikopoulos, G., Papadimitriou, A., Brusell, A., and
Nikolakopoulos, G. (2019). On model-based adhesion
control of a vortex climbing robot. In IEEE/RSJ In-
ternational Conference on Intelligent Robots and Sys-
tems (IROS), pages 1460–1465.
B
¨
ahnemann, R., Lawrance, N., Chung, J. J., Pantic, M.,
Siegwart, R., and Nieto, J. (2021). Revisiting boustro-
phedon coverage path planning as a generalized trav-
eling salesman problem. In 12th International Confer-
ence on Field and Service Robotics, pages 277–290.
Bugaj, M., Nov
´
ak, A., Stelmach, A., and Lusiak, T. (2020).
Unmanned aerial vehicles and their use for aircraft
inspection. In 2020 New Trends in Civil Aviation
(NTCA), pages 45–50.
Chang, F., Chen, C.-J., and Lu, C.-J. (2004). A linear-time
component-labeling algorithm using contour tracing
technique. Computer Vision and Image Understand-
ing, 93:206–220.
Chen, H., Fuhlbrigge, T., and Li, X. (2008). Automated
industrial robot path planning for spray painting pro-
cess: A review. In IEEE International Conference on
Automation Science and Engineering, pages 522–527.
Choset, H. and Pignon, P. (1998). Coverage path planning:
The boustrophedon cellular decomposition. In Field
and service robotics, pages 203–209.
Dahiya, C. and Sangwan, S. (2018). Literature review on
travelling salesman problem. International Journal of
Research, 5:1152–1155.
Fernandez, R. F., Keller, K., and Robins, J. (2016). Design
of a system for aircraft fuselage inspection. In IEEE
Systems and Information Engineering Design Sympo-
sium, pages 283–288.
Gabriely, Y. and Rimon, E. (2001). Spanning-tree based
coverage of continuous areas by a mobile robot. An-
nals of mathematics and artificial intelligence, 31:77–
98.
ICINCO 2023 - 20th International Conference on Informatics in Control, Automation and Robotics
442